Facility scheduled for completion in 2014 at Washington, D.C. treatment plant will utilize thermal hydrolysis and anaerobic digestion — and produce 11.8 MW of power.
Diane Greer
BioCycle October 2012, Vol. 53, No. 10, p. 42
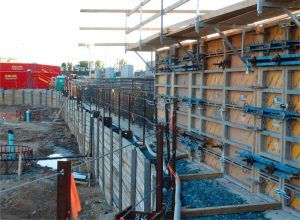
Construction of the thermal hydrolysis pretreatment system and digesters at the Blue Plains Advanced WWTP is expected to be completed in 2014.
The 153-acre plant, owned and operated by the District of Columbia Water and Sewer Authority (DC Water), is considered to be the world’s largest AWTP, serving over 2.2 million residents in Washington, DC and four adjacent counties in Virginia and Maryland. The facility, with an average flow rate of 370-million gallons/day (mgd), generates 1,200 wet tons/day of Class B biosolids that are recycled for use as soil amendments.
The anaerobic digestion system at Blue Plains, built in the 1930s to reduce biosolids volumes, was shut down about 10 years ago. “The digesters could not handle all our flow and were producing a very inconsistent product,” explains Chris Peot, DC Water’s manager of resource recovery. Currently, Class B biosolids are produced using a lime stabilization system. Class B biosolids are treated but still contain detectible levels of pathogens. There are buffer requirements and public access and crop harvesting restrictions.
Each day 60 to 70 truckloads of the material are transported and provided free primarily to farmers in Virginia and Maryland for application on agricultural land. Material is also sent to silviculture sites in Virginia, used for mine reclamation work and delivered to a composting facility. “We are successfully recycling the material,” Peot says. “We rarely have to send anything to a landfill but there are still risks involved with the Class B application programs so we wanted to put in the digesters to mitigate some of the risks.”
Thermal Hydrolysis
A few years ago Blue Plains decided to build a conventional egg-shaped digester facility, budgeting $300 million to $400 million for the project. When the bids and estimates were approaching $600 million, the Authority’s Board of Directors decided to investigate other technologies that stayed within the budget.
Thermal hydrolysis, pretreating the solids prior to digestion, looked very promising. Biosolids are treated with pressurized steam that destroys pathogens and improves digestion. In the first step, the solids are pressurized and cooked at very high temperatures (170°C) in a batch process for 30 minutes. The material is then fed to a flash tank operating at near atmospheric pressure. The drop in pressure causes the cells to burst, increasing the availability of food and proteins to the microbes in the digester. DC Water selected thermal hydrolysis equipment from Cambi, a technology provider based in Asker, Norway.
“The process provides several key advantages,” explains Perry Schafer, biosolids service manager for Brown and Caldwell, the firm hired to develop the biosolids program for the Blue Plains AWTP. “Besides improving digestion performance, the Cambi thermal hydrolysis process easily meets Class A biosolids requirements, greatly reduces sludge viscosity and digester sizing, and provides higher solids content dewatered cake. These factors have major economic advantages for a facility with the capacity needed at the Blue Plains plant.”
Utilizing the Cambi system and anaerobic digesters “makes financial sense,” Peot says. Digestion converts half of the organic material into methane, reducing the volume that needs to be recycled to 600 tons/day and lowering the costs of transporting the material for recycling. “It makes it easier to recycle and find a home for it,” he adds.
Initially Blue Plains will continue to land apply the Class A biosolids until it can build markets for the material through soil blending and other uses. “The options we have available to use the Class A product will allow us to keep some of the value within the District,” Peot says.
Digesting solids at higher concentrations will allow Blue Plains to save space and money. “Conventional digesters are fed at four to six percent solids,” Peot explains, noting that the thermally hydrolyzed sludge will be fed at 10 to 12 percent solids, halving the required digester volume. “Suddenly we could spend $30 million on the thermal hydrolysis pretreatment process and save $150 million in digester volume by building four tanks instead of eight. When you are building digesters the majority of the money goes into building the tanks.”
CHP System
Harvesting methane from the digester for use in the combined heat and power (CHP) system will produce 11.8 MW of power. About 2 MW are required to run the CHP system, netting the plant 10 MW. “The 10 MW of power is worth about $11 million/year,” Peot says. “Our draw from the grid is about 25 MW so it will cut our draw by more than a third and dramatically reduce our carbon footprint. In Washington, DC, power is generated from coal. By contrast this will be clean, green renewable energy.”
The Mercury 50 gas turbines employ a recuperative technology that uses turbine exhaust to preheat combustion air. “This is lowest achievable emission rate technology,” Peot explains. “We are in a sensitive area for air pollution. With this technology we are setting new standards for NOx emissions.”
Initially Blue Plains will only digest sludge but is considering Cambi pretreatment and codigesting of FOG (fats, oil and grease) and food waste. “We left room for receiving stations for restaurant grease, food waste and even outside sludge from other WWTPs that do not have the capital funds to build digesters,” Peot says. “We are not going to do it right away, but are leaving room so that we can expand operations, if we choose to do so, once we are comfortable with operating the system. “
He expects that at some time in the future the cumulative savings related to the project will exceed the costs. “Right now we think that is about 13 years out,” he says. “I think it will be quicker.” The estimate assumes that Blue Plains will continue to land apply the material. “We assume a $6.50/ton savings for applying the Class A biosolids versus the Class B but that does not account for the ability to create soil blends and sell it,” Peot continues. “I honestly think we will be able to make a product out of it and either sell it ourselves or work in tandem with soil blenders and share the savings and revenues.”
The goal is to eventually achieve a zero cost biosolids program. “Right now we spend about $18 million a year to ship this incredibly valuable resource to farmers and give it away free,” he says. “There is high demand for the material and there is going to be even more demand with our future class A product. We have a lot of different things that we can do, so eventually I think we are going to be able to, at the very least, avoid some costs if not make some money on it.”
Diane Greer is a Contributing Editor to BioCycle.