Top: Aerated static pile bays used for food scraps and manure composting at Kingdom View Compost. Photo by Robert Spencer
Robert Spencer
Situated in Vermont’s Northeast Kingdom region, Eric Paris and his wife Cathy have operated Tamarlane Farm, a small dairy farm in Lyndonville, for over 40 years, after taking it over from Eric’s father and mother in 1980. In 2003, they completed conversion to an organic dairy through Vermont Organic Farmers, feeding a grass only diet to the cows, and supplying milk to Organic Valley Cooperative. The husband-and-wife team now milk 35 cows, down from the 70 in previous years. Like many small dairy farms, their operation has diversified over the years, raising beef cows, vegetables, and hay.
The Paris’ family is close by, and provide help on the farm when needed. “With support from our family, Cathy and I recently decided to maintain a small dairy herd, but our primary focus is expanding the manure and food scraps composting facility,” explains Paris. “By working with local haulers and the solid waste district we plan to support and capitalize on Vermont’s mandatory food scraps diversion law, Act 148.”
They were an early adopter of food scraps composting, starting in 2005 prior to the state passing Act 148 in 2012. The composting business, known as Kingdom View Compost, has a facility certification from the Vermont Agency of Natural Resources (VT ANR). With proximity to Burke Mountain ski resort and the Northeast Kingdom (NEK) network of mountain biking trails, the area has numerous inns, restaurants, and bed and breakfast establishments that are required to recycle food scraps. Approximately 12 tons/week of food scraps are delivered by area haulers and generators, who are charged $2.75 per 48-gallon tote, full or not. Kingdom View Compost’s sources of food scraps include a prison, nursing home, hospital, supermarkets, bank, slaughterhouse, and a meat processor. In addition to its dairy manure, the facility processes manure from the county fairground and horse farms.
Black Dirt Farm, another northern Vermont composter, operates a collection program, and brings food scraps from generators near Tamarlane Farm to Kingdom View Compost rather than hauling it 20 miles to its own facility in Stannard. About 3 to 4 tons (30-40 totes) are tipped at the site once a week. Tom Gilbert, owner of Black Dirt, says that tonnage has decreased in the past two years because of competing collection by depackaging facility haulers, a state-wide situation.
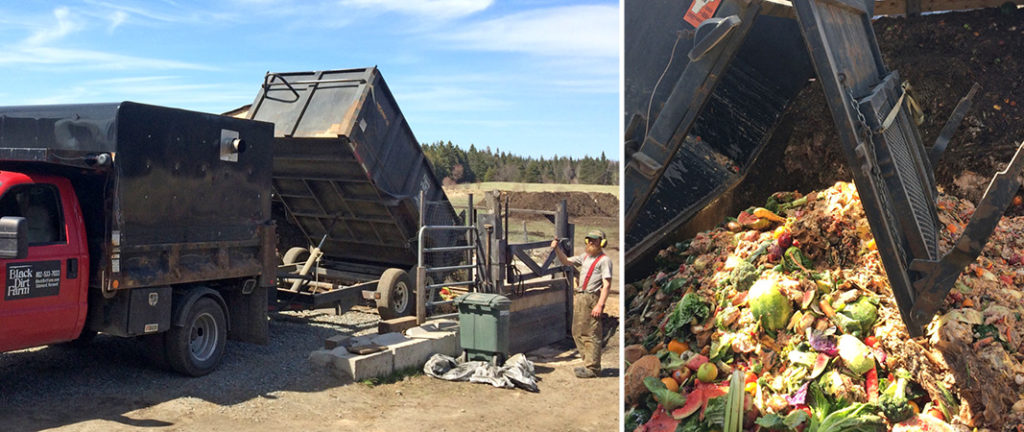
Black Dirt Farm collects food scraps in the Northeast Kingdom and takes them to Kingdom View Compost for processing. Photos courtesy of Black Dirt Farm.
“Eric and I have partnered starting when I ran Highfields Center for Composting and did the design and permitting of his site, as well as the development of collection programming in the region,” notes Gilbert. “It’s been wonderful to be with Eric and Cathy for nearly 20 years doing this work together, over which time our relationship has grown into new spaces and continues to flourish.” He adds that Black Dirt Farm runs a “rigorous source separation program in its collection operation. We are deeply motivated to protect Eric and Cathy’s soil, as well as our own, and that of our customers. Our commitment to clean food scraps is a reflection of the authentic relationships these systems are built on.”
Solid Waste District Collaboration
Another long-term supporter of Tamarlane Farm and Kingdom View Compost is Paul Tomasi, Executive Director of the Northeast Kingdom Waste Management District (NEKWMD), the region’s solid waste management agency. “Eric Paris is a pioneer in regard to composting in the NEK,” explains Tomasi. “I remember the day in January 2007 that he started receiving food scraps from the District’s new collection program. It was freezing cold and I was on the first pick-up. Our thought was if we could make it work in January, we could make it work in July. Eric has been composting ever since.”
Tomasi adds that the NEKWMD has been engaged in diversion of food scraps from landfill disposal since 2007. “Initially a commercial/institutional route was established and food scraps were hauled and delivered to Kingdom View Compost by the NEKWMD,” he says. “The District no longer operates a collection program as private haulers have come on line. We slowly began adding food scraps collection facilities to our local transfer stations and recycling centers. The NEKWMD currently offers food scraps collection at 25 locations throughout the District, providing collected feedstocks to four compost processing locations, all on farms. In addition to Kingdom View Compost, the sites are located in Irasburg, Lyndon, and Sheffield. The NEKWMD diverted just shy of 800 tons of organic material in 2021.”
In June 2021, the Vermont Department of Environmental Conservation awarded NEKWMD a $250,000 grant to expand organics processing capacity in the NEK. Tamarlane Farm/Kingdom View Compost was one of five recipients to receive a portion of that grant. It was awarded $60,000 to purchase a mobile compost screener from EZ Screen. No match was required, however, the cost of the screener exceeded the grant award by almost $4,000, which the farm covered. The District will maintain ownership of the screener for 10 years, after which it will be the property of Kingdom View Compost. The unit is scheduled to be delivered soon.
Currently the unscreened compost is mostly utilized on the farm, with some sold to gardeners and landscapers. As a certified organic farm, the compost is used to enhance soil fertility and build soil organic matter levels. The high cost of imported organic fertilizers motivated Paris to produce compost for application on Tamarlane Farm’s owned and rented acreage.
Challenging Winter Conditions
The composting operation is located about a quarter mile from the dairy barn, and Paris hauls manure to the site with a manure spreader. A Caterpillar IT18 loader with a 2.5 cubic yard bucket is used to mix the input materials, and move materials on and off the compost pad.
Kingdom View Compost originally utilized windrows, but transitioned to aerated static piles (ASP) about eight years ago in large part due to challenges with cold winter temperatures, snow, and the long duration of winter from November to April. “The compost process basically stopped most winters as cold temperatures penetrated the relatively small windrows built by the manure spreader on a gravel pad,” recalls Paris. “For several years that was not a serious issue since we were recycling our farm’s manure and a relatively small amount of food scraps.”
However, with increasing quantities of food scraps being processed, Kingdom View Compost received technical and financial assistance in 2014 through the U.S. Department of Agriculture’s Sustainable Agriculture and Research (SARE) program to conduct a pilot using ASP technology. Working with a grant from VT ANR, Compost Technical Services and the Highfields Center designed a small ASP system using positive aeration. Although the aeration improved operations, the cold weather was still an impediment to the composting process.
To further address the cold weather challenges, Paris started working with Agrilab Technologies, Inc. (AGT), a Vermont company with a proprietary compost aeration and heat recovery (CAHR) system that was operating successfully on other manure composting farms and commercial facilities, including Vermont Natural Agricultural Products in Middlebury (VT). With grant assistance from the Vermont Agency of Agriculture, Food, and Markets, as well as the Vermont Clean Energy Development Fund, a loan was obtained to finance the balance of the $220,000 project through the Vermont Community Loan Fund.
Construction of the AGT facility started in fall of 2020, and was finished in early December, just as winter arrived in full force. The installation includes a concrete pad with four aeration zones, HDPE aeration pipes, leachate tank, a blower that operates in both positive and negative aeration, and the AGT Compost Hot Skid 250-4R. The system has programmable controls for four reversing aeration ports, sensors for temperature, oxygen, and air flow, as well as remote internet access.
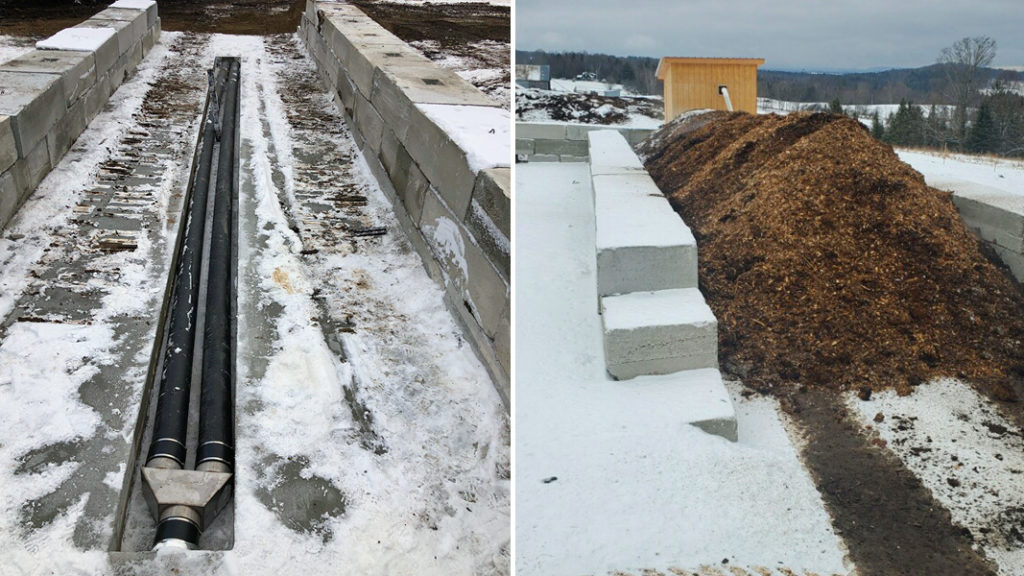
The facility has four aeration zones with a blower that operates in negative and positive modes (left is an aeration trench with pipes and manifold). The first batch of material (right) was loaded into a bay in December 2020. Photos courtesy of Agrilab Technologies, Inc.
“By drawing hot moist vapor from one active compost pile and directing it to a new pile, the process gets a jump start on heating up to composting temperatures,” explains Brian Jerose, President of AGT. “Just a few weeks after start-up in December 2020, 153°F vapor was being drawn from the first zone into a fresh pile in another zone.” A plenum of coarse wood chips is laid on top of the aeration pipes prior to placing the fresh feedstocks for composting. Paris adds that with the aeration system, he has been able to cut back on the proportion of wood chips utilized prior to having the ASP system.
“I’m very pleased with the performance of the system over the past two winters and have more than doubled our composting capacity,” he notes. The food scraps, manure and wood chips are mixed in a 2:2:1 ratio respectively, and stockpiled until there are about 125 to 150 cubic yards, enough to fill an aeration zone. One unexpected problem was that fat and grease in the meat processing material settled out in the aeration sump traps, significantly reducing air flow and requiring periodic maintenance. Paris is working with the grocery store meat department to minimize loads with high fat content. Future plans include adding an adjacent equipment storage and compost bagging garage, as well as a small greenhouse. Pipes have been run from the AGT Compost Hot Skid 250-4R to their planned locations to provide renewable thermal energy from the compost to assist in building heating and product drying.
Bob Spencer has been a Contributing Editor for BioCycle for over 30 years. As Executive Director of the Windham Solid Waste Management District in Brattleboro, Vermont, he operates a food scraps composting facility.