After raising $160 million in 2012, Tamar Energy Ltd set out on an aggressive plan to build 40 anaerobic digestion facilities over the next five years, and generate 100 MW of green electricity.
David Riggle
BioCycle March/April 2014
Creation of a “critical mass network” of anaerobic digestion plants is underway across England and Wales, as promised by Tamar Energy Ltd at the company’s launch in February 2012. Its vision is to develop over 40 anaerobic digestion (AD) plants generating 100 MW of green electricity over the next five years. The company points to the significant opportunity for AD to play an increased role in the United Kingdom’s (UK) green energy market, which has been projected to produce at least three to five terawatt-hours (340 MW/hour to 570 MW/hour) of electricity by 2020. “The underdevelopment of anaerobic digestion in the UK is principally driven by a historical lack of financing for the sector,” says Tamar Energy Chairman Alan Lovell. “Tamar Energy will be well capitalized by investors, with a pure focus on producing energy from organic waste, rather than as an adjunct to a waste management business.”
Tamar Energy was able to raise $160 million in 2012. The number of high profile backers providing equity capital for this start-up venture helped to convince normally skeptical observers that the company has serious intentions. Its investor group is led by RIT Capital plc, an investment trust chaired by Lord Rothschild, and Fajr Capital, an international investment firm with members including the Abu Dhabi Investment Council and the Government of Brunei Darussalam, among others. The Duchy of Cornwall, which funds the public, charitable and private activities of The Prince of Wales, is an investor, as is Ludgate Investments, Sustainable Technology Investments and other private parties. Of special interest to those in the organics industry, J. Sainsbury plc, the UK’s third largest supermarket chain with over 1,000 stores, is a strategic partner in Tamar Energy, as well as an investor.
“Raising the money in 2012 was an interesting experience,” says Bill Elliott, Business Development Director for Tamar Energy. “It was the largest European capital raise in the green tech field that year, so it got attention.”
Gathering Momentum
Progress has certainly been made in two years. Tamar quickly began developing AD projects and went from six to more than 70 employees in a very short time. The first facility, a plant at Holbeach Hurn, Lincolnshire, in partnership with food producer and processor A.H. Worth & Company Ltd, was announced in June 2012. In November 2012, Tamar acquired the management and development rights for four anaerobic digestion sites (three of them with planning permission) from the waste management and recycling company Countrystyle Group Limited. In an interesting twist, the deal also saw a newly formed Tamar Organics division take over management and operation of six of Countrystyle’s previously established in-vessel and open windrow composting sites in the south and east of England.
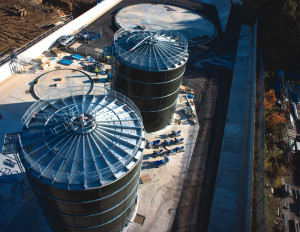
A 2 MW digestion plant in Halstead, Essex is designed to process 45,000 metric tons/year of commercial, industrial and domestic food waste.
“Acquiring those composting plants from Countrystyle fit with our development plan and gave us immediate income from profitable operation of the plants,” explains Elliott. “Having three in-vessel composting facilities and three open windrow composting operations also gives us credibility in the market. We’re not just saying we’re going to do something, we’re actually doing it.”
That acquisition helped to jump-start additional projects and one year later, in June 2013, Tamar announced that work was on or ahead of schedule at four new AD sites. In September 2013, a second wave of AD projects in various stages of development was announced. The locations, annual processing capacities, feedstocks, expected amount of electricity each will generate and technology used for some of these eight plants are listed in Table 1. Toward the end of 2013, another six projects were announced. “After that first round of financing, we are well into raising a second $100 million,” says Elliott. “It feels like there’s a bit of a race going on. We want to quickly build a national chain and to do that means getting on with it.”
As expected, Tamar announced in January 2014 that the Basingstoke and Holbeach Hurn plants completed their commissioning phase and were exporting electricity to the grid. “Both plants are full and nearing the end of their ramp up phase,” Elliott notes. “The return to our investors is in line with Tamar’s expectations. The Retford, Nottinghamshire facility is in commissioning and not far behind the first two with export to grid commencing in early March. Feed-in Tariff (FIT) is an important element of the operating plants’ income and Tamar has entered into short-term power purchase arrangements until we have a greater potential as sites come on line.”
Feedstock Assessment
Tamar’s concentrated effort at AD development has highlighted the issue of what feedstocks will be available to fuel all its plants. “When we started, we thought our feedstock would consist of about a third from agriculture, a third from food processors and a third from postconsumer domestic or commercial food waste,” explains Elliott. “That was the assumption in the business plan. However it didn’t take us long to see that it might not work out exactly that way.”
First it became apparent that the agricultural waste had a significant alternative value — for animal feed, pet food or as the raw material for something else. Not as much was available as Tamar had anticipated and what there was would have to be purchased. In terms of waste from the food processing industry, it was expected that the company’s partnership with Sainsbury’s supermarkets would make more feedstock readily available. In fact, the chief executive of Sainsbury’s commented in a newspaper article that it would encourage its suppliers to use the Tamar sites to cut down waste through its network.
In reality, Tamar learned that there is very little waste in the supply chain. After visiting some potential customers, it was clear that the profits of food manufacturers come from making food, not waste. Sainsbury’s itself is a zero waste-to-landfill company. Any surplus is donated to local charities or made into animal feed. Only food not suitable for consumption is used to generate energy through anaerobic digestion.
Those realizations increased the significance of obtaining steady supplies of food waste from other sectors to create viable AD plants. Corroborating that view, the Anaerobic Digestion and Biogas Association (ADBA) estimates that approximately two-thirds of the UK’s biogas potential comes from residential and commercial food waste — the vast majority of which is in the control of local authorities3. At this point, only around 19 percent of UK Local Authorities (LAs) have household food collections, and of those, around half collect food and garden waste commingled rather than source separated. Therefore, obtaining that steady supply will require careful planning. However, there’s a mutual dependency at work. The LAs — and businesses like restaurants, hotels and supermarkets — need to collect more food waste in ways that the AD industry can use, and the industry must provide a sufficient number of plants in close enough proximity to the waste source so that it can be transported and treated economically.
“Because we’re still planning to have 40 plants and 100 MW of output over the next five years,” says Elliott, “we’ve been thinking there may not be enough source separated food waste to fill them. We’ll need around 2.8 million tons of material and at the moment, while there is plenty of food waste, there isn’t 2.8 million tons of source separated Local Authority food waste available. We may have to rely on being innovative in the feedstock sources we look at, depending on where the plant is located.”
Elliott shares the accepted wisdom that the number of LA contracts for food waste will increase as the 2020 European Union Landfill Directive requirement to reduce the amount of biodegradable municipal waste sent to landfill to 35 percent of 1995 levels gets closer. Likewise, he believes that there will be significantly more industrial and commercial operations diverting source separated food waste. According to ADBA, the Government’s Landfill Tax escalator is a key driver for LAs looking to start separate food waste collection if they don’t have one already. The tax is rising to £80/tonne ($131/metric ton; £1 = ~$1.66) on April 1, 2014 and, although an announcement has yet to be made regarding the amount of tax in future years, expectations are that it will continue to rise.
Digestate Markets
One of the most interesting details about Tamar from an organics recycling perspective is the amount of work it has done from the outset to evaluate markets for digestate, as well as markets for energy. David Border, a consulting microbiologist with Tamar who has years of experience in the composting and anaerobic digestion industries, calls digestate “the elephant in the room” within AD business plans. He and others believe a new kind of thinking is required to develop value-added markets for digestate (see “Creating A Solid Base for Digestate Use in the UK,” October 2012).
“This is a small country,” notes Elliott. “The amount of land you can put digestate on is limited as are the periods of the year when you can apply it on that land. One of the real keys is to stop seeing digestate as a liability and start seeing it as an asset.” Tamar is looking at combining compost and solid digestate to make a better soil improver, blending both with other products and adding nutrients to digestate cake on its own. “We’re exploring our best options — we’ve got to solve this equation,” he adds. “Two years ago when we started, the cost of digestate management, including transport and land application, was around £6/$10 per tonne. Today it’s £12/$19 to £17.50/$28. In central London, by the time you’ve carted it out of the city, the cost could be around £20 $33/tonne. The whole economics of a plant are dead if you don’t have a good alternative.”
Tamar is not alone in working on this issue. At present, according to the Waste Resources and Action Programme (WRAP), the most commonly used digestion system in the UK is wet mesophilic operating between 25° to 40°C (77-104°F), producing a rich organic slurry as an end product. Most commonly, that is recycled to local agricultural land through injection or other application method. However, that may change as the value of solid digestate is more widely recognized. WRAP published an interesting study in 2012, “Enhancement and treatment of digestates from anaerobic digestion,” which highlights a number of possibilities for ongoing research and development. Looking at it from another angle, the ADBA’s Practical Guide to AD (see “Framework For AD Project Development,” November 2013) cites a rule of thumb that dewatered cake from wet AD systems will require only 15 to 20 percent of the vehicle movements required for liquid digestate (ADBA, 2013), which provides clear incentive for developing these new products from a transportation angle alone.
Location, Location, Location
The importance of where new AD plants are built is clearly recognized in Tamar’s plans. Elliott, who previously worked for 18 years as Development Director for SITA, a large UK waste management company, notes that waste haulers earn money while picking up bins, not driving to a disposal point. In his view, economical transport of any waste is not very likely if it has to travel more than 25 to 30 miles from the point of collection.
“Pubs, restaurants and other commercial establishments will usually do what is least expensive in terms of waste collection arrangements,” he says. “So, if someone is charging £20/$33 per lift to take the general waste bin to landfill, that will include the £80/$132 metric ton landfill tax. On the other hand, if it costs their hauler less than half of that — say £8.50/$14 per lift — to take a food waste bin for anaerobic digestion at a nearby plant, that’s a no brainer. They’ll fill up the cheaper food waste bin.”
Finally Elliott notes that a “build it and they will come” philosophy as the only rationale for building a new facility doesn’t go down very well with their investors. “That’s a very hard sell,” he says, “and it certainly isn’t the only factor in our considerations. However, to a certain extent it is true — especially with the clear need in the UK for more AD plants in strategic locations. If there is a disposal point nearby that’s cheaper than the alternative, then they will come.”
David Riggle is International Editor and a past Managing Editor of BioCycle. He has been living and working in Scotland for the past 14 years.