LHF Compost, Inc. in Peoria processes yard trimmings, food waste and manure. Recently, it erected a fabric building, and does active composting under roof.
Nora Goldstein
BioCycle April 2013, Vol. 54, No. 4, p. 26
As a former dairy farmer, Paul Rosenbohm has an appreciation for healthy soil, and first-hand experience with managing a waste stream. He and his wife, June, along with his brother and sister-in-law, owned a 150-head dairy farm in Peoria County, Illinois. As property surrounding the farm started being developed, the Rosenbohm brothers decided to start a business to compost the manure, in part to reduce odors. “My brother and I started the compost business together in 1998,” says Paul Rosenbohm. “In 2008, my brother took over the dairy farm and I took over the composting business.”
The enterprise, LHF Compost, Inc., was receiving manure from the dairy farm and yard trimmings from the City of Peoria. In 2000, the Peoria County Landfill attempted to become exempt from the state of Illinois’ yard waste disposal ban with the intention of developing a bioreactor landfill. “We lost the majority of Peoria’s yard trimmings at the time,” says Rosenbohm, “but we got it back several years ago by teaming up with one of the area haulers. While the city wanted to pursue the bioreactor, the county preferred our approach of composting and having a product that could be used.”
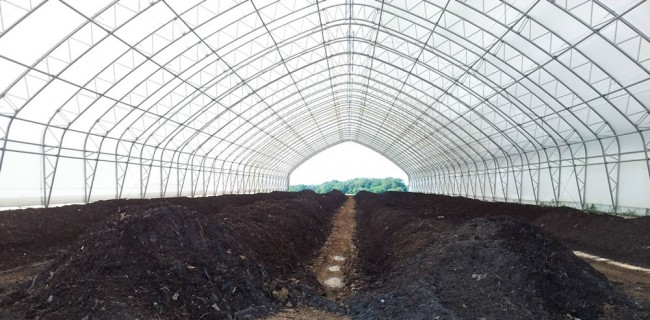
To better control the composting process, a ClearSpan fabric building was installed. The building accommodates four 450-foot long windrows.
To facilitate materials receiving and mixing, LHF Compost received a $125,000 grant from the Illinois Department of Commerce and Economic Opportunity (DECO) in 2010 to install a concrete pad and mixing pit. The pad receives the dry materials, including yard trimmings, wood and pallets. The mixing pit has walls on three sides and is sloped down six feet deep. “The wet materials are unloaded into that pit, and then we bring in leaves and other amendments to mix in with a front-end loader,” he says. Blended materials are put into windrows; manure is added at that point. LHF Compost has a 14-foot wide by 7-foot tall SCARAB to turn the windrows.
The facility is permitted to process 61,000 cubic yards/year, and is allowed to expand to 120,000 cy/year. “We haven’t arrived to the point where Illinois EPA will allow us to take that volume,” notes Rosenbohm. “In 2010, we received a penalty from the agency for leachate runoff from the pad to nearby surface water. We are getting a permit to put in a retention basin. In the meantime, we put up berms around the pads, and EPA is letting us apply captured runoff to our farm fields.”
Improving Process Control
Until last year, the blended materials were transported to an outside composting area where the windrows were constructed. To have more control over compost production — and to meet market demand for its trademarked brand, BetterEarth Premium Organic Compost™ — Rosenbohm investigated structure options to enclose the active composting portion of the operation. “If we have a lot of rain, the rows get saturated,” he explains. “We wanted to have the capability to compost year round without this issue.” LHF was able to obtain a grant from DECO in 2011 for a fabric structure. “We received a $249,500 grant, as another $500 would have put us in a totally different, and more complex grant category,” he adds.
LHF Compost selected a ClearSpan™ Hercules Truss Arch Building that is 100-feet wide, 465-feet long and 45-feet tall. The building accommodates four 14-feet by 7-feet by 450-feet windrows, and has adequate space to turn the piles and store screened compost if necessary. Rosenbohm and his crew chose to erect the building themselves, which went fairly smoothly. “ClearSpan had to send a crew to help us pull the last three tarps, but they didn’t charge us for the help,” he notes. “We opted for the Gable style structure because it goes more straight up like a regular building, giving us more vertical space. The pillars were installed 8-feet into the ground and 2-feet above, with a one-foot thick concrete wall between the pillars to keep the building from swaying. The concrete wall also protects the building from equipment like a loader hitting the sides. Windrows are built on a compacted dirt floor.”
The structure was completed in June 2012. The drought during the summer didn’t give LHF Compost much of an opportunity to take advantage of having the building, but the benefits were obvious during the winter months. “We were turning in January when the temperature was 0°F, and the center of the windrows was 150°F,” says Rosenbohm. “We also were able to screen product this winter, which we then put in a pile under the structure. We really like the strength of the metal frame and all of the natural light the cover lets in. Also, the ridge vent at the peak of the building enables the steam and vapor to go out.”
The facility is processing about 55,000 to 60,000 cy/year of feedstocks. Yard trimmings comprise the bulk of the material; food waste accounts for about 8,000 to 10,000 cy/year. It is permitted to receive compostable products, and accepts BPI-certified plates, cups, compostable food scrap bags, etc. LHF Compost purchased a Vermeer HG 6000 horizontal grinder, primarily to grind yard trimming and produce hardwood mulches. The food waste is not ground prior to composting. “It makes a mess going through the grinder, so we are just mixing it in and occasionally have to chase a few oranges or potatoes,” he notes.
The BetterEarth brand compost and blends are sold to landscapers, as well as bagged for retail sale. LHF Compost has a Screen USA star screen, and a Go Bagger from Rotochopper. “We’ve already been bagging for about two months,” says Rosenbohm. “We will probably make about 12,000 bags this year.” Landscape customers have included a new Target, Costco and Bass Pro shop. “They used our compost and mulch, and we made soil mixes to their specs,” he recalls. “We also produce bioswale mixes for storm water management. We haul in sand, and purchase topsoil, and then add in our compost. We use the SCARAB to blend these ingredients and it makes a really nice mix. We’ve also started marketing a garden mix, which our customers really like.”