Top: The Delaware County mixed waste and biosolids composting plant is totally enclosed in a 3-acre structure. A rotary drum bioreactor (inset) is the first step in processing the mixed MSW. Photos courtesy of Delaware County Department of Public Works.
Nora Goldstein
Delaware County, New York is in the watershed of New York City’s drinking water supply. Being in the watershed limited the County’s Department of Public Works’ (DPW) options for solid waste and biosolids management — especially in terms of expanding and/or siting a new landfill — ultimately leading the county to opt for pursuing a mixed municipal solid waste (MSW) and biosolids composting facility. In 1996, an RFP was issued for the composting facility. Conporec/S&W (Stearns & Wheler) Services, Inc. was selected to build the roughly $20 million plant. Operations got underway in 2006.
The county contributed the land, along with millions of dollars of construction work on the facility, including concrete construction, some electrical wiring, and installation of all processing equipment except the Conporec rotary drum bioreactor. Funding for the facility included a $2 million recycling grant from the New York State (NYS) Department of Environmental Conservation, a $11.5 million bond from the NYS Environmental Facilities Corporation, and $7.5 million from county solid waste funds.
Recyclable materials are collected curbside and taken to a materials recovery facility (MRF) located on the same site as the composting plant. Haulers bringing in solid waste generated in the county are not charged a tipping fee for residential waste collected in the county. The Delaware County DPW’s annual funding comes from receiving one percent of the county’s sales tax. The funds are used to cover capital and equipment costs and enable the county not to charge a tipping fee for residential and commercial in-county waste. There are tip fees for some industrial and construction wastes.
The 3-acre structure contains the tipping floor, bioreactor, primary screening trommel, secondary sorting line, the maturation area with the Siemens/IPS (now BDP Industries) Composting System, final screening system, aerated final product storage area, recycling and residue roll-off containers, and a compost load-out truck bay. The facility was designed to process 35,000 tons/year (tpy) of MSW, plus 6,700 tpy of biosolids, for an average of 120 tons/day (tpd). On the tip floor of the composting facility, a 5-ton capacity grapple on an overhead crane, controlled by an operator in an elevated booth, is used to pick out large bulky items, which are dropped into a roll-off container inside the building.
Original Facility Design And Process Flow
Waste Receiving
A 2006 BioCycle article, “Composting Mixed MSW And Biosolids To Extend Landfill Life,” was published when the Delaware County composting facility opened. The article noted that biosolids were handled in two ways on the tip floor. For biosolids less than 10% solids content, the liquid was discharged into a 30,000-gallon holding tank and then metered into the bioreactor as a moisture and nitrogen source. Leachate from the biofilter and other locations in the facility also flowed to that tank. For higher solids content biosolids, typically 18%, trucks would dump into a hopper below the tipping floor that fed an “Eleveayor” — two conveyor belts that compressed biosolids and lifted it up to a tripping conveyor that fed the biosolids directly into the bays of the maturation area on the other side of the tipping building wall.
The waste receiving area is a combination tip floor and waste pit with sufficient height and length for large roll-off trucks and dump trailers to tip their loads into the waste pit while the overhead doors remain closed. The pit has capacity to store about one week’s worth of MSW, or 500 tons. The operator in the control booth loads MSW into a hopper that feeds a conveyor to the bioreactor at the rate of about 10 to 12 tons/hour for approximately eight to 10 hours/day. A bucket loader is used as a backup to the grapple. If the plant is down for more than a week, MSW and sludge can be diverted to the adjacent landfill.
Rotary Drum
The 157-foot long by 14-foot diameter rotary drum bioreactor is constructed from rolled steel. Based on its experience at a facility in Quebec, Conporec built the shell out of thicker steel — three-quarters to 1.5 inches — to better protect against cracks in the shell and end walls of the bioreactor. The drum rotates seven days/week, 24 hours/ day, and is powered by a 200 HP variable speed electric motor. The hydraulic ram feeding MSW into the drum is constructed on a downward slope to take advantage of gravity to push MSW into the drum. Conporec also added temperature probes at the front and rear of the reactor, and two blowers instead of one to move air through the vessel, keeping an aerobic environment. The purpose is to maintain the pH as close to neutral as possible to minimize corrosion of the shell. If pH drops to 4.5, acidity attacks the shell.
The drum rotates at a maximum of one revolution per minute and is driven by a ring gear that automatically is lubricated with a spray system. The tire supporting the drum is not welded to the drum, but is free to move, or “float” on the shell; it also has an automatic lubrication system. Since the vessel is inside a building, there is no foam insulation on the drum, facilitating inspection of the shell for cracks or other signs of fatigue. Retention time in the bioreactor is three days. The drum is discharged simultaneously with the loading process, over an 8-to-10-hour period. A screen with six-inch diameter holes is attached to the discharge end of the drum to distribute the discharged material more evenly onto a heavy duty, mining grade discharge conveyor, which feeds a covered inclined conveyor going to a covered primary trommel screen with one-and-one-eighth-inch holes.
Compost Maturation
The compost maturation area is housed in a frameless, pre-engineered steel structure lined with stainless steel panels. The purpose is to minimize corrosion of the building, which is exposed to high concentrations of corrosive gases and condensation coming off the positively aerated compost bays. Raw compost from the primary trommel is conveyed to the maturation area with a conveyor system and tripper car to feed 14 aerated, agitated BDP bays, each 235-feet long by 8-feet high by 10-feet wide.
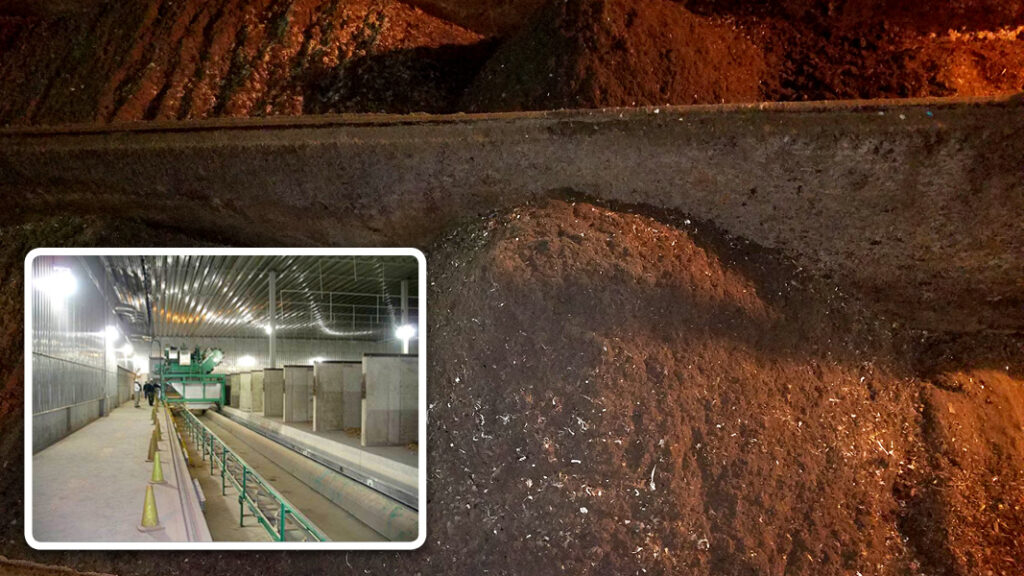
Raw compost from the rotary drum is loaded into aerated bays turned with a BDP Industries agitator; retention time in the bays is is 56 to 60 days.
Delaware County operates the bays on a 56- to 60-day detention time (21 to 28 days retention is more typical at plants using this technology). The purpose is to achieve a fully mature, finished compost coming out of the bays. The agitated bay system has three aeration zones that allow for better process control with respect to mixing and water addition — effectively curing the MSW compost with a relatively high carbon content. As designed, the system has capacity to process about 200 cubic yards/day, moving material down the bays about 13-feet for every pass of the automated agitators; each pass takes from 45 to 55 minutes to traverse the 235-foot distance to the end of the bay where material is discharged. The agitator is then automatically transferred to another bay.
Odor Control
There are many air changes per hour throughout the plant (as many as eight in the maturation building). Exhaust air from the maturation room, which includes air from other portions of the facility, is pushed to a 0.5-acre biofilter located outside the building. The biofilter is designed to process 78,000 cubic feet/minute of air and is constructed in two cells that can be independently operated.
Product Finishing, Compost Markets
The secondary screening system is in the same portion of the building as the primary screening system. The original design included a high-speed inclined conveyor with a leveling bar to spread out the material to separate pieces of glass, bottle caps, rock, and other heavier items that would roll backwards down the conveyor (including some chunks of compost). Compost that stayed on the conveyor passed through a drum magnet to pull off metal fragments, then went through a trommel with a one-quarter inch screen size, followed by a roller crusher to pulverize remaining glass fragments.
Most of that original equipment is no longer in use. What remains is a trommel with one-quarter-inch screen holes. For this screen to be effective the material must be rather dry. Because the compost is drier, moisture is added after screening to provide a better product and suppress any dust. WeCare Denali (originally named WeCare) has been marketing the compost since the facility opened. A significant portion of the compost is sold (as part of a blend) to contractors for projects with the New York State Department of Transportation (NYS DOT) for use in its roadway, slope stabilization and pollinator projects. The NYS DOT market varies by region and depends on the regional office’s understanding of compost use benefits and what should be specified for NYS DOT projects. Another potential market is mineland reclamation, especially at former coal mines in the neighboring state of Pennsylvania.
Current Operations
Little has changed in the overall process flow at the Delaware County mixed MSW and biosolids composting facility since it opened. The amount of incoming material fluctuates between about 18,000 and 20,000 tpy of MSW. Biosolids tonnages have decreased over the years; in 2022, the plant received about 2,000 wet tons.
Rotary Drum Maintenance
Delaware County is still using the original Conporec rotary drum, although its various parts have been replaced and cracks have had to be repaired. It is likely going to have to be replaced in the near future, notes the DPW. Cracks going down the sides of the drum are less problematic than those going across the drum in terms of necessary repairs. Cracks form due to stresses on the drum and have been apparent for a very long time. The drum sits on two sets of trunnions so it will feel stress as the drum ever so slightly bellies in the middle and sags on the ends. Stress creates weak points from this compression and expansion as the drum turns. These cracks have been addressed in several ways — from plug welding on plates to stitching on steel sutures. Wear bars (angle irons) are key to the drum’s longevity and involve a fair amount of welding inside the drum when it is time to replace them. Delaware County also installed thick blocks of steel with blunt edges inside the drum to break open bags and prevent “monsters” from forming. These wear bar “knives” help material from getting tangled in each other and forming balls and 90-foot-long strands of difficult-to-remove contamination. The drum’s one rotation a minute creates a gentle oscillation that keeps materials intact while degrading organics.
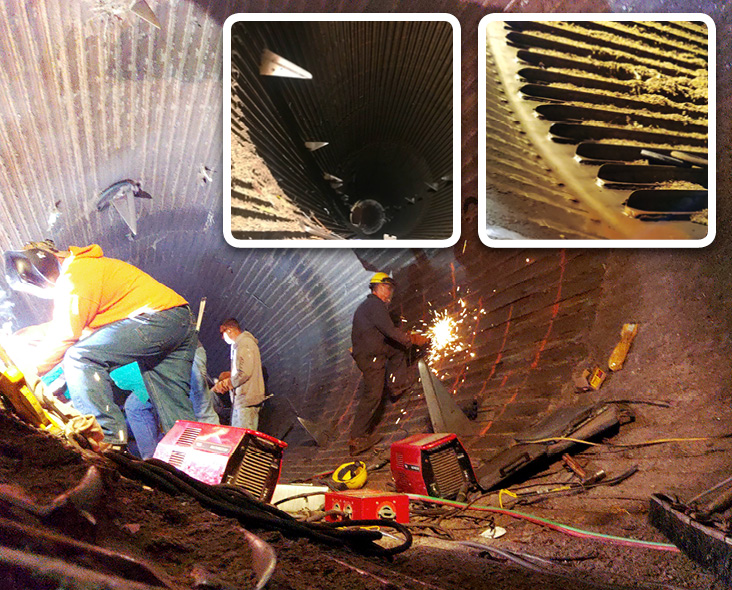
Wear bars (inset on right) are key to the drum’s longevity and involve a fair amount of welding inside the drum when it is time to replace them. Delaware County also installed thick blocks of steel with blunt edges (inset on left) inside the drum to break open bags and prevent material from getting tangled in each other and forming balls.
Additional air handling has been added at the inlet and outlet of the rotary drum. This helps limit corrosion on the structure and process equipment and reduces the potential of elevated concentrations of any harmful gasses. Stainless is the natural choice for all air handling equipment.
Biosolids Receiving
The biosolids receiving pit is 15- to 20-feet deep. Incoming biosolids vary in moisture content — from 12% to 15% on a “bad day” to upwards of 30% on other days. The original Eleveayor in the biosolids receiving pit, which could only handle drier biosolids, was replaced with a progressive cavity pump with augers. Unlike the Eleveayor, the cavity pump works best when the moisture content is high, i.e., it can only handle wet material. Across the county, the wastewater treatment plants operate differently, e.g., some use drying beds to remove moisture, and other have dewatering equipment that removes less moisture.
To resolve the situation, the facility has built an organics receiving area in a corner of the room where curing takes place after compost screening. Manually loading the bays will allow the composting facility to serve all treatment plants (with different capabilities) more consistently. The operator lays down a thin bed of wood chips and the biosolids are unloaded on top. A skid steer mixes the material and loads it into the receiving end of an agitated bay. Biosolids with high moisture content will be added via the cavity pump, which recently was replaced. The new biosolids receiving area and manually loading into the bays enables the county to handle all sorts of biosolids and organics by bypassing the drum and any pumps.
Facility Structure
Use of stainless steel in the structure housing the maturation bays has proven to be a good investment. When the surfaces are pressure washed, they look “good as new.” Other parts of the building, including the receiving area and the inlet to the drum, were built with galvanized steel, which has corroded. Delaware County recently replaced the walls and ceilings in those areas. For non-structural needs the county has found HDPE flat stock is more resilient than metal.
Total material that goes to landfill in the county can be as little as 0.5 cubic yards/person/year. Residuals from composting account for about half of that amount (these are primarily plastics); the other half is industrial waste material not suitable for composting. The county has been exploring alternative options for the residual plastic from primary sorting in the composting facility, including chemical recycling. The overall recycling rate in the county is about 45 to 50 percent and could increase if a recycling technology becomes available to recycle film plastics and packaging material.
When asked why Delaware County’s approach to solid waste composting has withstood the test of time, Tyson Robb, solid waste coordinator, noted the biggest strength is that composting is part of a system that includes a MRF, transfer stations, and an MSW landfill. “Any one of those components on its own would not be as strong,” said Robb. “The sum of the parts is greater than the whole. The ability to flex between systems, especially when the composting plant gets shut down for maintenance, is what makes our approach to solid waste management resilient. And the financial benefit to the county to compost is that the landfill is filling less and there is a reduced need to transfer solid waste, which is costly.”