Increasing volumes of commercial food waste, much of it contaminated or packaged, led digestion facility in South San Francisco to install a depackaging unit.
Nora Goldstein
BioCycle May 2018
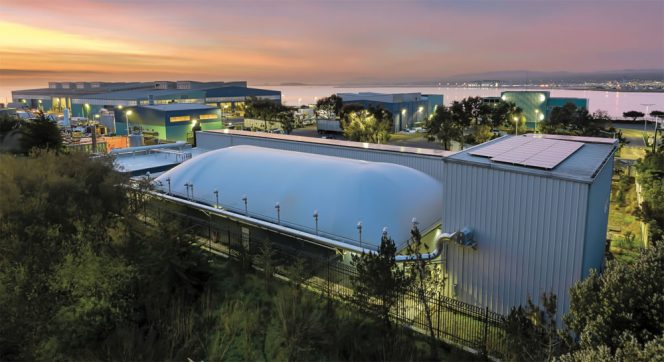
Dry fermentation digester at Blue Line Transfer processes about 11,000 tons/year of residential and commercial food waste and green waste. Photo by Mike Achiro
South San Francisco Scavenger Company (SSFSC) and Blue Line Transfer, the facility that handles SSFSC’s recycling and disposal, started up its dry anaerobic digester (AD) in late 2014. Situated at Blue Line’s 11-acre site in South San Francisco, California, the one-quarter-acre fully enclosed facility includes an aerated receiving bay, 8 modular AD tunnels — each with capacity for 240 cubic yards of material — and two in-vessel composting tunnels. “We are processing about 11,000 tons/year of food and green waste, which is close to the facility’s capacity of 11,200 tons/year,” notes Doug Button, president of SSFSC and its sister company, Blue Line Transfer.
SSFSC collects both commercial and residential organics in a service area that includes South San Francisco, Brisbane, Millbrae and San Francisco International Airport. About 20,000 households in three cities are serviced with weekly organics collection. Curbside food waste collection was integrated into the existing green waste collection program; households received 2-gallon pails for food waste, which they add to their green waste carts. Collection shifted from biweekly for green waste only to weekly with food waste incorporated because of vectors, says Button, adding that participation increased when the switch was made. “The residential organics are very clean,” he notes. “We are able to unload trucks servicing residential routes directly into the digester facility’s aerated receiving bay, which is 20-feet wide, 50-feet long and 28-feet high.”
Commercial organics, on the other hand, are very contaminated. Trucks servicing commercial routes unload in the materials recovery facility located at the transfer station. Originally, a trained employee would hand sort all visible contaminants — primarily plastic bags — prior to the materials being mixed with yard trimmings and loaded into the digester. But hand sorting by itself was not adequate, especially as SSFSC started increasing the amount of commercial food waste being collected, which included more packaged food.
As a result, the level of contamination in the digestate, especially plastic, became a concern. SSFSC transports the digestate to Napa Recycling and Waste Services in Napa (CA), where it is composted. “The operator showed us photos and told us that the contamination levels were problematic,” says Button. “If we were not able to clean it more, we were told the facility would have difficulty accepting our digestate in the future.”
The contamination, combined with the increase in packaged food, led SSFSC to evaluate food waste depackaging equipment. “We ran a trial with a Scott Equipment Turbo Separator, and ended up purchasing the THOR model with capacity to process 18 to 20 tons/hour,” he explains. “It was installed in July 2017. It runs for 5 to 6 hours a day, and throughput averages about 10 tons/hour, depending on the size of the screens and the cleanliness of the material. The dirtier the feedstock is, the longer it stays in the machine to do the separation.” On average, residuals comprise about 30 percent of each commercial load processed in the separator.
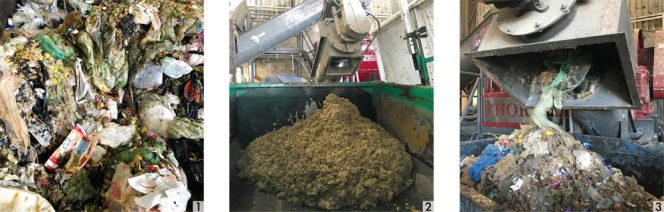
Contamination in the commercial stream, combined with an increased flow of packaged food, led South San Francisco Scavenger Co. to purchase a Scott Equipment Turbo Separator. Incoming organics (1); Fresh mash (2); Reject material (3). Photos by Teresa Montgomery, South San Francisco Scavenger Company
Side Effects
The digestion and in-vessel composting tunnels are less than 100 yards away from an 800,000 sq. ft. biotechnology complex, so managing odor emissions is a top priority. The digester tunnels are loaded and unloaded after 12:00 am and before 7:00 am, when the fewest people are around. Once loaded, the mix is aerated using an in-floor air supply system until the material reaches 125° to 130°F. Exhaust air from this stage is sent to an acid scrubber and biofilter to remove ammonia, VOCs and particulates. “We haven’t had one complaint in the almost 3.5 years we have been operating,” notes Button.
Once the desired temperature is reached, the system switches over to the anaerobic process, with microbes consuming the available oxygen. Material is sprayed with a fine mist of liquid (“percolate”) from the percolate tank, which is underneath the tunnels. The percolate is heated by a boiler, which is fueled by tail gas from the biogas conditioning system, and, when necessary, line [natural] gas from the pipeline. Total retention time in the digesters is about 3 weeks.
Prior to installation of the depackager, the mix going into the digester was 60 to 65 percent food waste and 35 to 40 percent green waste. With the “mash” (the preprocessed food waste), SSFSC was able to increase the tonnage loaded into a 240 cubic yard (cy) tunnel, so the ratio of food waste to green waste is closer to 70:30. “We have to be careful how much we increase that ratio, because if we put in too much food waste, the mix loses some porosity, and we need to keep that porosity at a set level so the organics break down,” explains Button.
The mash is still solid, but contains about 60 to 70 percent moisture. Initially, the increased amount of food waste led to an increase in biogas production. “But then, all of a sudden, biogas production was going down,” he recalls. “In general, biogas volume goes up and down for a number of reasons. In this case, however, we saw that we were using all the tail gas plus line gas to heat the percolate, which meant something was causing the temperature of the percolate to drop. We quickly recognized that the water contained in the mash was draining to the percolate tank. The mash was cold, which meant the water draining into the tank was dropping the temperature of the percolate, which in turn would kill the bacteria. In addition, we had to pump water out of the percolate tank more frequently, and take it to the wastewater treatment plant. By pumping to remove liquid, we were losing more of the bacteria needed for AD.”
To remedy this unanticipated side effect, SSFSC installed a 20 cy box with a screen on the bottom next to the depackager. The mash coming out of the Turbo Separator goes into the box, and the water drains out. “We let it drain for a day,” says Button. “By sitting in the box, with the water separated out, the mash is warming, which is beneficial to the digestion process. The liquid goes to the sanitary sewer, so we no longer have to truck it. And biogas production has been increasing.”
Digestate And Biogas Use
Once the methane content drops below one percent, and hydrogen sulfide is not detected, the digester can be open. Material is moved to one of the composting vessels (from 12:00 am to 7:00 am to avoid odor impacts). The main purpose of this on-site composting step is to scrub out the ammonia before the digestate is transported to Napa Recycling and Waste Services (NWRS). SSFSC pays for trucking and to tip the digestate. “The facility charges a lot less than it does for green waste because the digestate is half way or more broken down so the processing time is shorter,” he explains.
The digestate is shipped almost daily to NWRS. “While it may have already met PFRP, when it arrives we mix it with other incoming feedstocks and put it through our process to ensure a consistent finished product,” explains Will Kelley, NWRS’ director of composting operations.
The biogas is upgraded with a BioCNG conditioning system and utilized as compressed, renewable natural gas (RNG) in SSFSC’s collection trucks. When BioCycle last wrote about this AD facility (“Biogas To Fleet Fuel In South San Francisco,” July 2016), the company had equipped 27 of the 40 trucks in its fleet with compressed natural gas engines to run on RNG. Today, 34 of the 40 have CNG engines. “We are expanding the fueling system to 39 posts, so should be almost completely converted in the next year or two,” says Button.
The facility produces between 380 to 500 diesel gallon equivalents (DGE) per day of RNG. All trucks with CNG engines utilize RNG, typically supplemented with line gas during the week to reach 3,600 lbs/fill. On weekends, when the trucks are stationary, they are filled completely with RNG.
SSFSC is able to sell RINs under the federal Environmental Protection Agency’s (EPA) Renewable Fuel Standard, and carbon credits via California’s Low Carbon Fuel Standard. “We generate a bunch of RINs, but almost all are classified as D5 RINs [advanced biofuel], which have a lower market value than D3 RINs [cellulosic biofuel], which is what landfill gas qualifies for,” he adds. “It doesn’t make sense because a landfill can take a banana peel and get D3 RINs. We take that same banana peel and have to sell D5 RINs. We are still trying to work with EPA to get more D3 RINs, but it is a long process.” ( “101 For RINs, Nov. 2017, to learn more.)