China’s demand for softwood reached a fever pitch in early 2011, but it refused to buy logs with bark intact, leading to a huge surplus.
Nate Seltenrich
BioCycle November 2012, Vol. 53, No. 11, p. 27
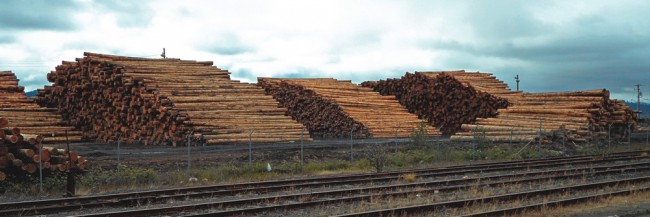
Logs stripped of their bark are stockpiled at an ocean terminal in Oregon. Photo by Gordon Culbertson, Forest2Market
The boom was great news for logging and sawmilling operations in the region, and likely helped keep dozens of sawmills open during an otherwise challenging time for the industry due to an ebb in new homebuilding in the U.S. But there was another, more unexpected outcome of the surge: a massive bark surplus.
The surplus was caused by China’s concern over importing bark-dwelling pests like the mountain pine beetle, currently devastating forests throughout the West. Like European countries that import biomass from the southeastern United States, where other pests are common, China refuses to buy logs with bark intact. “It’s an issue with bringing in insects that don’t belong in the country,” explains Hakan Ekstrom, president of Wood Resources International, which tracks biomass markets throughout the world. “They want to make sure the country isn’t flooded with North American insects.” Instead, all logs must be debarked before export.
It’s worth noting that the risk of spreading pests through bark removed from the logs is small, according to Dave Atkins of the U.S. Forest Service. When logs are mechanically debarked, most larvae that happen to be living in the bark will be killed by sheer force. “The ones that don’t get squished are going to be exposed to drying because of not being hidden between the bark and the wood,” Atkins explains. “The potential for something to complete its life cycle and then expand out is really, really minimal.”
Managing The Bark
The huge volumes of logs and lumber leaving Northwest ports last year meant a proportional quantity of bark staying behind (bark represents about 10 to 12 percent of a log by volume). This occurred at export ports throughout the region, including southern Washington’s Port of Longview, where many regional log exports are funneled, as well as at Coos Bay, Tacoma, Port Angeles, Everett and other, smaller ports, Hekstrom says.
At first, no one knew quite what to do with the bark. But eventually, most was absorbed into the market. Understanding where it went may provide a lesson for the future, should demand for logs and lumber from China recover in 2013 and beyond — as many industry analysts expect it will.
There are three primary uses for bark, and each played a part in absorbing the Northwest surplus: decorative bark and mulch, fuel and compost blends. Although it’s impossible to follow every load of bark from every port — and no one seems to have tracked the material with any detail — compost outlets probably played the smallest role. Companies can generally get more value out of the bark by processing and bagging it for sale as decorative mulch or by selling it as fuel.
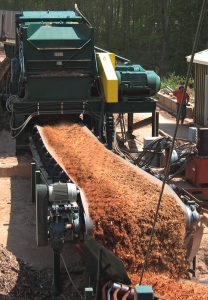
Softwood bark on the West Coast sells as a premium product. After processing, it is typically bagged for market.
Cedar Grove Composting in Seattle includes one-half compost and one-half locally sourced fine bark in its Northwest Garden Mulch. It also uses bark in smaller concentrations in its basic potting soil. Oren Posner of Lane Forest Products in Eugene suggests that the extra bark on hand in the Northwest last year was reason alone to funnel some of it into compost products. “They had so much material they just had to get rid of it,” he says.
For many processors, selling bark as fuel has traditionally been the most profitable option. However, that’s changed in recent years as declining energy demand and a glut of natural gas have exerted downward pressure on the price of hog fuel, which is composed of low-grade bark, wood shavings and other biomass materials. Declining fuel markets compounded the challenge of finding a home for all the new bark.
The most likely destination for the bulk of the bark is what’s alternately referred to as beauty bark, landscape bark and mulch — bark in its best use, serving both aesthetic and practical purposes and earning the highest dollar. “Softwood bark on the West Coast sells as a premium product,” says Mark Lyman, president of West Salem Machinery in Salem, Oregon. “It has a lot of value.” West Salem sells grinding and screening machines as well as complete plug-and-play systems for producing bark products in the desired size and shape. Oscillating and trommel screens are used in conjunction with horizontal and vertical feed grinders to produce bark pieces sized for bark rock, decorative bark and finer mulch and ground cover.
After processing, the bark is typically bagged and sold to markets throughout the West. Cedar, spruce, hemlock and Douglas fir all produce bark suitable for landscaping use, with cedar typically being the most expensive. According to Tim Gammell of Wood Resources International, bark out of the Northwest is primarily separated into premium grades for local use or shipment to California, Phoenix and Las Vegas. But with the slow pace of new home construction in those regions last year, demand for landscape bark was down, too.
Bark markets in the Pacific Northwest are likely to remain tied to construction and development in China for the foreseeable future. “I’m not used to having what happens in China affect what happens in Eugene,” notes Posner, “but I think we all better get used to it now.”
Nate Seltenrich is a writer based in Oakland, California.