Top: Adrienne Huckabone and Ryan Green (above) founded Happy Trash Can in 2016. Photo by Kene Sperry
Nora Goldstein
Ryan Green and Adrienne Huckabone cut their composting teeth on the East Coast, working in both agricultural and community composting settings. Green worked at the New York City Compost Project hosted by the Lower East Side Ecology Center in Manhattan; Huckabone was a volunteer at their neighborhood community garden’s composting operation.
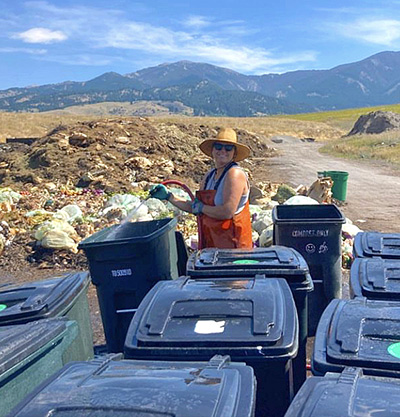
Adrienne Huckabone washes carts used by commercial accounts. Tipped food waste (in background) is blended with ground yard trimmings before being placed under the GORE cover.
In 2016, the husband-and-wife team decided to move to Bozeman, Montana, Huckabone’s hometown, and offer collection and composting of source separated organics from residents and businesses. “We wanted to move to Bozeman and do composting, but we had never run a business before nor were we certain that the culture would embrace our services,” recalls Green. “For the first three years, we weren’t sure our business would succeed. Adrienne and I both were working other jobs. Then, the business really took off!”
Their company, Happy Trash Can Curbside Composting, LLC, services residential and commercial customers in Gallatin and Park Counties, Montana. Participating households receive a 5-gallon bucket with BioBag compostable liner bags. Collection is offered biweekly for $15/month. Residents in communities further away from Bozeman (“extended zones”) are charged $20/month for biweekly collection. The company also offers a subscription-based food waste drop-off option. Commercial kitchens and office clients can select the service that best fits their needs, e.g., cart size, collection frequency, etc. Happy Trash Can’s (HTC) team helps with staff training, custom signage, and presentations. All food waste is accepted, along with BPI certified compostable foodservice ware and bags.
Initially, Green and Huckabone set up their composting operation on a farm, but quickly outgrew the space. In 2018, HTC collaborated with Sustainable Generation to serve as a demonstration site for the smaller scale SG Mobile® GORE® Cover aerated composting system. A 100-foot-long cover was set up on a commercial property that HTC rented. The demo illustrated the capability of the system to compost increased tonnages on a similarly sized footprint. In January 2021, HTC moved its operations to the City of Bozeman’s Story Mill Convenience Site, situated on a closed landfill. “We compost yard trimmings collected by the city with the food waste,” explains Green.
Food Waste Flow
HTC has about 1,200 residential subscribers and about 75 commercial clients. It collects about 15 tons/week of food waste, on average. In addition, Montana State University (MSU) collects food waste from its campus kitchens and tips a 20 cubic yard roll-off once a week at HTC — equivalent to about 10 to 15 tons weekly throughout the school year. “With ample signage in the pre and postconsumer areas, we find that we have low contamination in the material received,” notes Huckabone. “We also work closely with MSU’s recycling coordinator and communicate when a contamination issue occurs.”
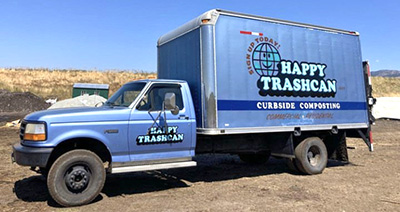
A box truck is used to service commercial accounts. All food waste is accepted, along with BPI certified compostable foodservice ware and bags. Photos courtesy of Happy Trash Can.
A heavy-duty pickup truck with a trailer attachment is used to service residential accounts. Filled buckets are emptied into totes on the trailer. “Prior to the pandemic, we would do bucket swaps, but then the number of households serviced skyrocketed overnight when COVID hit,” she adds. “It doesn’t pencil out to a livable wage to wash hundreds of buckets a week.” A box truck with a lift gate is used for commercial accounts. Full toters are swapped out for clean toters at each pick up as HTC does not have the ability to dump toters on the route.
As the quantity of food waste tonnages grew, so did HTC’s composting system. The company leases four 100-foot GORE covers, in addition to the original one. The 100-foot-long covers accommodate about 300 to 400 cubic yards of material per batch. Composting under the covers is done in two 30-day phases. After the initial 30 days, the covers are removed and the piles are turned with a 1.5 cy loader bucket. HTC leaves the above-ground aeration pipes in place and turns the material “as best we can,” says Green. Following those two phases, material is moved to a curing area (not aerated) for about three months. After curing, compost is screened with a static vibratory screener; HTC is planning to upgrade to a trommel to mitigate bottle necks in screening during the spring. “We need to sift sooner and faster,” he adds.
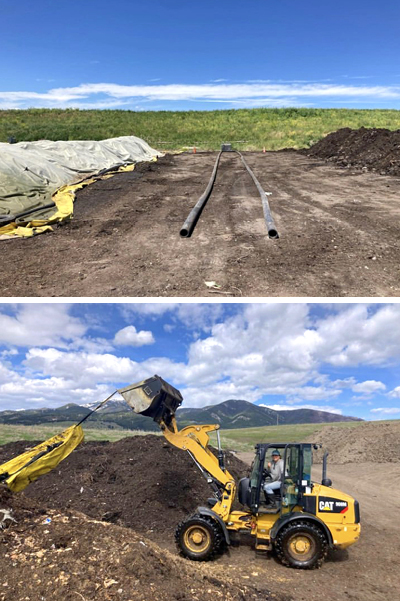
Sustainable Generation’s SG Mobile® composting system (top) is used for the active composting phase. Curing is done in uncovered windrows.
Household accounts receive about 5 gallons/month of compost as part of their subscriptions. The majority of the compost is sold to flower farms and other local farms and larger community gardens that use it for vegetable production. Some is sold to residents with larger gardens. HTC focuses on farms, versus the landscape market, because Green’s and Huckabone’s mission is to close the loop locally as part of a Fork-to-Farm” movement. HTC “constantly sells out” of compost, they note. Once the trommel screen is procured, they plan to screen and broker yard trimmings compost that has been stored elsewhere on the site by the City of Bozeman.
Green notes that HTC has low contamination rates in the residential and commercial streams. “We do a lot of outreach and education with our clients to ensure as clean a stream as possible,” he says. “Following the initial training with our commercial accounts, we will retrain as necessary.” The certified compostable products disintegrate well during composting and curing. “We have been managing this material in our feedstock stream for the past five years and have helped move many clients away from single-use plastics to certified compostables,” he adds. “Compostable products are an important option in this region because there are not recycling facilities for single-use plastics.”
Public-Private Partnership
Executing a contract with the City of Bozeman to operate at the Story Mill Convenience Site will cement the informal relationship HTC has had with the city to date. There is ample room to expand composting operations and accommodate compost curing. “We are moving through tons and tons of material on behalf of the city,” says Huckabone. “We don’t receive a tipping fee to process incoming yard trimmings. They are processed with the food waste from MSU and we receive payment from the city per cubic yard once its yard trimmings are composted.”
Currently, the City of Bozeman collects residential yard trimmings seasonally from May to September. The City Council would like to see the city offer residential food waste collection on a year-round basis. A rate study was conducted by a consultant to evaluate pricing and fees for solid waste services, including curbside collection of food waste. Huckabone and Green embrace the curbside plan, noting that “in the long run, we want to get out of the hauling game and focus on processing.”
A pilot curbside collection program is planned for the summer of 2023 in several neighborhoods. Food waste and yard trimmings will be commingled in the same cart. HTC will encourage its residential customers in the pilot neighborhoods to join the city’s program. “The Bozeman solid waste department has been reluctant to offer year-round organics collection,” explains Green. “But our successful working relationship has given them confidence it will work.”
In addition to Huckabone and Green, HTC has two full-time drivers, one for the commercial route and the other for residential. They also have several part-time employees, e.g., a staff person to run the farmer’s market drop-off stand during the summer. Huckabone, who manages the business, will pinch-hit as a driver as needed. Green focuses on the composting side of the business.
“Looking back, we should have hired staff a lot sooner than we did,” reflect Huckabone and Green. “It was just us for the first three years. We just were uncertain about our business viability. But we have created jobs and pay livable wages, and our employees learn the system and take work off our back. We also believe it would have made sense to invest in better equipment earlier on. When we bought a new loader last year, it was the first time we took out a large loan. We’re not intimidated by taking on a little debt knowing we have a good business model.”