Food processor installs anaerobic digester primarily to treat acid whey from its Greek yogurt production. Power generated offsets about 10 percent of plant’s electric load.
Alle Crampton
BioCycle September 2016
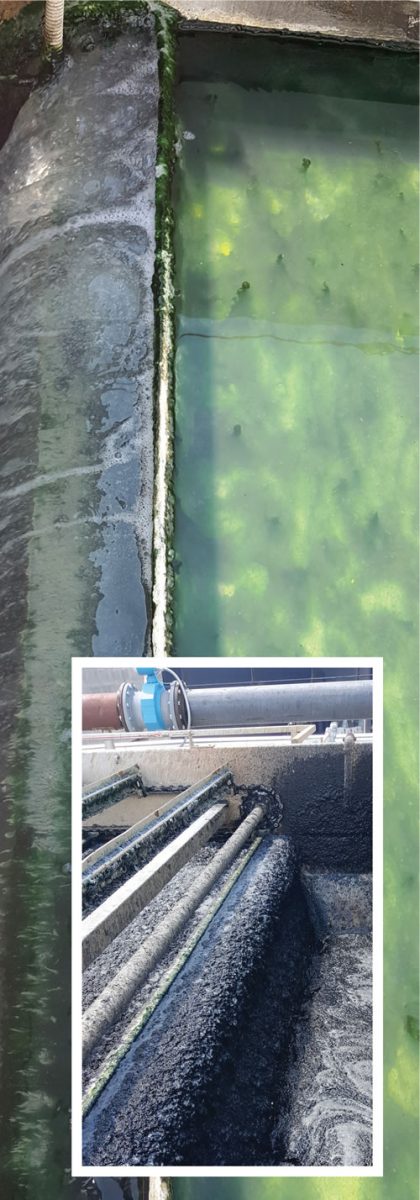
Water from the anaerobic process is shown flowing the opposite way as the digested sludge (inset). Some solids to the right can be seen in main photo, but overall the water is clear. Photos courtesy of General Mills Incorporated
Opened in 1979, the Murfreesboro plant was originally used to make frozen pizza food items. In 2004, General Mills added production lines to produce Yoplait yogurt goods, including Greek yogurt. Production of Greek yogurt requires three gallons of milk to make one gallon of Greek yogurt (vs. 1 gallon of milk to make 1 gallon of regular yogurt). It involves separating whey from the heavier cream in milk; 60 to 70 percent of the milk becomes an unusable waste by-product called acid whey that is either landfilled or land applied. The General Mills plant was not allowed by the Murfreesboro Water and Sewer Department to increase its BOD loadings, thus the yogurt whey was collected into storage tanks and then trucked off site for land disposal.
Supported by Chief Sustainability Officer Jerry Lynch, the plant and corporate teams worked to find an improved solution to managing the Greek yogurt by-products. In late 2014, the Murfreesboro plant received corporate approval for construction of an anaerobic digester (AD), and connected energy recovery facilities. The project was partially funded by a federal Investment Tax Credit.
“Prior to the digester being added, General Mills still produced high quality effluent that was able to be reused,” notes Steve Huffman, Murfreesboro Water and Sewer Department’s Pretreatment Coordinator. “The addition of the anaerobic digester greatly reduced the sludge loading while still maintaining the high quality effluent. Sampling analysis for total suspended solids (TSS) and biochemical oxygen demand (BOD) rarely show concentrations higher than 100 ppm. The dedication to their pretreatment plant has prevented any loadings of TSS and BOD to the publicly owned treatment works.” The AD facility enables General Mills to treat all of the yogurt whey to BOD values that are always within permit limits rather than having to truck the whey off site.
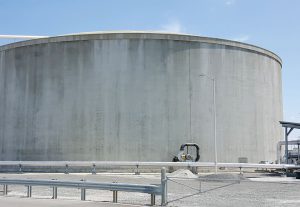
The 6.5 million gallon anaerobic digester installed at the General Mills Inc. plant in Murfreesboro (TN) began operating in 2014. Photo courtesy of General Mills Incorporated
AD Treatment
Permitting for the AD facility was received from the Tennessee Valley Authority. Key partnerships with Murfreesboro Electric Cooperative and the Tennessee Department of Environment and Conservation helped with facilitating the permitting process. Installation began in 2012, and in July 2014, the 6.5 million gallon, continuously stirred anaerobic digester began operating at full capacity. The concrete reactor tank was constructed by Crom.
The digester contains self-renewing anaerobic bacteria that break down the whey and purify the BOD in the water. The process produces a nutrient rich sludge mixture that goes through a Dissolved Air Flotation (DAF) system, which processes approximately 600 gallons per minute, removing pollutants and solids. FRC Systems, a wastewater treatment solutions provider, constructed an open-style DAF system with 510 square-feet of free surface area and a solids loading rate of 5.65 lbs/sq. ft./hr.
Wastewater entering the DAF system “collides” with a stream of recirculated clarified water from the DAF that is super saturated with dissolved air. As the two streams blend together, microscopic bubbles attach to solid particulates, giving them enough buoyancy to rise to the surface of the DAF tank. These digestate solids bind together and accumulate in a floating layer on the top of the DAF tank. A skimmer gently pushes the floating layer toward a discharge hopper.
Any solids that don’t float will sink to the bottom of the DAF tank, which is shaped like a “V.” Settled solids are concentrated and discharged by an automatically controlled pneumatic drain valve. These solids can be put back into the anaerobic digester, or into a separate holding tank. The clarified water flows in a separate direction out of the tank via an under-over weir on either side of the DAF unit. Some of this water is used in the recirculation loop while the rest flows out of the vessel to an aerobic treatment phase.
The digestate solids skimmed off the top are not dewatered beyond the DAF surface removal process; solids content is around 7 percent. The solids contain higher concentrations of plant-available nitrogen and phosphorus compared to manure. They can be put back into the anaerobic digester, or used for agricultural purposes.
Aerobic Treatment
The anaerobic digester and DAF system pretreat all Yoplait and Pillsbury processing wastewaters. The aerobic system that treats the clarified water can also be used for finishing water and to augment other types of treatment. “It’s a separate system using a different set of microbes to continue to clean the water,” explains Dexter Dean, Site Environmental Engineer at the General Mills’ Murfreesboro facility.
The water is discharged to either the sanitary sewer or to Indian Hills, a local golf course, which uses it in its sprinkler system to distribute to certain areas within the course., says “It has been a great partnership so far,” notes Jim McElyea, Indian Hills’ course manager. “We are looking to further the partnership by expanding our irrigation, which will allow us to use more of the water through a larger part of the course. The water has some good qualities and the course will be more aesthetically pleasing, especially when the natural areas become more lush and green. This started out as a possible cost savings project, but it has really turned into environmental stewardship for us and how to best reuse the water General Mills provides.”
Adds Dean: “This anaerobic digester project definitely expanded our partnerships. We needed to work very closely with the city water plant and the local electric utility. Our wastewater flow to the city is consistently cleaner than it was before the project.”
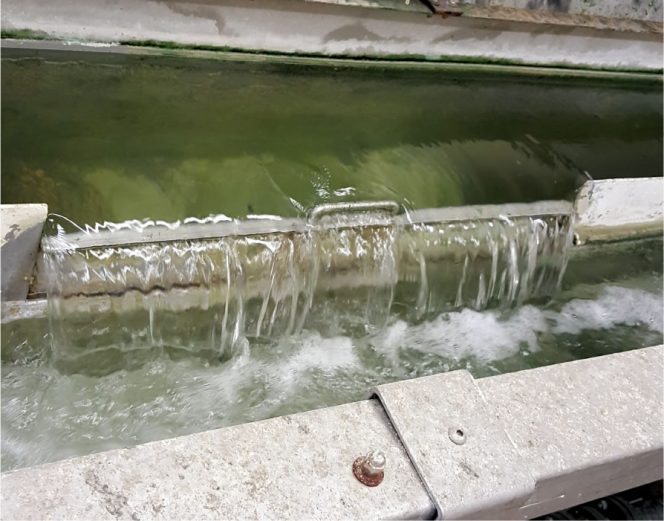
The sludge mixture flows from the digester into a DAF tank that separates the liquids and solids. Clarified water from the DAF tank goes through aerobic treatment prior to being discharged to the sanitary sewer or to a local golf course where it is used for irrigation. Photo courtesy of General Mills Incorporated
Results And Benefits
The biogas, which is approximately 60 percent methane, is used to power a Caterpillar engine that generates about 1.6 megawatts of electricity — supplying slightly over 10 percent of the Yoplait yogurt processing facility. Waste heat from the generator is recovered, heating the water necessary for sanitation throughout the plant. This translates into decreasing natural gas use by 10 percent.
Murfreesboro Electric installed a switching mechanism to ensure that the power generated does in fact supply the plant and does not reenter the grid. The anaerobic digester generated 3 million kilowatt hours of electricity in the first four months of operation, which resulted in a 9,000 metric ton decrease in carbon dioxide as well as a significant decrease — $2.4 million — in the plant’s annual utilities bills.
This project keeps 15 to 20 tanker trucks filled with unusable whey off the roads daily, decreasing diesel fuel consumption by 25,096 gallons, and returning over 34 million gallons of clean water back into the watershed annually. Approximately 2,000 acres of farmland were able to return to normal agricultural use, since there is no longer a need to apply all of the by-product to the land. “General Mills has been on the forefront of industrial pretreatment,” says Huffman with the City of Murfeesboro, “and a great example of what a good steward to the environment really is.”
Alle Crampton is with the Tennessee Department of Environment and Conservation’s Office of Sustainable Practices.