North Florida dairy with 6,100 mature cows and 5,500 replacements installed anaerobic digestion system that is yielding multiple benefits.
Molly Farrell Tucker
BioCycle September 2016
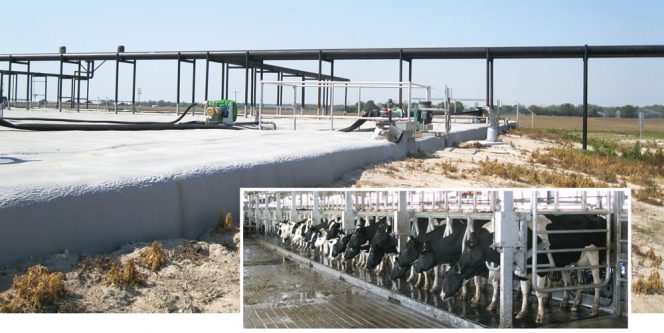
Alliance Dairies installed a DVO Two-Stage Mixed Plug Flow digester (above) in 2012 to help manage manure from its 11,000 head dairy operation. Milking parlor (inset). Photos courtesy of Alliance Dairies
Ron St. John and William “Sandy” McArthur started the dairy in 1990 with 2,000 cows. They now operate the largest free-stall dairy in Florida, with 140 employees tending to 6,100 mature cows and 5,500 replacements on 4,000 acres. Much of the 450,000 to 500,000 gallons of milk produced daily at Alliance Dairy is sold in Publix Supermarkets in Florida.
Each milking cow produces more than 100 pounds of waste per day. The dairy’s two milking parlors operate 24/7, and Alliance’s annual electric bill was averaging $1.2 million. Alliance grows its own feed crops on 4,000 acres. Florida’s climate allows for triple cropping each year. The sandy soil requires fertilization to grow these crops, but its porous nature increases the likelihood of nutrient runoff from fertilizers.
Investing In AD
Four years ago, Alliance installed a DVO-designed Two-Stage Mixed Plug Flow anaerobic digester. St. John, McArthur, and St. John’s daughter, Jan Henderson, who is CEO of Alliance Dairies, applied for and received a $2.1 million federal TARP Green Energy grant to offset the $8.5 million cost. “We knew of DVO in Wisconsin,” says Charlie Smith, Alliance’s Office Manager. “It had around 100 digesters in place around the country so we weren’t the first.”
The digester was specifically designed for Alliance’s freestall barn flush system. “We use a lot of water because we flush our barns,” explains Smith. “This required us to build a larger digester, because the water makes the manure less concentrated, which reduces the ability to create methane gas. Other farms with less access to water scrape the manure out of their barns, which leaves the manure more concentrated.”
Construction began in April 2012. DVO was the design engineer and Martin Machinery of Missouri sold the dairy the motors and generator. Testing to satisfy the Green Energy grant requirements was completed, and the digester system began producing electricity in January 2013.
Alliance Dairy uses sand bedding for the lactating herd. “The milk cows like it because they can move around in the sand and make it conform to their body shape,” notes Smith. “Clean dry sand is the gold standard when it comes to dairy cow bedding.”
The barns are flushed and then scraped with a rubber tire scraper down to a sand lane where more than 80 percent of the sand is reclaimed. At the end of the sand lane, the manure-laden flush liquid goes one of two ways — either to the methane digester or to a drum composter system.
The flush liquid headed to the digester first goes to a mixing pit where screen separators drop solids from the flush into the side of the pit that feeds the digester. Liquids flow to the other side of the pit and then back to the flush tanks to be reused to flush the barns.
Biogas Power
Retention time in the digester is 21 days. Methane gas powers a 1-megawatt genset located in a building next to the digester. Biogas is conditioned to remove hydrogen sulfide prior to entering the engine. “We struggled with the original Spanish motor provided by Martin Machinery for two years,” says Smith. “It threw a rod twice. We replaced it with a CAT motor in January 2015. The oil in the motor needs to be changed every 400 hours as we are not producing a clean gas.” Alliance does all its own maintenance, which is a full-time job for one employee.
Drum Composter For Bedding
The portion of the scraped manure that doesn’t go to the AD system is directed to a large drum composter that converts the manure solids into animal bedding. The drum composter, manufactured by Integrity Ag Systems, is 30 feet long and 10 feet in diameter.
The scraped manure is separated mechanically by two Integrity thickeners and then passes through a screw press to remove liquid. The manure fiber solids are loaded into the drum where they stay for 24 hours. Material reaches 150°F to destroy any weed seeds and live bacteria. “The solids that come out of the composter are relatively dry and virtually odor-free,” says Smith.
The farm uses a portion of the solids to bed its dry cows and springers. In addition, each week from November through April, Alliance Dairies sells two semi-truck loads of the manure fibers to Black Kow, which sells bagged composted manure throughout the South.
Liquid Stream
Liquid effluent from the digester is used to fertilize 2,000 acres of the crops. The digested effluent is piped from the digester through one of two very fine screen separators, then sprayed on the fields through drop down irrigation pivot nozzles.
Alliance has found that crop yields are better when using digested manure. “The process converts its nutrients from an organic form to an inorganic form, so the nutrients are much more available to the plants,” explains Smith. “Three crops are grown on sandy soil with just the manure water: corn, then sorghum, and then rye grass, oats and small grains in winter. We are getting nearly 24 tons/acre of corn silage, which is a really good yield.” No additional N-P-K fertilizers are used on the crops.
The digester removes most of the odors from the effluent, he adds: “I drove by the end irrigation gun today and couldn’t smell it. We have neighbors all around and they can attest to it.” He notes the old irrigation pivots that used to spray the undigested manure left a distinct odor.
In 1990, Alliance Dairies became the first dairy in northern Florida to be permitted by the Florida Department of Environmental Protection (FLDEP). “An industrial wastewater permit from the state of Florida is required when milking over 800 cows,” says Smith. To get the permit, Alliance had to submit a comprehensive nutrient management plan and remain in compliance with it.
Using the liquid effluent as fertilizer is a double-edged sword, he explains, because although nutrients are taken up by the plants, with heavy rain events the liquid can leach more quickly into the soil and contaminate groundwater. Alliance has seven monitoring wells downgradient to the irrigation pivots to measure how the crops and pastures are absorbing the nitrates. The dairy tests the wells every three months and sends the results to FLDEP. It also installed soil moisture probes to determine when the crops need to be watered.
Alliance Dairies was recognized for its sustainability initiatives when it received an Outstanding Dairy Farm Sustainability Honorable Mention from the Innovation Center for U.S. Dairy’s 2015 Sustainability Awards.
Molly Farrell Tucker is a Contributing Editor to BioCycle.