Robin Szmidt
The city of Aberdeen, located on the Northeast coast of Scotland, UK, looks out to sea where deep below the waves of the infamously hostile North Sea, oil was found in the late 1960s. The ‘black gold’ formed the basis of decades of prosperity in Aberdeen, turning it into the offshore oil industry’s capital. Previously, the city had been something of an ‘island’ with relatively difficult transport links to other large Scottish population centers some hours distant. In earlier times, the city had relied on traditional industries, such as high quality agriculture and fishing. Today Aberdeen’s population is around 230,000 and the city is a dynamic blend of modern and traditional — the oil sector, while still extremely important, is perhaps itself seen increasingly as yesterday’s powerhouse.
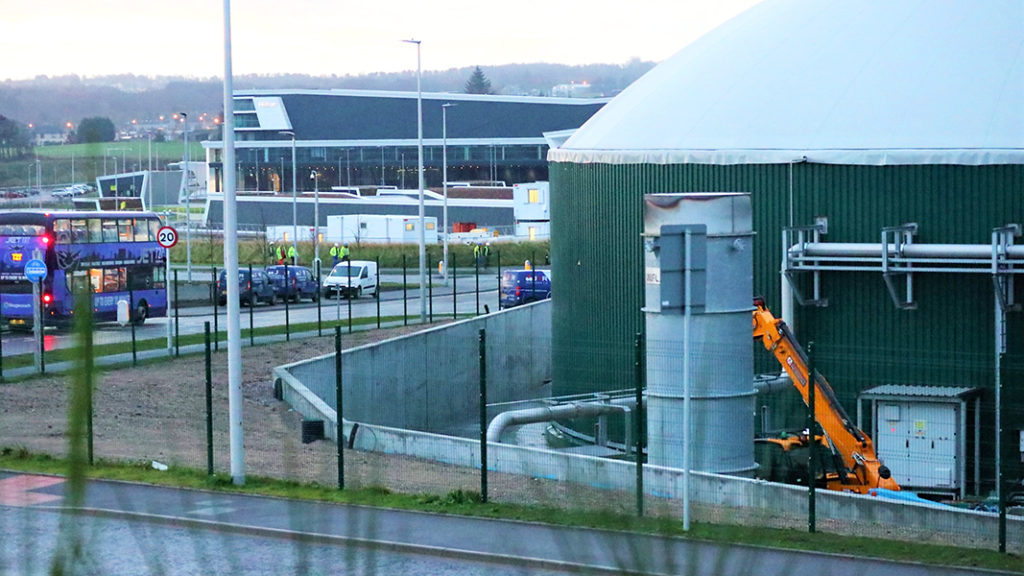
Heat and power produced with biogas are supplied to the nearby events center (in background). Photos by Robin Szmidt
In 2016, with an increasing awareness of its own environmental footprint, Aberdeen City Council (ACC) published “Powering Aberdeen: Aberdeen’s Sustainable Energy Action Plan.” Around the same time, a decision was made to replace the aging conference and exhibition center with a state-of-the-art venue. The new strategy included a vision to integrate an anaerobic digestion plant at the new site, including heat and power not only for the events complex but also for new hotels that would be built.
ACC went to tender for construction of the AD system in 2018. The facility would become not only the power supply for the development site originally envisaged, but also would take on a pivotal role in the waste strategy of the city and its transport, while integrating with farming in the surrounding countryside through land application of high quality digestate.
Austrian company Thoeni Industriebetriebe GmbH was appointed lead contractor for construction of the AD facility in late 2018. Downstream contracts were also awarded for long-term operation to Future Biogas, Ltd, and to Keenan Recycling Ltd., a local company, for waste collection and delivery to the AD plant. Construction began in May 2019 with a deadline of gas-to-grid of January 2020.
Facility Design
Details about the facility are in the “At A Glance” sidebar. ACC had begun the process with a concept of what the site would look like and had secured planning permission to begin the project. However, this has evolved substantially to adapt to needs of new neighbors — so-called sensitive receptors — that include Aberdeen airport, local housing, hotels and The Event Complex Aberdeen (TECA).
The plant is designed to process a range of curbside collected food waste from Aberdeen City using 16.5 ton side-lift collection vehicles operated by Keenan. Households with food only collection, and industrial and commercial food waste generators, are serviced. Food waste is preprocessed at two sites, each equipped with an Atritor depackager and post-separation 12mm macerator. The slurry is delivered in a road tanker to the AD on a just-in-time basis with buffer capacity of about 2 days’ feedstock. It is metered directly to the digestion process by the control computer. Solid agricultural vegetable wastes and distillery waste ‘draff’ are delivered to the flat bunker area within the air-controlled reception building which includes a double door ‘airlock.’ Solid material is lifted by automatic crane and deposited in the weigh-cell equipped feed hoppers, which then direct it to the two primary digesters.
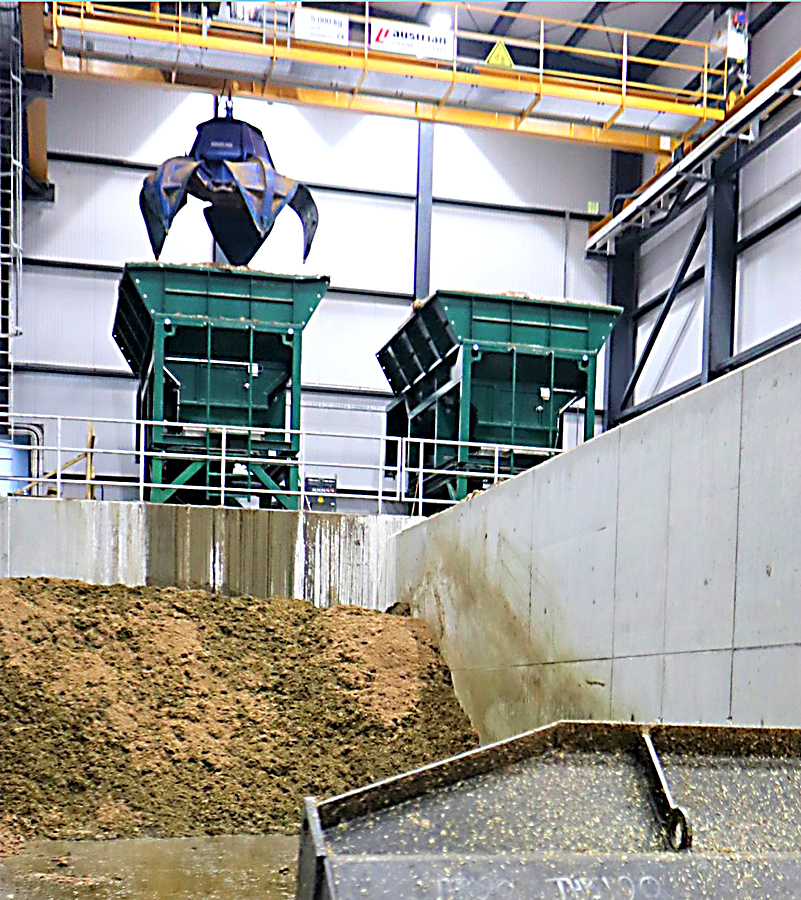
Solid material is lifted by automatic crane and deposited in the weigh-cell equipped feed hoppers, which then direct it to the two primary digesters.
The digesters are equipped with the unique Thoeni TNV mixing system. The turning paddles are slow-speed, high torque, allowing a relatively high dry solids content of approximately 14% in the digesters (a so-called semidry process). The inertia of the mix system ensures low power consumption of the agitators and minimum water consumption. The latter is really important as the Aberdeenshire countryside includes excellent arable land that would benefit from high quality digestate, but also experiences high rainfall. Thus minimizing liquid output was key in system selection.
The digestate is pumped to a secondary digester, then to the pasteurization unit prior to dewatering. Solids (approximately 28% dry solids) are directed to the vehicle-loading bay for agricultural use while liquids (about 7% dry solids) are sent to the final buffer storage tank before distribution to farms.
Biogas Utilization
The site was designed to be self-sufficient in electricity due to limited grid export potential and procurement of a 2G 499 kW CHP (combined heat and power) engine that meets the facility’s parasitic demand for heat and electricity, with surplus going to the grid. The majority of the raw biogas is upgraded to biomethane using an HZI membrane system prior to downstream utilization.
There are two options for biomethane transmission. Most is injected into the gas grid via the grid-entry point after final sampling, odorization and propane calorific-value balancing. The remaining biomethane is directed to the TECA events venue and energy center, which has a dedicated CHP system that generates heat for the buildings and powers a hydrogen reformer. The hydrogen can then be utilized by the city bus network, one of the largest hydrogen bus fleets in the UK and Europe.
“We wanted to make TECA a world-class facility not only for the types of entertainment and conferences it can accommodate but also for renewable energy,” notes Aberdeen City Council hydrogen spokesman Councillor Philip Bell. “The AD plant at TECA contributes to the city’s Net Zero Vision which supports Aberdeen’s leading role in energy transition. The city is already leading the way in the UK in developing and deploying renewable technologies to combat global warning and climate change.”
Although the Aberdeen facility achieved gas-to-grid injection in January 2020, site completion was significantly delayed by COVID as the international construction team was severely restricted in many ways. Nonetheless the site is now receiving waste and was at full capacity by October 2020.
Energy Supplier In An Urban Environment
The integrated nature of AD as an energy source in an urban environment is an environmental challenge with the very neighbors that want the power being potential objectors! The site has therefore been designed to the very highest standard in terms of environmental controls. Positive pressure ionization and activated carbon filtration supplied by CSO Terminodour are used for odor control. Key elements of the site are located with purpose-designed sound mitigation barriers and the facility itself is severely restricted in terms of water discharge rates to mitigate against contributing to local flood risk. The bunded site discharges surface rainwater first to a purpose-built buffer pond before downstream clean water only discharges to a local water course.
The AD site is located only a few hundred meters from the southern end of the main runway of Aberdeen airport — one of the busiest in the country, not only with fixed-wing take-off and landings but also seemingly continuous helicopter traffic serving the offshore oil industry. The National Air Traffic Services (NATS) required specific design changes for the AD plant, including modifications to the lightning protection system supplied by LPS and the construction of a ‘waved’ solid fence on a nearby raised area to ensure that flight radar didn’t show up a series of confusing circular profiles. This made the Aberdeen site the first known ‘stealth’ AD facility!
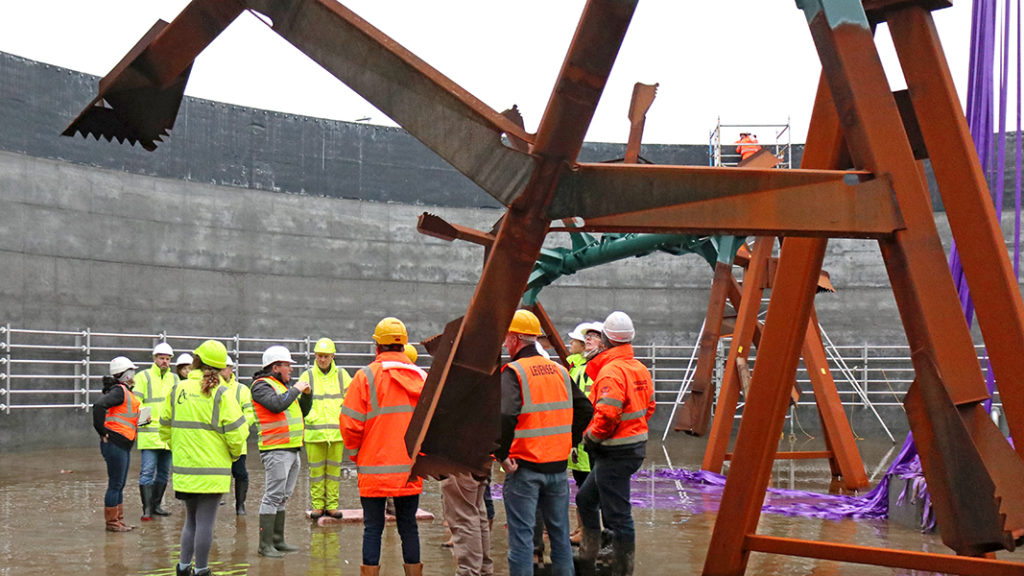
The Thoeni TNV mixing system has slow-speed, high torque turning paddles (seen while digester was in construction) that accommodate a relatively high dry solids content of approximately 14% in the digesters.
Like any new initiative, it has attracted a lot of interest and the site received its first technical visitors from the UK Renewable Energy Association in winter 2019 during construction, giving visitors the rare chance to see the scale and detail of the Thoeni TNV mixer system before tank-filling. The project also includes educational aspects on topics such as food waste and recycling. Although engagement with schools has been limited by COVID, the project team has helped develop web-based learning material for junior and senior schools, information for the University of Aberdeen at undergraduate and postgraduate level, and factsheets for farmers.
Robin Szmidt, PhD, is Director of Target Renewables Ltd.