Compostable product disintegration trials conducted in British Columbia help lay groundwork for open source, field testing protocol.
Chantal Strand and Emily McGill
BioCycle September 2017
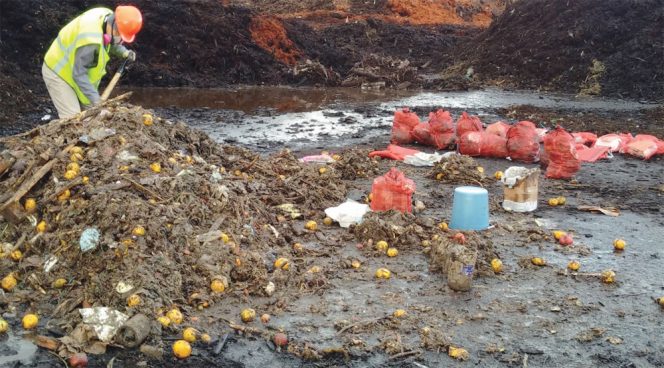
The high solids AD facility processes commercial food waste and amendment. Mesh test bags (right) loaded with compostable products and feedstock were buried in the middle of three AD tunnels. Photo courtesy of BSIbio
To find answers to this question, BSIbio, a distributor of compostable food service ware and product packaging based in Vancouver, British Columbia, partnered with the University of British Columbia’s (UBC) Faculty of Land and Food Systems and regional composting and anaerobic digestion facilities, to conduct field testing trials. The long-term goal is to create a reliable testing protocol to help raise the industry’s understanding of compostable product disintegration across different facility types and processes.
Funding for the field trials was provided by Canada’s National Science and Engineering Research Council (NSERC). The test method used was based on existing best practices for testing compostable product disintegration, refined in consultation with industry experts. The disintegration study, which took place between October 22, 2014 and February 16, 2015, had both an anaerobic and aerobic component. The first half of the study analyzed the breakdown of compostables at a high solids anaerobic digestion (HSAD) facility, followed by covered aerated static pile (CASP) composting. The second half studied CASP-only disintegration.
“Standardized field testing for compostable products will help answer questions about the variables in a composting facility that impact disintegration, with comparable results that could provide baseline data for developing decision making tools for facility operators,” notes Rhodes Yepsen, Executive Director of the Biodegradable Products Institute (BPI), which certifies compostable products.
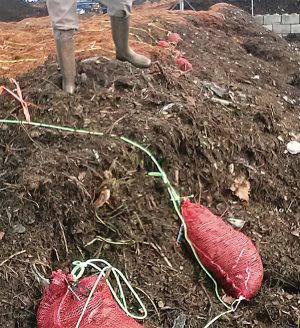
At the CASP, the bags were laid on the side of a new row and buried as the row was built. Photo courtesy of BSIbio
Test Methods
On October 22, 2014, BSIbio and UBC project participants loaded 13 different BPI-certified compostable products and feedstock ingredients into mesh polypropylene bags. The tested products ranged from clamshell containers made from sugarcane fiber (bagasse) to cold cups, soup bowls, hot cups, cutlery, deli containers, and biofoam trays made from polylactic acid (PLA). Compostable ingredients were placed into mesh testing bags in a dry, unsoiled state. Two concentrations of packaging were used: high (20 percent by volume) and low (10 percent by volume). Each trial had eight duplicates for each concentration and was replicated three times.
The test method commonly used in aerobic composting facilities involves combining evenly scooped feedstock and compostable product samples into mesh bags. A natural control ingredient with known disintegration is included to validate test results. If the control material does not break down during testing, the test is considered invalid. For these tests, a 10-inch by 10-inch square of 2-ply kraft paper was used as the control ingredient.
Criteria used to assess disintegration was based on American Society for Testing and Materials (ASTM) standards D6868/D6400, but adapted for the facility’s specific requirements. End products were considered successfully disintegrated if they broke down to less than 10 percent of their original weight within 42 to 70 days, could pass through a one-eighth-inch screen and did not pose a threat to end customers (i.e., no sharp edges).
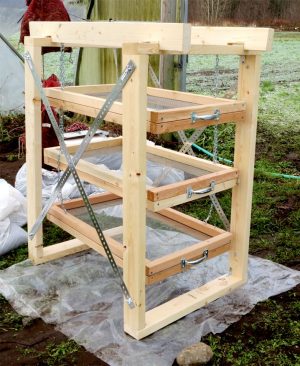
Entire contents of sample bags were sifted through three successively smaller screens to evaluate disintegration. Photo courtesy of BSIbio
Field Trials
Anaerobic Digestion Testing
The HSAD facility was processing commercial source separated food waste in the AD tunnels. The mesh test bags loaded with the compostable products and feedstock were buried in the middle of three enclosed AD tunnels. At this facility, after a 14-day retention time in the tunnels, HSAD digestate is extracted, mixed with ground yard trimmings and postprocessed in the reverse-aerated CASP, effectively converting to an aerobic process to manufacture compost.
In the field trial, after 14 days, tunnels were emptied with a front loader and mesh bags were transferred to the CASP for composting. About 20 percent of bags were lost in transfer due to the volume of material being moved. Bags were buried manually in the forced-air CASP from 0.5 to 5 feet deep and left to process for another four weeks. They were removed by hand after four weeks and hung to dry before disintegration was assessed.
Aerated Static Pile Testing
The CASP-only test feedstock was a mixture of residential food waste and yard trimmings. CASP test bags were buried in three different rows. Machinery-assisted burial enabled bags to be buried between 6 and 10 feet deep. The bags remained in the CASP for four weeks and then were moved to a curing pile. In curing, they were buried 1 to 2 feet deep and left for another four weeks. Although machinery helped in burial efficiency, 20 to 40 percent of bags were lost during machinery-assisted retrieval, again due to the sheer volume of material being handled. More than enough test bags remained for statistical analysis.
Analysis And Results
Bags from both sets of testing (HSAD+ CASP and CASP only) were removed and hung to dry before disintegration evaluation. Entire contents of sample bags were sifted through three successively smaller screens, ending with an one-eighth-inch screen. Compostable product fragments collected by the screens were sorted by product type, weighed, and photographed.
The results were a mixed bag, so to speak. The 13 products tested by BSIbio and UBC had lower degrees of break down in the HSAD/CASP trial compared to the CASP-only trial.
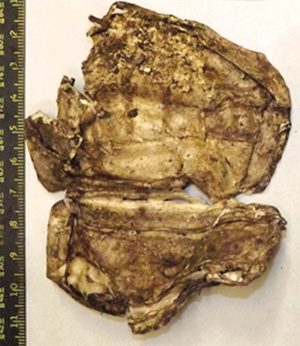
HSAD+CASP testing found fiber products nearly intact at the end of the test. Photo courtesy of BSIbio
The HSAD-CASP mix had a noticeably lower percentage of break down among ingredients being tested compared to the CASP-only mix. Only about 35 percent of the kraft control ingredient disintegrated in both low and high-concentration bags, invalidating the test. In comparison, products made of PLA, such as the biofoam tray, did not show any percentage of break down in either low or high mixes. Although certain product materials had a higher rate of break down, like the fiber bowl made of bagasse, most products tested (9 out of 13) had a disintegration rate lower than 42 percent.
“This was a huge learning experience,” explains Susanna Carson, CEO of BSIbio Packaging Solutions. “The mesh bag method has been applied to many types of aerobic facilities, but it doesn’t work the same way in an HSAD environment. We look forward to building on this work and improving the disintegration test methods for anaerobic digestion.”
The conclusion from these results is that the test method should be refined. Researchers understood that the poor disintegration results had multiple contributing factors, including: material compaction and saturation in the HSAD tunnels, resulting in anaerobic pockets when the bags were loaded in the CASP; process interruptions resulting in premature removal from the CASP, and too-shallow depths of burial which can impact both temperature and moisture levels.
CASP Results
In contrast to the HSAD results, most certified compostable products in both concentrations in the CASP had 90 to 100 percent break down, passing the disintegration test requirements of being under 10 percent of their original weight and less than one-eighth inch in size. In particular, products made of biofoam PLA and amorphous PLA (like the cold cups and deli container) completely broke down in the CASP.
However, the kraft control ingredients broke down to only 70 percent of their original size and weight in low concentration bags, and 60 percent in high concentration bags. Other fibrous materials disintegrated from 60 to 90 percent in both concentrations. Researchers concluded the low disintegration of fiber-based materials was potentially due to high temperatures throughout active composting, with a shorter curing time than regular operations.
Invitation To Test
Results from the HSAD/CASP field study point to the need for more research, testing and collaboration to evolve test methods for anaerobic digestion coupled with aerobic postprocessing. BSIbio is seeking other academics, facility operators and interested parties to advance initial research into testing compostable products for disintegration in HSAD when followed by aerobic processing.
The 2014-2015 HSAD test brought some challenges where unexpected changes in operating conditions (residence time and moisture extremes) led to skewed results, including zero break down of the kraft control ingredients in the HSAD and insufficient break down in the CASP phase. A major takeaway is that AD and composting facility operators wanting to accept certified compostable products need the right recipe and operations to achieve full disintegration.
Although the HSAD test protocol requires further development, the successful mesh bag test method in use for aerobic facilities is in the beta stage and ready for collaboration with other facilities. BSIbio has partnered with the US Composting Councils’ Research and Education Foundation (CCREF) to launch a Canada-United States field testing program. The same basic sample products will be tested across all facility types to enable comparison. Results will be shared in an open-source anonymized database currently under development. This testing program provides an opportunity for composters to participate in an ongoing study into how compostables behave in real-world operations. The aim: a compostable product disintegration test method for widespread application and success.
“The more we understand how and under what conditions these products will disintegrate in a timely manner, the more we can help composters understand their own best practices to accept these products if they choose,” notes Cary Oshins, Education Director, CCREF.
Chantal Strand is BSIbio’s copywriter assistant. Emily McGill is, Manager of Research and Communications at BSIbio (compost@bsibio.com). Facilities interested in conducting their own field testing can contact BSI for more information.