With over 15 operating anaerobic digesters and several innovative power purchase incentive programs, Vermont provides an opportunity to assess what is required to advance AD in the agricultural sector.
Nora Goldstein
BioCycle February 2013, Vol. 54, No. 2, p. 28
Accompanying article: Digester Taps Thermal Energy To Grow Greens
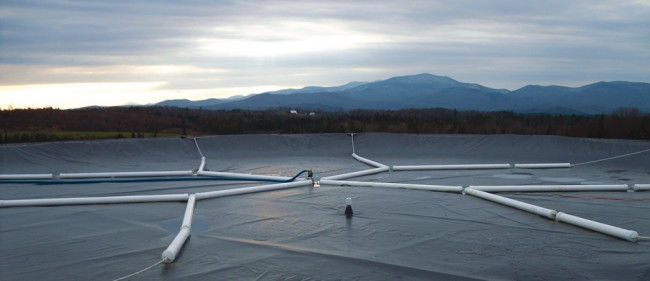
Joneslan Farm in Hyde Park milks about 200 cows. It installed a UEM digester, which has a prefabricated, insulated 240,000-gallon geomembrane tank. Weighted pipes keep biogas under the cover pressurized.
In the fall of 2012, Brian Jones of Joneslan Farm in Hyde Park, Vermont spread the first load of manure that had gone through the farm’s new anaerobic digester. “It didn’t smell at all,” recalls Jones. “And we’ve been told that the nitrogen in the digested manure is more available to the plants we grow.”
When the Joneslan Farm digester went on line in late Spring 2012, it became the 15th operating digester in the state of Vermont. Since that time, several more digesters have come on line or are in construction (see http://www.vermontagriculture.com/energy/ for most current data). Like projects in other states, Vermont dairy farmers have been able to utilize federal funds for digester construction, primarily from U.S. Department of Agriculture Rural Development and Natural Resource Conservation Services (NRCS), as well as the renewable energy stimulus dollar grant program (Sec. 1603 Treasury grants) that expired at the end of 2011.
But unlike other states, farm digester projects in Vermont were able to tap into a utility-funded grant program that was created as a result of an insurance settlement related to the sale of the Vermont Yankee nuclear power plant to Entergy Nuclear. The utility, Central Vermont Public Service (CVPS), started the Renewable Development Fund (RDF) in 2004, primarily to help finance utility interconnections. The RDF program also included funds for technical assistance related to digester selection and operation and feasibility studies to evaluate interconnection options. Also in 2004 CVPS created its Cow Power program where customers opt in to pay a premium of $.04/kilowatt hour (kWh) on renewably-produced power. In turn, CVPS (renamed Green Mountain Power after merging with that utility in 2012) pays farms a premium of $.04 for each kWh they deliver to the grid.
In 2006, Entergy Nuclear Vermont Yankee, LLC requested permission from the utility regulating body, Vermont Public Service Board (PSB) to increase power output from the nuclear plant and to store high-level radioactive waste on-site. The PBS agreed to the request but required Entergy to fund a renewable energy development program. This funding — administered through a “Clean Energy Development Fund” (CEDF) created by the state legislature — could be used “to increase the development and deployment of cost effective and environmentally sustainable electric power sources.” The first few grants targeted three-phase interconnections; grants for later projects were unspecified in terms of use.
A year earlier, in June 2005, Vermont’s Sustainably Priced Energy Development (SPEED) Program was enacted by the Vermont legislature. The goal of the SPEED program was to “promote development of in-state energy sources that use renewable fuels (SPEED resources) to ensure that to the greatest extent possible the economic benefits of these new energy sources flow to the Vermont economy in general and to the rate paying citizens of the state in particular,” according to the SPEED website. SPEED established a goal that 20 percent of total statewide electric retail sales annually must be generated by SPEED resources that constitute new renewable energy, starting in 2017.
In May 2009, the Vermont legislature passed the Vermont Energy Act (Act 45) that significantly modified a number of provisions in the SPEED Program. Act 45 created the feed-in tariff Standard Offer Program (SOP) and Standard Offer Contracts for SPEED resources of less than 2.2 MW. The SOP is designed to encourage development of SPEED resources using a variety of different renewable technologies. The Act establishes default prices for the standard offer for different technologies, calculated to allow developers of renewable power purchased through the SPEED program to recover their costs plus a return on their investment. The original rate for digester projects was initially set at $0.16/kWh for a contract term of 20 years. A subsequent rate setting lowered the farm digester rate to $0.14/kWh for 20 years. (Under SPEED, farmers with anaerobic digesters can retain ownership of the environmental attributes created by their projects.)
In addition to the incentives just described, the Vermont Agency of Agriculture, Food and Markets (AAFM), through its Best Management Practices program, has provided grants to assist with upfront digester construction costs as well as costs for solids separators, and manure storage and transfer. The grants top out at $75,000. Funds for those grants were monies allocated by the Vermont legislature for water quality projects on farms. “We just learned that at least 10 percent of the manure generated in the state of Vermont goes through an anaerobic digester,” says Stephanie Congo, an agricultural engineer with AAFM. “And Vermont has one of the higher per capita number of digesters in the U.S. compared to the overall number of dairies in the state.” Congo notes that January 2013 statistics indicate Vermont has 993 milking dairies with about 134,000 milking dairy cows.
Joneslan Farm Digester
In early December, BioCycle had an opportunity to tour two fairly new digesters in Vermont — Joneslan Farm in Hyde Park and the Gebbie’s Maplehurst Farm in Greensboro. (A third digester, part of the “Green Machine” system at Jasper Hill Farm in Greensboro, also was on the tour and will be profiled in an upcoming issue.) The Joneslan Farm milks about 200 cows, with about 230 head in total. Its heifers are kept at another farm, but may be brought back to Joneslan Farm in the future. Owned by brothers Brian and Steven Jones, the farm is located on about 400 acres. The storage lagoon has about 200 days of storage. A significant incentive for installing a digester was the need for bedding. “We had been using sawdust for bedding and would skimp because it was hard to get and expensive,” says Brian Jones. “With the digested solids, we can make the bed thicker and have seen a reduction in hock lesions.”
The Jones began exploring the option of a farm digester several years ago. They started working with Mike Raker, a contractor to the CVPS Rural Development Fund, who was hired to provide technical and grant application assistance to the farms. “We evaluated what their best bet would be in terms of the SPEED program versus net metering,” recalls Raker. “Vermont offers group net metering, which allows offsetting usage for multiple meters. Many net metering programs only allow one meter. In Vermont, a renewable energy producer can group accounts, as long as they are all with the same utility.”
Raker explains that under the Vermont program, producers receive both the value of the kWh produced as well as the demand value (electricity required at any one moment). “These are the two costs utilities have and until recently, the value paid via net metering reflected only the kWh value. Now, with demand value combined with kWh value, producers can get something on t he order of 14 to 16 cents/kWh — the equivalent of the host utility residential rate — for all the power they produce. With SPEED, a farm the size of Joneslan would get $0.14/kWh.”
Joneslan Farm started out in the SPEED program, but then switched to group net metering offered by Vermont Electric Cooperative. “We have 17 meters in our group; 16 are family and one is a nearby minimart,” says Steven Jones. “We can take anyone on Vermont Electric Cooperative’s grid. When we did the math, we realized that we could average 15.3 cents/kWh for 10 years, and 16 cents for 20 years, so in 10 years’ time, we would be better off than the SPEED program which is $.014/kWh for 20 years.”
Given the smaller size of its dairy herd, Raker introduced the Jones brothers to UEM, Inc., which was getting ready to enter the farm digester market in the U.S. “I was looking for smaller scale systems and learned about UEM, which has been supplying turnkey digester systems to the industrial food processing and wastewater sectors for many years,” he says. “Our challenge is to get more aggressive at bringing the cost of farm digesters down, especially for smaller dairy farms. The question to the industry is, ‘Can we build systems where a farmer can expect a payment of 16 to 20 cents/kWh, with grant support, when available, from NRCS and USDA Rural Development. The answer better be yes.”
Installation of the digester and related equipment was done in phases, with interconnection to the utility grid completed in August 2012. The UEM digester, which is 16-feet deep and 72-feet in diameter at the top, has 240,000 gallons of capacity. It was sized to accommodate 100 more cows (if the heifer operation is brought to this farm). Joneslan did the excavating, which involved blasting to create the digester pit. “The NRCS EQIP funds paid for the blasting and excavation of the pit, the manure pumps and piping, and the solids separator and building where it is housed,” says Brian Jones. “Our Section 1603 grant only covered 10 percent of our capital costs because the 65 kW engine we installed falls below the 150 kW engine requirement to have 30 percent of the costs covered. At this point, our total capital costs are around $825,000, somewhat over what we had budgeted.” Nina Kshetry of UEM notes that actual facility costs are closer to $1 million due to the retrofits that have been needed.
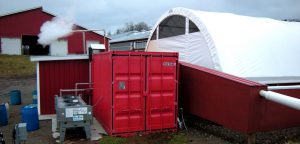
The equipment and controls, as well as the engine, are housed in a shipping container (foreground) that is adjacent to the solids separator building (right).
UEM supplies a complete turnkey digester plant, which includes design and engineering, all the equipment and controls (including the engine set) and utility interconnection. Its digester uses geomembrane for the tank instead of concrete, which typically is used by below-ground digester systems (other than lagoons). “For agricultural digesters, we wanted to utilize a completely geomembrane solution for the tank and the cover,” explains Kshetry, noting that its goal for the farm digester sector is to provide a standard, cost-effective design that can be prefabricated at its facilities and then shipped to farms to be installed. “Our experience has shown that the less site activities we have to do, the more affordable the projects will be,” she adds. “Use of membrane material to make the tank allows us to move toward the goal of minimizing site activity.”
For the Joneslan installation, the entire 240,000-gallon tank was shipped in a single prefabricated section, in the shape of a salad bowl, and placed into the excavated hole. The 72-foot diameter cover was shipped as a separate prefabricated section. Insulation for the tank was assembled onsite into modular pieces and installed on the sides and cover of the tank. The cover has 4-inches of insulation underneath; the tank has 4 inches of insulation for the first half of the 16-foot depth, and 2 inches for the remaining 8 feet. In the future, UEM plans to preassemble the insulation and ship it to the site in modular pieces.
A biogas-based mixing system is used to agitate the digester contents, but UEM is evaluating mechanical mixers for future installations. There is an 18-inch concrete support beam around the perimeter of the digester. Weighted pipes lay on top of the cover to keep biogas under the cover pressurized. The project uses an I-Power 65 kW biogas unit.
While the insulation has been effective at retaining heat in the tank, the heat exchanger in the receiving pit is undersized, and it has been difficult to get the manure temperature high enough over the winter months. As a result, biogas production has been lower than anticipated. In early December, the system was only generating about 25 kW. “It’s bringing in enough revenue to pay the utility bills on the farm,” says Jones. “The digester is only around 80°F and it should be closer to 100°F. The heat exchanger just isn’t big enough, so we will have to replace it.” In addition to heating the digester with the engine heat, there is enough to preheat the water used to wash the milk vessels. “Eventually we’d like to provide heat to our homes as well,” he adds.
The Jones brothers own and operate the digester; UEM provides technical assistance as needed. The farm isn’t planning to take in off-farm substrates, at least not at this time. “Our primary motivation was the bedding and the power,” says Jones.
Maplehurst Farm Digester
The Maplehurst digester in Greensboro, which uses the RCM system, was started up in late 2011, and began producing useable quantities of gas in the Spring 2012. The Gebbie’s Maplehurst Farm is owned by Peter and Sandy Gebbie. It has 375 dairy cows and several hundred young stock. The Gebbies began planning the digester project in 2008, and were one of the original applicants to the SPEED Standard Offer program in the fall of 2009. The Certificate of Public Good (CPG) — issued by the Vermont PSB to generate electricity for the grid — was approved in October 2011.
The 300,000 gallon digester, 16-feet deep and 60-feet in diameter, was completed and filled with manure in the winter of 2011/2012. The barn has a slatted floor and manure is gravity fed (at about 8-9% solids) to the receiving pit. Digestate is separated in a DODA unit; solids are used for bedding and digested effluent flows to the farm’s storage lagoon, where it is ultimately land applied. “It was getting increasingly difficult to get sawdust for bedding and what we could get was very expensive,” says Peter Gebbie. “Being able to produce bedding from the digested solids is a significant benefit.”
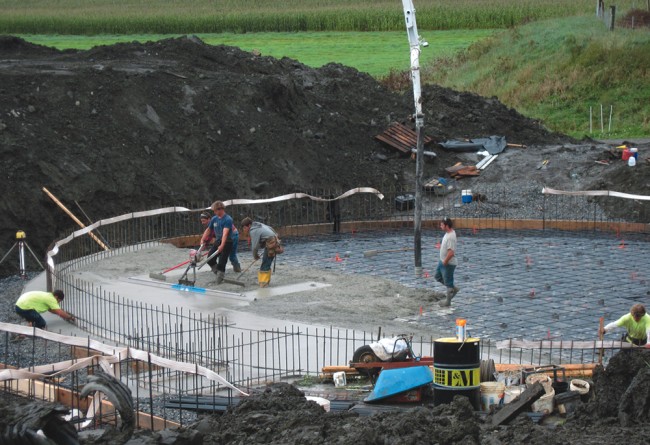
Maplehurst Farm in Greensboro installed a 300,000-gallon RCM digester to process manure from about 375 dairy cows. Recently, it was approved to receive off-farm feedstock to boost biogas production.
Manure from another farm digester in Vermont was used to seed Maplehurst’s digester. An RCM hydrogen sulfide removal unit is used to condition the biogas ahead of the gas engine. A 150 kW Martin Machinery engine set was installed in late spring 2011 and commissioned in July 2011. “Our farm is on a single-phase electric line and we were told by the utility that the only way we could avoid a costly three-phase upgrade or an even more costly transfer-trip interconnection system, was to install an induction generator which cost over $220,000,” explains Gebbie. “Our generator was built specifically for this project. The utility wanted it for protection. It took an extra year to work through that process, and get it interconnected. We sized the engine at 150 kW because that didn’t require replacing the power line. That size also fits fairly well with the number of cows we have, however if we process only manure, we can only generate about 70 kW.”
Recovered engine heat is used to heat the digester. All the electricity generated is sold at wholesale rates under the SPEED contract for $0.14/kWh. Maplehurst Farm buys back the power it needs at market rates for $0.18-0.19 cents/kWh. “The goal is produce and sell as much power as we can to earn those revenues,” says Sandy Gebbie. “But when we do buy power, we pay more than what we sell it for.” The farm also participates in Green Mountain Power’s (GMP) Cow Power program. Currently, supply of green power is exceeding utility customer demand, so GMP sells the renewable energy credit portion of the environmental attributes into the Connecticut market at the current rate of over $.04/kWh; proceeds go back to the farm.
The farm installed a 20,000-gallon tank to receive off-farm substrates when it built the digester. It wasn’t receiving any off-farm material in early December, but had applied to the PSB to amend its CPG in order to start receiving substrates. In its application, Gebbie noted that the “digester has not been performing as anticipated … exclusively using manure produced on the Farm, and the digester is at risk of stopping during the cold weather months without the addition of more potent substrate, such as food waste.”
On December 19, 2012, Maplehurst Farm received permission from the PSB to import up to four tractor trailer loads/week of off-farm feedstock to add to the digester. The following requirements are outlined in the amended CPG: a) Ensure that at all times, the amount of on-farm feedstock exceeds the off-farm feedstock used in the digester; b) Ensure that at least 51 percent of feedstock shall be derived from on-site agricultural operations; c) Obtain all necessary permits or approvals as required by Vermont Agency of Natural Resources (ANR) and AAFM; d) Except for testing purposes, if using off-farm food waste, obtain a Solid Waste Management Certification from ANR’s Waste Management Division; and e) Except for testing purposes, if using off-farm liquid food processing wastes, only accept such wastes from generators that have received an Indirect Discharge Permit from ANR’s Wastewater Management Division. All off-farm feedstock shall be immediately transferred to the covered substrate tank and stored in the tank for no more than seven days before being pumped directly into the digester.
Capital costs for the Maplehurst digester were about $1.5 million. The farm received a Section 1603 grant, funds from USDA Natural Resource Conservation Service’s EQIP program, CEDF and Cow Power, AAFM and a project grant from the U.S. Department of Energy.
2013 Grant And Incentive Outlook
With the reauthorization of the 2008 Farm Bill still in flux in the current Congress, Vermont officials are uncertain about the status of federal funding through the USDA Renewable Energy Assistance Program (REAP). “It’s an unknown,” says Alexander DePillis, Senior Agricultural Development Coordinator with AAFM’s Division of Agricultural Development. “At the state level, there is discussion about getting a new fund established for renewable energy, utilizing money returned to ratepayers as a result of the 2012 merger between Green Mountain Power and CVPS.” He adds there is a growing emphasis on funding for thermal projects, e.g., increased energy efficiency in the agricultural sector.
The rate paid under Vermont’s SPEED program was recently evaluated to determine if $0.14/kWh is adequate to cover the costs of renewable power generation via anaerobic digestion at dairy farms. “The contractor’s report was just submitted to us recently,” says Stephanie Congo of AAFM. “This study is looking at typical digester inputs, as well as with and without current and past grant funds to offset capital costs, to assess the total economics of a farm digester facility.”
A current challenge in Vermont is that Green Mountain Power’s Cow Power program needs to expand its base of customers willing to pay the voluntary tariff for green power. “The CVPS Cow Power program, now GMP Cow Power, is an innovative green energy initiative created approximately 10 years ago which helped farmers address challenging waste management issues and improve their bottom line,” notes Chuck Ross, Secretary of the Vermont AAFM. “Today, the program is highly acclaimed for its success, bringing many digesters on-line, and has established Vermont as a national leader for this technology. One of the challenges of this program is matching the customer demand with the supply of the digester-produced energy. CVPS and now GMP, have worked hard to make sure the revenue has been available to meet the premium. The renewable energy marketplace has continued to evolve since the program’s inception. As GMP Cow Power looks to the future it will need to continue to work to align customer demand with the farm-supplied gas so that farmers can have the financial certainty they need to make these investments and Vermont energy consumers can continue to help drive the creation of green renewable base load power generated from the manure of our farm industry.”
Overall, utilities in Vermont have been receptive to facilitating power purchases from farm digesters, add DePillis and Congo, noting that utilities like Vermont Electric have gone the extra mile to work with farmers such as Brian and Steven Jones.
Last year, the Vermont legislature passed Act 148, which phases out disposal of organic wastes in landfills. While farm digester facilities in Vermont are taking in liquid food processing residuals, the volume is typically around 10 percent of total digester inputs. “From the point of view of our agency,” explains DePillis, “there are several key questions that need to be answered for farm digesters taking off-farm substrates: What does the material contain? Can it be stored prior to digestion? And does the farm have an adequate land base to apply the digested manure and substrates? It really is a nutrient management issue.”
The Vermont Agency of Natural Resources (ANR) also has oversight of food processing waste streams via its indirect discharge permitting program that covers wastewater that doesn’t go to a wastewater treatment plant. “The indirect discharge permit helps ensure that a food processor or its hauler isn’t driving around with a truckload of food waste looking for a place to unload,” explains Carey Hengstenberg with Vermont ANR. “The permit includes information on the contents of the material, and where it is being discharged.”
As the organics disposal ban phases in (enforcement starts with larger scale food waste generators and eventually will ban all food waste disposal), ANR and AAFM are evaluating the role that farm digesters can or will play in managing these materials. “In Vermont, no food scraps from commercial and institutional generators are in a pumpable, liquid form, which is how farm digesters in the state receive off-farm substrates,” says Congo. “So at this point, farm digesters aren’t a good fit for the food scraps stream.”
Hengstenberg adds that digesters receiving source separated organics from the municipal solid waste stream would be regulated by ANR. “Our policies draw the line on what is considered farming and what is not,” she explains. “A lot of farms seem hesitant to have ANR involvement in their operations.”
In late November, Mike Raker held a one-day meeting for farm digester operators in Vermont. “The biggest operational issue right now for the farms is hydrogen sulfide (H2S) and the impact it is having on the equipment, particularly the engine generators,” explains Raker. “All of these gensets were oversized, so the farms aren’t running them at their rated capacity. That isn’t a problem, as the facilities were designed to accommodate growth. What is a problem is that the H2S causes more friction in the engines, which leads to overheating. To avoid the overheating, the units are being run at a lower output, thus having an overall negative impact on power generation. ”