Top: While the site for this large scale composting facility originally didn’t have immediate neighbors, subsequent development and odor management challenges ultimately led to its closure. Photo courtesy of Coker Composting & Consulting
Ron Alexander
Commercial-scale composting in the U.S. has enjoyed steady expansion over the past 40 to 50 years. Several times, industry growth spurts have occurred because of federal or state regulation. Interestingly, whether state, provincial, or national regulation is enacted which seeks to expand the organics recycling infrastructure, the actual development of said infrastructure is always slowed down by state and local regulations and siting issues. While these industry growth spurts are welcomed — they help to promote the recycling of so called “wastes,” as well as create sustainable soil building products — history has shown that when growth spurts occur, expensive mistakes often follow. With implementation of SB 1383 in California (the Short-Lived Climate Pollutant Reductions Act), it is expected that the next composting facility growth spurt will occur there. To achieve the goals of SB 1383, CalRecycle estimates that California needs approximately 50 to 100 new or expanded organics processing facilities to annually recycle an additional 20 million to 25 million tons of organic waste.
Having entered the composting industry in 1984, I have witnessed many industry growth spurts, and sadly, some huge facility failures. In the early 2000s when I tried to investigate why some large and expensive North American composting (and anaerobic digestion) facilities failed, I wanted to look past the obvious answers to get at the true root causes. Back then, I identified $400 million to $500 million in facility failures in just 20 failed (or failing) facilities. These cautionary tales can help avoid costly mistakes.
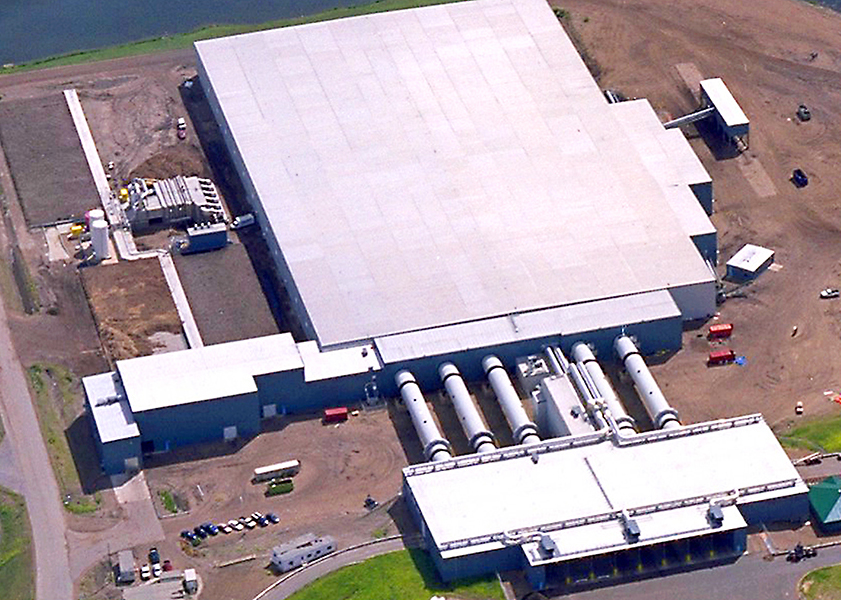
Facility design must take into consideration odor management and the quality and marketability of the finished product. Photos courtesy of Ron Alexander
What Goes Wrong
Some common mistakes found to contribute to facility failures are presented to assist in composting facility development.
Facility Design: Mistakes made in the overall design of composting facilities have been varied and numerous. In the past, major design failures (e.g., under designing aeration systems, poor use of conveyers with wet feedstocks, lack of curing space, etc.) have occurred when design engineers only possess a peripheral understanding of the composting process, as well as inexperience in the management of the specific types of organic by-products. Some mistakes have been caused by engineers and their clients trying to meet unrealistic economic parameters and bypassing a formal and appropriately completed facility design review. Working with an engineering firm that can illustrate it has designed well-operating composting facilities and understands the feedstock(s) to be managed, is paramount, as is their understanding of siting, environmental and regulatory issues. Of course, facility design must also take into consideration odor management and the quality and marketability of the finished product.
It often pays to get a second opinion on facility designs or technology selection. Large-scale facilities often cost tens of millions of dollars, thereby justifying an additional consultation phase.
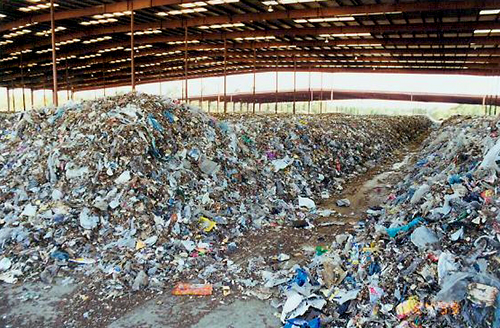
Misunderstanding the waste characteristics can greatly affect the operational costs and input capacity of a facility.
Technology Selection/Equipment: Consultants, their clients, and politicians have made mistakes by becoming enamored with specific types of composting technologies to the exclusion of others. At times, the favored systems have simply not worked as advertised (e.g., vertical biosolids composting vessels), while in other cases the systems were not appropriate for the location or feedstocks (e.g., continuous flow low solids digester for processing yard debris). It is vital to obtain assistance from consultants that possess proven experience in commercial-scale composting and technology selection before a preferred technology is chosen and an RFP is designed around it. The importance of working with a composting technology provider that can illustrate field success or working with an engineering firm that has designed successfully operating composting facilities cannot be understated.
Odor/Odor Control Systems: Probably the greatest cause of composting facility shutdowns in the U.S. — and perhaps the world — is odors. Although odors are always generated during the commercial composting process, the volume of the odorous air stream, as well as the types of odorous compounds generated, can greatly affect the severity of the potential odor problem offsite. Odors are often generated because of anaerobic conditions during the process caused by an under or poorly designed aeration system that provides oxygen to the process. Odor systems are often under designed, unable to provide the appropriate number of air exchanges per hour. Odor generation and management must be considered in the design phase, but proper operation of the facility is often the key to reducing odor generation and movement offsite.
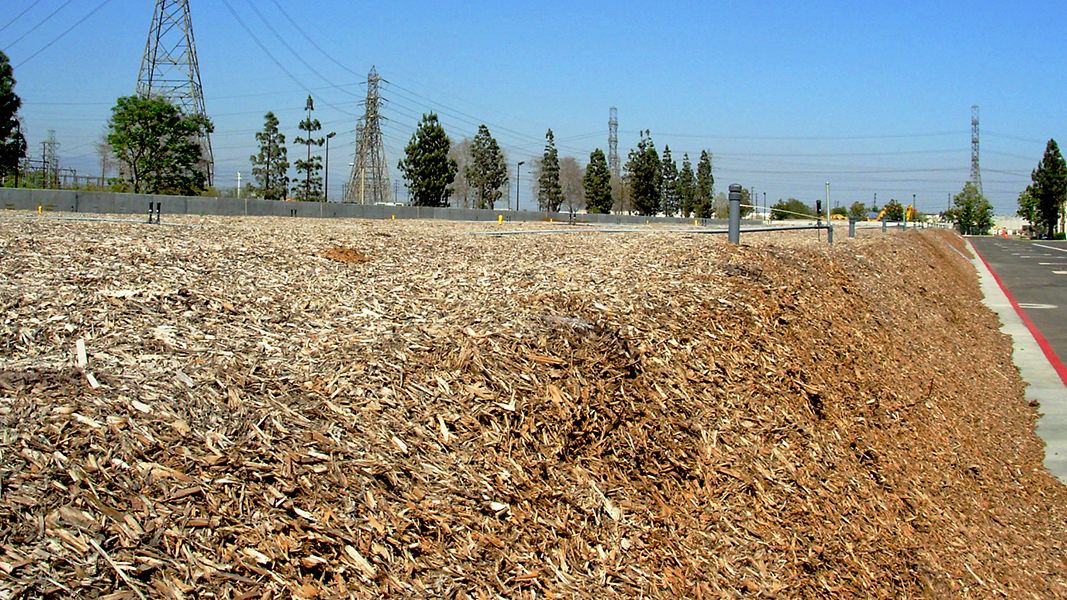
Proper operation of the facility, including maintenance of the biofilter, is often the key to reducing odor generation and movement offsite.
The science of odor control and odor monitoring is very complex, but the reaction of the general public is not. Facility developers may overlook including a budget line item for public outreach and investment in an odor response plan, e.g., a 24-hour odor complaint hotline, a staff member(s) who respond to and investigate odor complaints, and building in time to meet with community members who may be negatively impacted by odor incidents. Almost every composting facility will have odor incidents. The key is to set the public’s expectations that odors will happen and explain how facility operators will respond and be accountable.
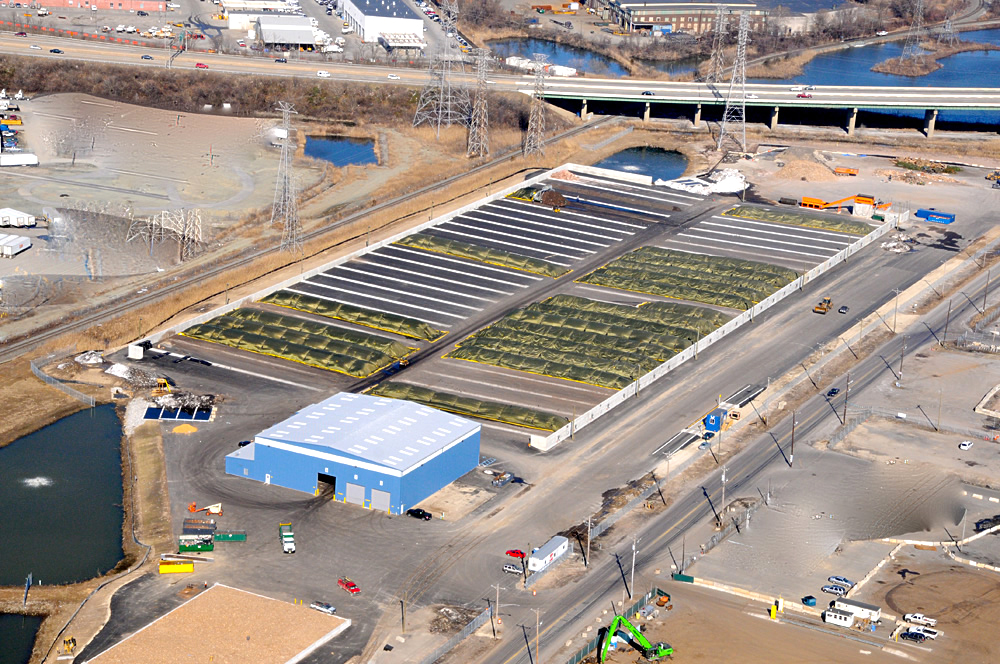
The location of a composting facility often goes hand in hand with nuisance odor issues.
Siting: The location of a composting facility often goes hand in hand with nuisance odor issues. Siting a facility too close to neighbors is a classic mistake of the composting industry. Even “in-vessel” systems are affected by siting issues related to odor generation. Further, truck movements (traffic) and other logistical issues pertaining to facility operation should never be disregarded. It is necessary to completely understand the environmental impacts of a composting facility’s site.
Misunderstanding Waste Characteristics and Properly Controlling Facility Inputs: Large-scale composting facilities, especially ones accepting food waste and mixed solid waste (MSW), should never be developed without completing proper waste characterization. Using national or regional characterization figures, which do not represent actual locally generated waste characteristics, has been a fatal flaw of several composting facilities. Misunderstanding the waste characteristics can greatly affect the operational costs and input capacity of a facility. This issue has been exacerbated by mandates to recycle postconsumer food waste, which can be highly contaminated. In the past, MSW composting facilities have been designed with a belief that food by-products and packaging would be the primary inputs, only to find that great volumes of nonrecyclable paper and cardboard were a majority of their feedstock. Other facilities have been designed having unrealistically viewed the purity of the expected incoming feedstocks.
Also, assumptions should not be made when it comes to the ability to capture incoming feedstocks. Steps must be completed to assure that at least a base volume of incoming feedstock is guaranteed before the facility is developed.
Politics: Several composting facilities were doomed from the start because of poor political decisions in the design phase. Examples exist where local politicians were invited on junkets to evaluate composting facilities without involving proper technical representation to assist them. Poor systems choices have also been made because powerful members of the selection committee have been enamored by specific composting systems, even though those systems were not best suited for their particular situation. Politics dealing with local residents and regulatory bodies have also caused the operation of many facilities to be altered or snuffed out completely. The lesson is that technical decisions need to be made by technical individuals who have practical experience.
Financial: Failures have also occurred because composting facilities were undercapitalized from the beginning and were unable to properly operate without compromising the long-term integrity of the program. Some facilities have been developed under “low bid” contracting conditions, and simply cannot perform as promised (additional infrastructure was required). Undercapitalized facilities have been forced to ramp up too quickly, trying to manage larger volumes of incoming waste than possible, in order to bring in required tip fee income. These situations have also caused odor problems because the proper investment was never made in an odor control system. Failures can occur because certain technology providers routinely underestimate the operational costs of their system, making the per ton management fees significantly lower than reality.
Product Quality/Marketing: Manufacturing a compost product that meets the quality requirements of the intended end users is the key to its marketability. However, aside from product quality issues, history has also shown that a lack of market development activity and underestimating the requirements necessary to develop a successful marketing program can cause marketing failures. This is important because poor or inconsistent marketing can impact storage requirements for the product.
One way to avoid such failures is to determine the realistic characteristics for the product you expect to produce, and then do market research to determine if markets exist for it. Understanding the needs of the marketplace, as well as the investment necessary to develop a successful marketing program, is often overlooked. Poor marketing leads to excessive inventory at the facility which may lead to odor generation, logistical issues, increased management costs, and public relations difficulties.
Summing Up The Realities, Key Steps
We have seen successes and failures, and what we have learned is that most of the latter can be avoided. One of the best ways to avoid failures in the development of large-scale composting facilities is simply to understand the realities of composting. Some of these realities are:
- Composting is both an engineering and biological process
- No composting facility is odor-free
- Most composting facilities generate some “reject” material (product that has to be landfilled). MSW composting facilities often have a 35% to 45% reject rate
- Operational challenges increase exponentially with facility size
- Developing markets for compost products takes time and investment (no composting facility should be developed without an understanding of where or how the product will be used).
Remember, if it sounds too good, it usually is. To minimize the possibility of facility failure, learn from past. Allow past experiences in composting facility design and operation to shape the design and operation of future facilities.
The keys to constructing and operating a successful composting facility are:
- Work with people/companies that understand the composting process
- Seek out experienced assistance to help you in the facility development process
- Select the proper composting technology and consultancy assistance
- Understanding the markets for your perspectives product(s)
- Allow for a proper planning and technical review process
- Start the planning/design process early (don’t let a short timeframe cause bad decision making)
- Never be a guinea pig — don’t be the first one to develop a composting facility based on a new or an unproven technology
Ron Alexander is president of R. Alexander Associates, Inc. (Apex, North Carolina, www.alexassoc.net), a company specializing in product and market development for organic recycled products. He is author and presenter of over 400 papers and presentations in composting and organics recycling. Ron is also the author of “The Practical Guide to Compost Marketing and Sales” and has over 35 years of experience in composting industry.