Vermont farm adds new revenue stream by installing greenhouse heated with thermal energy from the digester engine.
Nora Goldstein
BioCycle February 2013, Vol. 54, No. 2, p. 33
Accompanying article: Farm Digester Evolution In Vermont
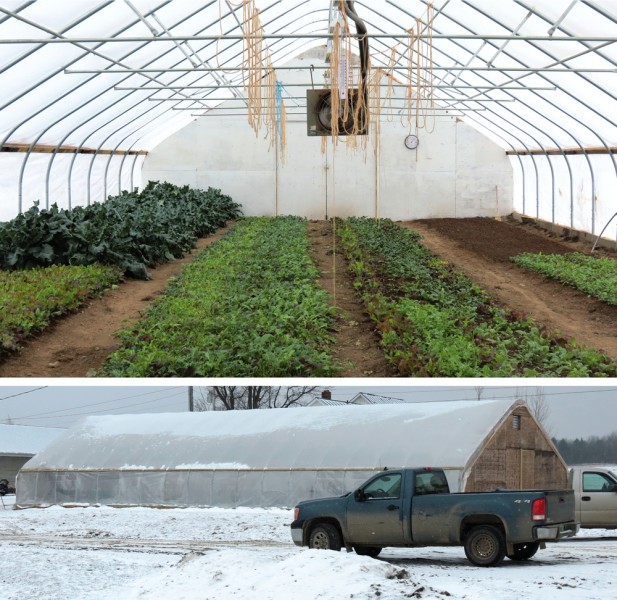
Neighborhood Farm is able to plant lettuce and cut greens for sale within three weeks. Radiant heat keeps the soil at 70° to 75°F
Neighborhood Farm in Newport, Vermont was started in 1957 by Maurice and Lois Maxwell. The dairy farm has 800 milking cows in a six row, fully insulated free stall barn. In 2008, Neighborhood Farms installed an anaerobic digester supplied by DVO Inc. (formerly GHD), along with a 225 kW Guascor (Martin Machinery) gas engine. Power is sold to Vermont Electric under the state’s SPEED standard offer feed-in tariff program. “We originally had a power purchase agreement directly with Vermont Electric, and when SPEED came along, we got rolled into the program at a slightly different rate than the current $0.14/kWh,” says Matthew Maxwell, grandson of the founders.
To increase biogas production, Neighborhood Farm receives about 14,000 gallons/week of fats, greases and oils from a food processor in Portland, Maine. The farm installed a 22,000-gallon in-ground precast concrete holding tank to receive off-farm substrates. “The material is very high in volatile solids so it is very good for electricity production,” notes Maxwell. “We add about 2,000 gallons at a time to the manure pit, where it is premixed before being loaded into the digester.”
When the digester was being constructed, Maxwell envisioned building a greenhouse that would be heated with the thermal energy captured from the engine generator. “We laid pipes in the ground from where the engine is to where we wanted the greenhouse to be,” he recalls. “And last August, we finally built the greenhouse and have been growing mixed greens and broccoli. We expect the capital costs to be paid for by the end of the winter growing season.”
Heat Capture
The pipes are buried far enough in the ground to not require insulation. Water, heated to about 180°F by heat captured from the engine, runs through the pipes that are under the raised beds in the greenhouse. The 36-foot wide by 72-foot long greenhouse accommodates three rows of raised beds. The radiant heat keeps the soil at 70 to 75°F; the temperature in the greenhouse is above 60°F. “That’s about as cool as it gets,” notes Maxwell. “And it is much warmer in the middle of the day when the sun is out. We did install some heaters in case supplemental heat is needed.”
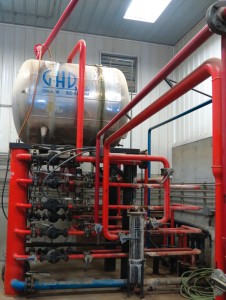
Water is heated to about 180°F by heat captured from the engine and stored in a tank that is part of the heat exchange system and pumped to various locations, including the greenhouse, as needed.
Right now, the greenhouse operation is producing about 30 lbs/week of mixed greens, which is sold to restaurants in the area. “No one else is growing greens right now in northern Vermont, so demand has been great,” he adds. “Next year, we will strictly grow spinach and lettuce because it grows quickly. We can plant lettuce and cut greens for sale within three weeks.”
Engine heat also is used to heat the farm maintenance shop, the milk house water and the flooring in the engine room. Separated solids are spread on the floor to dry them before using them as bedding for the cows. Neighborhood Farm composts a small amount (about 2 percent) of the solids in static piles. Compost is sold to landscaping companies and other greenhouses. The farm uses it in its raised beds as well.
Maxwell would like to receive additional off-farm substrates, including source separated food waste. The current rules are fairly stringent, he explains, and are based on the farm’s nutrient management plan, and whether capacity is available in the storage lagoon and on the land base (for managing the nutrients). “Food waste is so much better for producing electricity than manure, so we are exploring our options,” says Maxwell.
Total costs for the digester system and engine were about $2 million. A USDA grant covered 25 percent of the costs. About $425,000 was provided through grants from various state and utility funding programs. After four years of operating the digester, and six months of growing greens, Maxwell emphasizes the importance of capitalizing on the excess heat produced by the system. “Farmers need to think about how to generate separate revenue streams from the heat. And in my opinion, without off-farm substrates, it is difficult to pay back the capital cost of the digesters on manure only.”