Huckabay Ridge was shuttered in 2010, but after the facility was purchased at a public auction, operations restarted in 2011.
Diane Greer
BioCycle February 2012, Vol. 53, No. 2, p. 49
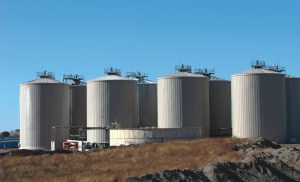
Huckabay Ridge is comprised of eight, 916,000-gallon above ground digester tanks operating at thermophilic temperatures. Photo courtesy of Element Markets
But the plant fell victim to EPC’s ambitious plans, which saddled the company with an unsustainable debt load. Meanwhile falling natural gas prices and the demise of national climate legislation negatively impacted revenue expectations. Unable to generate sufficient cash flow to meet bondholder obligations or find outside financing to bridge the gap, EPC filed for Chapter 7 bankruptcy in July 2010. Huckabay went into receivership.
The plant received a new lease on life in November 2010 when Houston-based Element Markets (EM), through its wholly owned subsidiary EM Biogas LLC, purchased Huckabay at a public auction, paying $3.3 million for the facility that cost $18.4 million to build. EM is a privately held producer and marketer of renewable natural gas and environmental commodities. The purchase of Huckabay Ridge fits the company’s development strategy, which is focused on the biogas market. The firm is also developing and constructing several landfill gas projects that will upgrade the biogas for injection into natural gas pipelines.
EM’s goal is to turn Huckabay into a technological and commercial success. To that end the company is investing approximately $12 million in plant improvements and upgrades. “The plant had been offline for awhile when we purchased Huckabay,” explains Angela Schwarz, EM president and CEO.“We knew from our initial due diligence that the gas pad had been pieced together with refurbished equipment — some components appeared to be over 30 years old and in tired condition even though the facility was constructed less than 5 years earlier — and would need to be replaced to ensure sustainable and profitable operations.”
Huckabay Ridge is comprised of eight, 916,000-gallon above ground digester tanks operating at thermophilic temperatures. At capacity the complete mix system is designed to digest manure from about 10,000 dairy cows, along with organic substrates, to produce 2 million-cubic feet/day of renewable natural gas (RNG) with an energy content of 650,000 MMBtus/year. Manure received at Huckabay arrives via trucks.
Biogas is purified and upgraded to pipeline quality RNG using amine processes. A low pressure amine system removes most of the carbon dioxide (CO2) and hydrogen sulfide (H2S) in the biogas. It is then compressed to pipeline pressures and fed to a high pressure amine system that removes the remaining CO2 and H2S. Glycol treatment is used to dry that gas prior to pipeline injection. The RNG is sold to PG&E (Pacific Gas & Electric) in California under a 10-year power purchase agreement, signed by Microgy (an EPC subsidiary) in October 2006.
Facility Improvements
EM’s first order of business after the purchase was to get the plant back online. The digesters were reseeded in late January 2011 and started producing biogas about a month later. Initial improvements focused on health, safety and operating procedures along with reenergizing the team.“The operating manager and his team had the resident knowledge on the plant,” Schwarz says.“Reconstituting their enthusiasm for the plant and accessing their historical knowledge has really been key to us for operating the plant.”
Installation of a natural gas pipeline insured a consistent gas supply to the boiler heating the digesters. Previously the plant relied on biogas to fuel the boilers. This arrangement proved problematic when the digesters were down or not producing sufficient quantities of gas.
An agitation system was added to the preslurry pit to mix the manure before it is fed to the digesters.“We are looking at the possibility of mixing the substrate and the manure prior to introducing the material to the digester,” says Alan Jackson, EM’s vice president of engineering services. Currently incoming organic substrates, consisting of fats, oils and grease (FOG) along with glycerin from biodiesel operations, are delivered to a substrate tank that is heated and agitated. These materials are then fed separately into the digesters.
Newly added access ports, located at the mid-point of each digester, allow plant operators to take daily samples to test for volatile solids levels, alkalinity, pH and COD. Based on the analysis, adjustments are made to the proportion of manure to substrate fed to the digesters. Operation and maintenance work included cleaning pipes and replacing a number of pumps at the facility. A review of the plant’s instrumentation is planned to determine upgrade requirements.
Running the plant in Stephenville’s hot, dusty environment requires a lot of operation and maintenance work.“We are in the process of analyzing every piece of equipment and putting an O & M program in place,” Jackson explains. Tasks include identifying a list of critical spare parts and possible process improvements to provide system redundancy.
To insure feedstock quality EM built an onsite laboratory staffed with a full time technician. Every incoming truckload of substrate is tested for pH, moisture and COD levels, Jackson explains. Manure is tested for TKN (Total Kjeldahl Nitrogen) and moisture content.“If it doesn’t meet the criteria coming in we reject the loads.”
Unfortunately the manure testing program was not in place in early July when the plant experienced a decrease in digester alkalinity that caused biomethane production to drop below the level required to run the gas compression process essential to the gas purification and pipeline injection system. “Analysis of the ‘wet’ manure received from freestall dairies indicated very low TKN values,” Jackson explains.“Discussion with these dairies revealed significant changes in cattle feed formulations due to the Texas drought. We believe these changes resulted in impacts to the manure quality and our ability to manage digester alkalinity.”
The plant discontinued accepting deliveries of wet manure and relied solely on dry lot manure for the rest of the summer. The dry lot manure, while satisfying the facility’s TKN requirements, had high levels of inorganic content, such as sand, and required more fresh water to hydrate the manure prior to feeding it to the digesters. By late August digester alkalinity levels were back to normal and the facility resumed pipeline injection.
Currently Huckabay is feeding 120,000 to 150,000 gallons of manure and 30,000 gallons of substrate (50 percent glycerin and 50 percent FOG) to the digesters daily to produce about 2,000-scfm of biogas. Manure is primarily received from one freestall and one dry lot dairy.“As the conditions have changed and the freestall dairy has gotten back to its original animal feed we are bringing in more of that wet manure,” Jackson explains. As more experience is gained with the plant, Jackson believes biomethane production could ultimately surpass the facility’s original design capacity of 2,400-scfm.
Digester capacity is one factor that may limit increases in biogas production. Prior to restarting the plant, EM chose not to clean out the tanks.“We recognize that there is probably a significant portion of the digesters that have inorganic material settled on the bottom,” Jackson explains, noting EM wanted to focus first on the biogas handling equipment. To deal with the reduced capacity, EM decreased the amount of substrate fed to the digester by one-third to one-half compared to historic levels.
Increased retention time helps offset the reduced volume. “We are processing less material in those digesters now then in the past yet we are producing significantly more gas,” Jackson says.“We are on the analysis curve, trying to figure out the sweet spot.I’m still hesitant to push too hard too fast but remain optimistic that the plant will be able to consistently exceed its design capacity.”
Future capital projects will look at technologies available to clean out the digesters.Getting back the lost capacity will enable some increase in the daily feed rates. Also under consideration are solid separation systems to significantly reduce the amount of inorganic material in the manure prior to feeding it to the digesters.
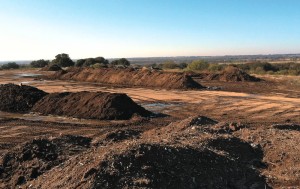
Digested solids separated from liquid effluent are being stored on site. Future plans include composting the solids to create an additional revenue stream.
Liquids are injected into nearby farmland. EM is considering building a liquids storage lagoon.“Once we get the liquid-solids separation running well we will have other options for the liquids including recycling some back to the digester,” Jackson explains.“It is a process of optimizing at this point and we are still on a learning curve.”
Commercial Success
Currently the majority of Huckabay’s earnings are garnered from biogas production with some revenue from substrate tipping fees.“Our 2012 plan is to create multiple revenue streams for the facility,” Schwarz says.“While the primary source of revenue will remain gas sales, we anticipate considerable revenue from our composting activities, along with tipping and water usage fees.”
Schwarz does not see the existing PG&E contract as a liability nor does she believe that alternative uses for the gas, such as electricity generation, make sense at this time.“Power prices in Texas remain low as does the underlying natural gas price,” she explains. “Bringing the gas to premium markets is the only economic option for this plant today.”
From a project economics standpoint the RECs (renewable energy certificates) and other environmental attributes of the RNG are an important part of the value proposition. California’s new cap and trade program, mandated as part of the state’s larger plan to reduce greenhouse gas (GHG) emissions under the Global Warming Solutions Act of 2006 (AB 32), represents one potential source of additional revenues for Huckabay. EM will leverage its expertise in the trading and marketing of environmental commodities to participate in the California credit market via its sale of RNG to PG&E. Starting in 2013, large industrial sources and electricity utilities in California will be required to reduce their GHG emissions or purchase emission allowances from other entities.
Production of RNG from biogas is considered to have negative net emissions and thus enables its users to reduce GHG emissions.(Biogas is seen as GHG negative since it not only displaces natural gas making it a biomass derived fuel and therefore carbon neutral, but it also generates GHG reductions through the avoidance and destruction of methane emissions, which is a CO2 reduction below the neutral baseline set by the displacement of natural gas.) The added value of trading emission allowances by RNG producers is yet to be determined. As an indicator, Schwarz is seeing premarket pricing of emission allowances between $10 and $17/metric ton.
Diane Greer is a Contributing Editor to BioCycle.