Feasibility study supports a shift from the conventional CHP model to a renewable natural gas (RNG) model that takes advantage of the accelerating move to natural gas fuels in the transportation sector.
Nicholas Kennedy
BioCycle November 2013
Washington State is tenth in the nation in milk production, with its 420 commercial dairies producing more than 700 million gallons in 2011. Most of these dairy farms are located in two areas: the Northwest corner, where small and medium-sized dairies are the norm, and the Central region encompassing the Yakima River Valley and the Columbia Basin, home to the state’s largest dairies. Eight dairy digesters, using manure from about a dozen dairies, have been installed in Washington State since 2004 with the majority located in the upper Northwest corner (Figure 1). Only one project has been completed in the Central region, despite growing environmental concerns raised by the higher percentage of concentrated agricultural feeding operations (CAFOs).
Why is implementation of AD more prevalent in the Northwest corner of the state? Dan Evans, President of Promus Energy, cites three key barriers: “First, electrical power rates are traditionally among the lowest in the nation and have recently declined with an abundance of cheap natural gas. Second, regional utilities have not shown much interest in renewable energy and offer relatively low premiums for it, and third, nonmanure organic feedstocks (substrates) that boost biogas production and can garner a tipping fee are not as readily available compared to the more urbanized western part of Washington.”
In light of these barriers, the Washington State Department of Commerce funded a feasibility study to provide a better understanding of the hurdles facing the only digester currently operating in the Central region, the DeRuyter digester, and explore additional options that may increase the facility’s viability into the future. DeRuyter’s most recent power purchase agreement (PPA) expired at the end of 2012, resulting in a drop in power rates from $0.065 per kWh to $0.035 per kWh — clearly not good for business. The findings of the comprehensive feasibility study provide valuable information that private and/or public entities can use to pull together business plans and financing opportunities to further the development of AD both at the DeRuyter project and elsewhere in the Central region.
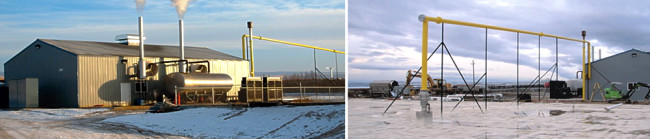
The George DeRuyter & Sons dairy digester processes around 175,000 gallons/day of concentrated manure from over 5,000 cows using a hybrid plug flow complete mix system designed by DVO, Inc. and Andgar Corp.
Baseline Numbers
Located in the Yakima River Valley near Outlook, the DeRuyter digester relies primarily on a flush manure feedstock from two dairies: George DeRuyter & Sons and D & A Farms. The digester is on the DeRuyter & Sons dairy and consists of a hybrid plug flow complete mix system designed by DVO, Inc. and Andgar Corp. It processes around 175,000 gallons/ day of concentrated manure from over 5,000 cows. Biogas is used to generate around 8.4 million kWh of electricity per year via two 600 kW combined heat and power (CHP) gensets. The total project cost was $3.9 million ($3.3 million for the digester, and $600,000 for other infrastructure) and paid for in part by George DeRuyter & Sons with additional assistance through grants and government loans — a $499,219 USDA 9006 grant and a Washington State BioEnergy Loan for $1,972,715 at an interest rate of 1 percent.
Heat is reclaimed from the engines to maintain the digester; fiber is separated after digestion, dried, and sold to Organix, a Walla Walla (WA) company that uses the fiber to produce a peat moss substitute. In addition, phosphorus-rich manure fines are collected in settling weirs and naturally dried for use as a soil amendment.
Revenue is generated from three major pathways: Electrical sales and associated credits/incentives; fiber and nutrients; and carbon credits. “In the past, the project relied heavily on electrical sales and the associated credits (renewable energy credits (RECs) and carbon credits) that were generated,” explains Craig Frear, an Assistant Professor at Washington State University (WSU) who was involved in the study. “However, recently the project’s revenue streams have altered due to foreseeable decreases in revenue from these sources, thus forcing the project to rely more heavily on revenue from nutrient sales.”
Unfortunately, this provides only a temporary and partial solution to the core problem of the DeRuyter project — diminishing returns from electrical generation. “In addition, RECs and carbon credits are volatile and preferably should not be relied upon as major sources of revenue,” adds Frear. “And in the case of this particular project, an unpaid debt load still remains.” Figure 2 details this baseline CHP Pro Forma, showing how the revenue streams will change over the years; Figure 3 illustrates the baseline pretax cash flow from 2012 to 2032 with changes in revenue streams and debt service.
Researchers from WSU’s Center for Sustaining Agriculture and Natural Resources (CSANR), the WSU Energy Program, Promus Energy, Scanlan Consulting and The Climate Trust (the principal feasibility study participants) investigated three Pro Formas beyond this baseline to determine the best case scenario for the DeRuyter project as well as other potential AD projects in the surrounding area. These included both increased electricity production, and renewable natural gas (RNG) options under several scenarios.
Non RNG Fuel Options
Transitioning away from electrical generation by selling the two gensets and installing a boiler to heat the digester was investigated for its effect on the pretax cash flow. This option saves on the high operation and maintenance costs associated with gensets, but as Frear explains, “results indicated that the current CHP operation would actually still produce more cash flow when compared to the boiler only operation.” Even with the lower PPA in 2013, CHP is more viable. “Therefore, this option is not advised over the current CHP mode,” he says.
Another non RNG option is to incorporate additional substrates (e.g. food scraps or grease trap waste) for codigestion to boost biogas production and electrical generation. Three scenarios were investigated: Substrate addition utilizing the two current 600 kW gensets (1.2 MW); substrate addition plus a brand new third generator (2 MW); and substrate addition plus a used third generator (2 MW). “Maintaining the two generators and increasing the biogas production via substrate addition resulted in a similar cash flow to the baseline scenario, while the most improvement upon the CHP model resulted from the addition of codigestion and a used third generator to boost electrical generation to 2 MW while at the same time saving money on capital costs,” notes Frear.
Electrical generation is greatly improved when substrates are included and electrical capacity is increased, but at the current PPA of $0.035/kWh, the debt service for a new genset (over $1 million with a 20 year payback period) completely offsets any additional revenue generated. On the other hand, purchase of a used genset (10% of the cost of a new one), the true benefits gained from the increase in power production can be realized. Frear does however recommend caution whenever considering codigestion as an option in the Columbia Basin due to the “unpredictability of acquiring substrates and the excess nutrients generated that would need to be incorporated into the farms nutrient management plans.”
RNG Under Three Price/Market Options
Three different price/market options were explored with RNG for AD projects in Washington. Biogas is cleaned of its impurities and can be injected into the natural gas pipeline grid or compressed into tube trailers and transported to truck fleets or other “off-takers.” “Even at half the retail price of diesel, RNG is worth many times the value of electricity produced by the same amount of biogas,” says Evans of Promus Energy. “When RECs are added to the commodity value of the RNG, it can even compete with cheap fossil natural gas as a vehicle fuel.” Because RNG can be marketed as a commodity (wholesale) or retail product and can capture valuable credits, three RNG scenarios were evaluated to compare to the baseline CHP Pro Forma: Commodity-only value; Commodity plus partial RIN (Renewable Identification Number) value; and Fast filling station value (retail compressed natural gas (CNG) plus full RIN value). Renewable CNG made from biogas is categorized as an advanced biofuel in the RIN market.
The commodity-only scenario assumed that DeRuyter receives 100 percent of the commodity or selling price of RNG by cleaning the biogas of impurities and injecting it directly into a natural gas pipeline. “No additional revenue is generated from RINs,” notes Evans. “A slightly lower cash flow than the baseline CHP scenario resulted, mainly due to all the added capital costs and debt services required for biogas cleaning, and pipeline and injection infrastructure.” Under the assumptions made in this study, the debt service (around $500,000 over a 20 year period) required for the capital/operation costs and delivery charge to the pipeline outweighed the revenue potential of selling biogas as natural gas.
However, the second scenario, commodity price plus RIN revenue (split between DeRuyter and the off-taker), was able to increase the revenue potential by selling the RNG as a transportation fuel and thus generating RIN values in addition to the commodity price. “RINs originated from the first Renewable Fuel Standard (RFS) established in the Energy Policy Act of 2005, and provide incentives to blend fuel derived from renewable sources into existing petroleum based fuels,” explains Peter Weisberg, a program manager at The Climate Trust in Portland, Oregon. Projects producing fuel from renewable sources use RINs to track compliance with RFS2, the current version of the standard. “The DeRuyter project can earn RINs if the project cleans and compresses biogas for use as vehicle fuel,” he adds.
Two RIN values were included in the feasibility study — a lower and more conservative RIN value of $0.25 ($0.37/gallon gasoline equivalent (GGE)) and a 2012 RIN value (RIN price at the time of the 2012 study) of $0.74 ($1.10/GGE). “The lower RIN value increased the cash flow above the CHP scenario by $141,000 in 2014 and $444,000 in 2032, while the 2012 RIN value increased the cash flow by $1.15 million in 2014 and $1.9 million in 2032,” says Weisberg. Figure 4 compares the pretax cash flows. In both scenarios the potential revenue gain is substantial, especially at the 2012 RIN value. RIN proponents note it would take both houses of Congress and the President to eliminate the RFS2 RIN program, providing some security for this market into the future. However, market strategists like Weisberg recommend caution: “RINs are volatile and hard to predict, thus making it difficult to finance a project that relies too heavily on the RIN.”
The third scenario, fast fill station, assumes that the RNG is sold at or near the retail value of CNG. Biogas would be upgraded and piped to a CNG fueling station in close proximity to the DeRuyter project, compressed and sold to the public. Infrastructure upgrades are required on top of the already heavy capital and operating costs but since RINs are also generated, a significant improvement in cash flow results compared to all other business models investigated in this study. “When RNG is sold with associated RIN values, the revenue potential is very encouraging from a business standpoint, especially when a fast filling station is constructed at or near truck fleets,” says Jim Jensen, Senior Bioenergy and Alternative Fuels Specialist at the WSU Energy Program. “When compared to the baseline CHP scenario, the pretax cash flow increased by $1.15 million in 2014 and $2.0 million in 2032, assuming the lower RIN value. At the average 2012 RIN value, the pretax cash flow increased by $2.2 million in 2014 and $3.5 million in 2032.” Jensen notes that additional capital, and potentially specialized partners, would be required to build and operate the biogas upgrading and RNG filling stations.
Inclusion Of Enhanced Nutrient Recovery
One of the ongoing environmental issues with CAFOs in the Central region is managing excess nutrients. “While AD converts most of the organic carbon to inorganic gases, the same cannot be said about organic nitrogen and phosphorus, potentially causing problems to air and water quality as well as human health,” explains Frear. “Dairy owners identify nutrient issues as one of their most important environmental concerns, one with potentially negative economic impacts.” As a result, a lot of research has been aimed at recovering nutrients from AD effluent for sale as valuable coproducts. For the feasibility study, three nutrient recovery options were investigated:
1) The nutrient recovery system currently operating at the DeRuyter project that uses a traditional screen/roller press for fiber separation and settling weirs and natural drying for phosphorus-containing manure fines collection.
2) Struvite crystallization within an RNG model that will help supplement the high capital and operation costs of this technology by obtaining higher revenue (e.g. RNG and RINs). Revenue is generated by exportation of phosphorus and some ammonia.
3) Combined ammonia-stripping and phosphorus-rich solids settling (also known as the AIR-TRAP system) within an RNG model. Revenue is generated by exportation of fiber, phosphorus-rich solids and an ammonium sulfate solution.
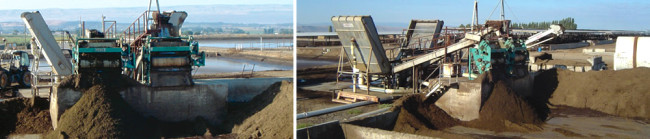
The current nutrient recovery process at DeRuyter uses screens/roller presses to separate fiber (left) and weirs to settle phosphorus-rich manure fines (above).
Table 1 shows the percent removal of nitrogen, phosphorus and salt as well as the resulting pH of the fertilizer using the three nutrient recovery approaches. The first scenario is currently being utilized at the DeRuyter digester. The dairy is getting ready to sell dried manure fines rich in phosphorus as a value-added fertilizer. “This system is rather effective at removing phosphorus at around 50 percent,” says Frear. “But the process does little in regard to nitrogen removal and remediation of nitrate and ammonia concerns.”
The second scenario, struvite crystallization, is used on other wastewaters (e.g. municipal and swine) to remove phosphorus and some ammonia from the effluent. “The feasibility study showed that even at around $150/ton, the struvite option negatively impacted the cash flow when compared to the current screening/settling system used at the dairy, with a loss of over $1 million in revenue in 2032,” he explains. “Therefore, struvite crystallization, in its present state, was not viewed as a viable approach for the DeRuyter project.”
The third scenario involves using a combined ammonia stripping and enhanced phosphorus settling technology developed by engineers at WSU, alongside their industrial partners (DVO Inc. and Andgar Corp.). This physicochemical process combines elevated temperature (50°C), aeration and settling to produce three different product streams: an ammonium sulfate biofertilizer, phosphorus-rich solids, and a residual nutrient reduced AD effluent. “All of these can be used as fertilizers either on-site or sold off-site,” says Frear. A commercialized system (AIR-TRAP) is installed at Vander Haak Dairy in Lynden, Washington.
Three nutrient price scenarios were investigated due to the lack of an existing nutrient market. Yearly revenues were averaged to $389,526 for the low value, $683,855 for the medium value, and $731,453 for the high value due to the range in value of the ammonium sulfate and phosphorus solids fertilizers. “Negative cash flow resulted from the low nutrient price scenario when compared to the fast filling station from the RNG only study, while the medium and high price scenarios resulted in neutral and positive cash flows, respectively,” states Frear. Figure 5 illustrates the three scenarios as well the fast filling station at the high RIN value from the previous section. “This combined system is costly from a capital and operating standpoint, which doesn’t allow it to be too competitive compared with the stand-alone RNG Pro Formas,” he adds. “However, inclusion of nutrient recovery systems, despite the additional capital and operating expenses as well as negative pressure to the entire Pro Forma, might be warranted as a cost of doing business in an emerging CAFO regulatory climate.”
Bill Dunbar, policy advisor at EPA Region 10, confirms this point. “Nitrates and phosphorus are increasingly significant regulatory concerns for environmental and public health agencies, so they’re increasingly significant costs for agriculture,” he notes. “As the market for home-grown, low-carbon fertilizers continues to grow, it seems this kind of systems approach to waste management would become the standard.”
Advancing AD In Washington State
With the recent drop in electricity revenues, the current DeRuyter digester project is not a financially compelling model due to “ever changing electrical prices and volatility in the REC and carbon credit markets,” says Weisberg. “The challenges this project is having aren’t encouraging new projects to emerge in the Columbia Basin, where most of the CAFOs are located.” The findings of the feasibility study support a shift from the conventional CHP model to an RNG model that takes advantage of the accelerating move to natural gas fuels in the transportation sector as well as valuable credits and high values associated with direct fueling of RNG users. The value of nutrient recovery to sustainable dairy operations is another powerful driver of that RNG model, addressing environmental and regulatory issues that could be showstoppers for dairies in the near future.
Many options exist for the DeRuyter project — some more viable than others. However, AD is going to continue to require significant capital investment that may dissuade dairy farmers from adopting this technology, especially when more infrastructure (and complexity) is required. As this feasibility study illustrated, the potential gains of a systems approach, one that goes beyond traditional combined heat and power, are substantial when an RNG model is incorporated. But again, capital and operating costs are a barrier.
An immediate way to help accelerate adoption of advanced AD projects in the Columbia Basin is “via federal/state assistance through infrastructure improvements and grants/loans,” explains Weisberg. “The national shift to methane fuels will address some of the impediments such as filling stations and natural gas vehicle availability, but stable, long-term policy incentives from the state and federal government will continue to be needed for the success of these projects.”
Nicholas Kennedy is a graduate with a MS in Biological Systems Engineering from Washington State University. To review the entire feasibility study report, “Renewable Natural Gas and Nutrient Recovery Feasibility for DeRuyter Dairy,” download http://csanr.wsu.edu/publications/deRuyterFeasibilityStudy.pdf.