Synthetic covers include polyethylene (PE) tarps, flexible vinyl fabrics, PE fleece blankets and expanded polytetrafluoroethylene. Covers are used with both forced and induced aeration. Part III
Craig Coker and Tom Gibson
BioCycle May 2013, Vol. 54, No. 5, p. 21
This series of articles has established that aerated static pile (ASP) composting is increasing in the U.S. composting industry due to the potential for better process and odor control and, when covered, for potential improvements in odor management and storm water runoff quality. The last article in this three-part series focuses on covers.
Equipping a composting pile with a cover, whether made of carbonaceous materials, compost or fabric, serves several purposes: Maintaining moisture levels by reducing evaporative losses; retaining heat in smaller piles and in colder climates; reducing the attraction of the pile to vectors; reducing odors either through in-situ biofiltration (compost cover) or water absorption of odorous molecules on the underside of the cover (fabric covers); preventing rainfall from contacting decomposing waste thus enabling runoff to be managed as storm water; and providing better visual appeal (many facility neighbors smell with their eyes). But the main attraction of covering ASPs is to reduce emissions of volatile organic compounds (VOCs), the primary source of odors and a regulated air pollutant in some places.
Pile covers are either biogenic or synthetic, with biogenic covers including compost (screened and unscreened), wood chips, sawdust, hay/straw and similar materials. The porosity of a biogenic cover greatly influences odor-reducing capability. Synthetic covers include polyethylene tarpaulins, flexible vinyl fabrics (recycled billboards), polyethylene fleece blankets, and expanded polytetrafluoroethylene (ePTFE) covers, although any water-repellent fabric cover will meet some of the goals. Truly impermeable synthetic covers do not allow for heat escape (excepting along boundaries between cover panels). Heat buildup can cause composting issues, such as inhibition of active composting above 160°F.
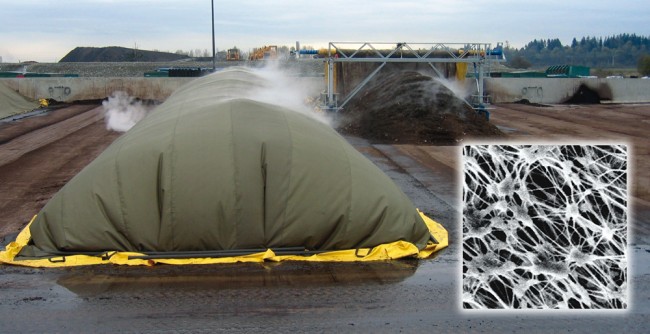
The Gore cover system uses fabric covers made of a layer of ePTFE (see close-up) sandwiched between two layers of polyester for structure.
Micropore Covers For Positive Aeration
Many new covered ASP systems in North America are based on the use of microporous ePTFE, an extruded sheet-form version of the carbon-fluorine compound that forms the basis for DuPont’s Teflon. This application has been utilized in Europe for over 15 years. W.L. Gore & Associates uses this material in its Gore-Tex fabric found in clothing such as ski jackets, which are known for being breathable yet waterproof. Gore’s composting system offers fabric covers made of a layer of ePTFE sandwiched between two layers of polyester for structure. The ePTFE has pore sizes between 0.02 micron (Ìm) and 40 µm.
Brian Fuchs, an associate at Gore, explains that moisture control plays a big role in making their cover very suitable for positive aeration systems. “The moisture is retained within our covered system because the air is blowing upward and using the inherent properties of the membrane to keep the moisture in the system, as compared to a negatively aerated system that’s drawing the air down and pulling the moisture out with it, which then ends up either in a condenser or the biofilter.”
Managed Organic Recycling (MOR) also bases its Compost Cover System on ePTFE fabric. “Our covers are primarily designed for VOC control now because of the California requirements,” explains John Bouey, president of MOR. The company is starting to see demand for covers in other states besides California, which are copying the Golden State’s regulations.
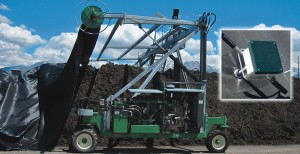
Managed Organic Recycling custom builds its Cover Placement Machine to handle its ePTFE fabric covers. Temperature monitoring (closeup) is on 5-minute intervals.
A third company in the mix, Engineered Compost Systems (ECS), builds covers for both negative and positive aeration systems. Its AC Composter is an induced-draft system; there are 10 installed in the U.S. at present. Covers for negative aeration systems are made from a standard tarp material with larger holes up to one-sixteenth-inch in diameter. This keeps most of the rainwater out but allows adequate air flow, which is important because pulling air through a covered pile takes more power than pushing it. According to U.S. Patent No. 7,642,090, “the compost cover is formed of a material that is substantially gas and liquid impermeable, and is provided a plurality of aeration ports, or orifices, that permit the passage of gases through the cover. The size and number of aeration ports may be varied to meet the air flow requirements for given biomass, or feedstocks, zone size and process goals. The compost cover is generally constructed of fabric that is durable, flexible, UV resistant, waterproof, and relatively lightweight.”
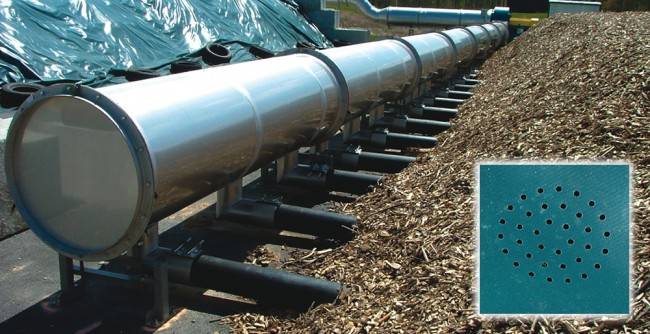
Engineered Compost Systems offers a negatively aerated cover system with process air treated in a biofilter. Its covers are made from a standard tarp material with larger holes up to one-sixteenth-inch in diameter (closeup).
Effect On Blower Pressure
Several design and operating factors should be considered with covers on ASP systems. Part 2 of this series (see “Pipe And Blower Fan Fundamentals In ASP Design,” February 2013) discussed calculating static pressure drop in ASP aeration systems in order to size the blower needed for supplying air to the pile. It stands to reason that a cover over a pile will add one more element in this process because air has to be forced through tiny pores in the tarp, increasing pressure drop and subsequently the blower size required. This can vary from one system to the next and by manufacturer, as they take different approaches.
Bouey says for positive aeration systems with 15 to 20 percent porosity in the pile, the cover adds 2 to 3 inches water gauge (W.G.) to the head loss. O’Neill notes that with the ECS covers, the added pressure drop is about 10 percent, or 0.5-inch W.G. over a cover measuring 40-feet wide by 100-feet long — “about the same increase you’d see in a biofilter due to settling over time.”
Blowers may actually operate on a reduced schedule, however. For example, Gore’s fabric-covered system uses oxygen content as the fan operational control variable, in addition to temperature. “We deliver air using our oxygen-controlled system, which offers greater control over the process by establishing oxygen set points based on the mix recipe,” explains Fuchs. “Essentially, we allow the microbes to determine the demand on oxygen, and our experience shows these set points could be as low as 2 percent and as high 18 percent. We use low-energy fans that generally operate only 25 percent of the time, which is a pure energy consumption advantage.”
MOR operates aeration blowers based on feedstock characteristics (i.e., average oxygen demand rates for some feedstock materials of about 750 cubic feet/hour (cfh)/dry ton organic matter in the mix and peak demand of 1,250 cfh/dry ton organic matter, assuming 8-inch pressure loss). Temperature monitoring is on 5-minute intervals and compared with control set points. Air flow rates are increased or decreased to maintain the temperature within the set point. MOR systems run at temperatures between 155°F and 165°F in the active composting phase. Typically, this equates to blower run times between 3 to 5 minutes every 30 minutes.
According to Fuchs, the Gore system actually requires less blower pressure because it creates an encapsulated in-vessel system. “The cover is surrounded with a weighting system, which holds down the cover and allows the whole system to be pressurized,” he notes. “The membrane is specifically engineered with the trench and blower as one combined system.” The cover provides an even backpressure, resulting in an even distribution of resistance and air flow through the pile, and the blower works more efficiently.
With air pressure working against the underside of the cover, some mechanism is needed to hold the covers down. Options include sand bags, perforated truck tires, or perimeter water- or sand-filled anchoring tubes. Holding down a cover is important for two reasons: to keep fugitive emissions from leaking out around the base of the cover and to resist wind. “It is really important to secure them, especially because of wind,” says O’Neill. “The covers develop lift like a wing. You can imagine the force over 100 feet. They’re huge sails. We discourage them in windy areas.”
Another consideration with covered ASP systems is handling the covers. With smaller installations, the cover can be moved by hand, but larger ones are heavy and are usually moved onto and off the piles with machines like sidewinders, straddlewinders, winches or tractor-pulled winders. “We have different types, including a mobile winding machine, wall-mounted winders, and portable winders that are pulled with a trailer hitch behind a loader or pickup truck,” explains Fuchs. “We’ve worked with facilities that have front-end loader-mounted winders.” He adds that in Europe, Gore cover system installations include inflatable versions and mechanical roof-types of apparatus. MOR custom builds its Cover Placement Machines (CPM). It offers both two-wheel and all-wheel drive CPM with hydraulic “joy stick” control as well as a towable machine for smaller covers in the 30-foot by 90-foot range.
In conclusion, the main advantages of fabric-covered ASP composting, whether forced-draft or induced-draft, are control of VOCs for air quality reasons, improved moisture control in the aerated pile, and odor control through water absorption under the cover. Composters can choose biogenic covers that are replaced with every new pile, or consider one of these fabric-covered systems that can have an 8- to 10-year lifespan with careful maintenance.
Craig Coker is a Contributing Editor to BioCycle and a Principal in the firm Coker Composting & Consulting (www.cokercompost.com), near Roanoke VA. He can be reached at cscoker@verizon.net. A consulting mechanical engineer, Tom Gibson is president of Tom Gibson, P.E. Green Building Engineer (www.progressiveengineer.com/consulting.html) in Milton, PA and can be reached at tom@progressiveenginer.com.