An anaerobic digester at Michigan State University processes a variety of source separated food waste, FOG and dairy manure. The facility is helping to meet the campus’ renewable energy target.
Craig Coker
BioCycle February 2016
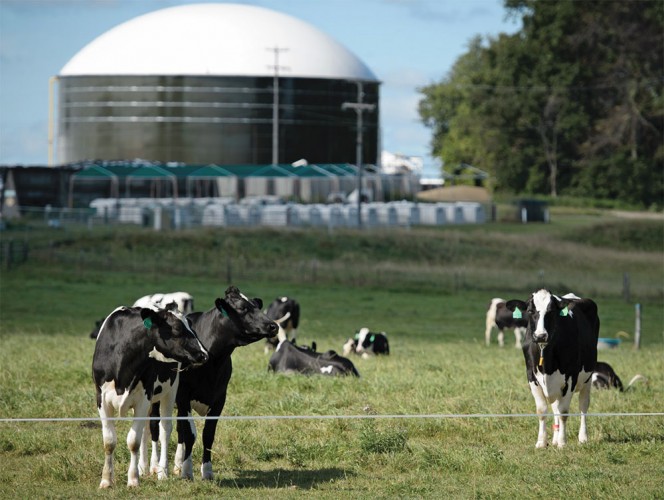
Digestate is dewatered with a screw press. Liquid ef uent is used on the University’s agricultural land. Solids are composted on- campus with landscape trimmings.
Michigan State University (MSU) is the seventh largest university in the United States in terms of enrollment. Approximately 17,000 students live on the East Lansing campus. In 2010, recognizing that MSU had the opportunity to set a standard in sustainable energy usage, the Energy Transition Steering Committee — a 24-member group of students, faculty and staff — was formed. The committee was charged with developing a plan to help MSU reliably meet its future energy needs while keeping a close eye on costs and environmental impacts.
The resulting MSU Energy Transition Plan was adopted by the MSU Board of Trustees in April 2012. It features three primary goals that will move the university toward 100 percent renewable energy sources and reduced greenhouse gas emissions: Improve the physical environment, invest in sustainable energy research and development, and become an educational leader in sustainable energy. In addition to an anaerobic digestion (AD) project, MSU has almost finished converting its power plant from coal to biomass and has started work on a 20 megawatt (MW) solar array. Future projects may include a wind farm and algae growth biomass production facility to help sequester carbon dioxide.
South Campus AD Facility
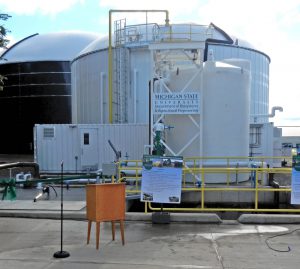
The feedstock receiving area (foreground) includes an open- air receiving pit for “low energy” feedstocks like manures, and a covered receiving area for “high energy” feedstocks like food scraps and FOG.
The South Campus Anaerobic Digester was the first project to be implemented to support the Energy Transition Plan. Beginning in mid-2012, planning focused on developing a system that could handle campus cafeteria food scraps, manure from the MSU Dairy and Teaching Research Center, fruit and vegetable wastes from a nearby food distribution center, and fats, oils and greases (FOG) from area restaurants. Campus Culinary Services provides over 150,000 meals per week through nine dining halls and 23 other food service establishments. University food scraps generation is estimated at 900 to 1,000 tons/year (tpy); annual dairy manure production is estimated at 22,000 tpy. Prior to development of the AD project, food scraps were macerated and flushed down the sewer to the University’s treatment plant.
The AD project was preferred over a composting alternative as it could contribute to both the MSU Energy Transition Plan and the MSU Campus Sustainability initiative, which has a large recycling component. The facility is located next to the Dairy Center. The AD system was designed to process 16,650 tpy, generating 3.0 million kilowatt-hours (kWh)/year of electricity to be used on-campus “behind the meter.” Heat captured from the Combined Heat-and-Power (CHP) generator is used to heat the digester, the support building and the solids separator during cold weather, and radiated to atmosphere in warm weather. A ribbon cutting was held on August 13, 2013. Total cost of the project was approximately $5.1 million.
The digester complex was designed by MSU and the feedstock mixer-digester-CHP engine system was sourced from Anaergia. It is a continuously-stirred tank reactor (or complete mix system) with 400,000 gallons of capacity (52-feet diameter, 26-feet high), a hydraulic residence time of 20 to 25 days, a solids residence time of 20 to 25 days, and an operating temperature of 100°F. Digestate is dewatered with a screw press. The liquid effluent is used on MSU’s agricultural land. Dewatered solids are composted on-campus with landscape trimmings in a windrow system.
The feedstock receiving area consists of two separate systems — an open-air receiving pit for “low-energy” feedstocks like manures, and a covered receiving area for “high-energy” feedstocks like food scraps and FOG. The food scraps receiving area is a 20,000 gallon concrete tank heated to 80° to 90°F; compartment air is vented to a biofilter. Residence time in the food scraps receiving area is about 24 hours.
The original feedstock mix plan was for 43 percent dairy manure, 24 percent waste fruits and vegetables, 30 percent FOG, and 3 percent cafeteria food scraps. However, the actual feedstock distribution in 2014 was significantly different with 67 percent dairy manure (16,000 tons), 12 percent waste fruits and vegetables (2,900 tons), 19 percent FOG (4,400 tons, but at higher moisture content), and 2 percent cafeteria food scraps (430 tons). This was due to constraints in securing adequate amounts of the previously committed off-site FOG due to contractual sourcing issues. Thus the operator had to bring in manures from other campus sources, primarily the Beef Cattle Teaching and Research Center, to try to maintain biogas output.
In 2015, the manure contribution was reduced to 43 percent by supplementing off-campus sourced feedstocks with a milk processing waste (which, in 2015, accounted for 25% of all feedstocks). Biogas production in 2014 averaged 1,196 cubic-feet-per-minute (cfm) per ton of incoming feedstock, with a methane content of 63.4 percent. In 2015, as feedstock quantities and qualities stabilized, gas production improved to 1,953 ft3/ton with a methane content of 61.3 percent. Electricity production in 2014 averaged 199 kWh; in 2015 it was 260 kWh.
Early Challenges
MSU had run methane generation potential tests on the various feedstocks it planned to feed the digester, which were used in the process design. The original FOG sample tested had a solids content of 20 percent, however what was actually delivered had a solids content of only 2 to 5 percent, and was only 25 to 30 percent of the 5,000 tpy they anticipated. This had a large impact on volatile solids mass balance and is one reason why biogas production was so variable in 2014.
In addition to unanticipated changes in the quality characteristics of the FOG, operational challenges in the first year included large particle sizes of the incoming fruits and vegetables, contamination in all the feedstocks (stones/grit, plastics, gloves, salad tongs, grill grates) and dealing with partially-frozen feedstocks. “It gets quite cold up here in the winter, and AD systems don’t handle frozen feedstocks well,” notes Dana Kirk, Assistant Professor of Biosystems and Agricultural Engineering at MSU, and manager of the AD facility. “We avoid temperature shock to the digester by preheating the feedstock with captured heat from the CHP and from the warm effluent from the dewatering system, but in the winter, the preheated feedstock going to the digester is noticeably colder than in other months. We also noticed that, because the hauling contractor bringing us the fruits and vegetables uses a compactor, the weights and volumes were reduced due to the compaction.”
MSU solicited design-build-operate bids for the AD system based on its specifications in late 2012. As part of the submittal, technology providers were required to estimate operations and maintenance (O&M) costs. The initial estimates ranged from $35,000 to $107,000 annually, with a mean estimate of $40,000. The actual O&M cost to MSU in 2014 was $215,000, primarily due to much higher labor needs (14 hours/week in the estimate versus 70 hours/week actually expended in 2014 and 55 hours/week in 2015). For example, the same pump is used to feed the digester and to move digestate to dewatering. Rather than run two pumps simultaneously, both processes have to be managed separately, increasing labor requirements.
The low energy output and high O&M costs in 2015 also were related to premature failure of components in the CHP generator. “We found that running a converted 50 Hz European generator on 60 Hz American power created an environment where the engine couldn’t dissipate the heat produced by friction quickly enough,” explains Kirk. “Short spark plug life and unexpected head failures resulted in higher maintenance costs and reduced operating time.”
Problems with the mixing paddle were the third contributor to the high O&M costs. The mixing paddles were not equipped with a swept-back anti-ragging design, causing the mixer shaft to wobble due to buildup of long, stringy material. The paddle shaft bent under the uneven load. “This was not the right mixer for our application, but we’re glad it failed here in the shaft paddles, and not upstream in the mixer gearbox, where repairs would have been much more expensive,” notes Kirk. In addition, the mixer system required twice yearly maintenance, which involve confined space health-and-safety and explosion protection protocols at a cost of $8,000 to $10,000 per maintenance event. MSU is now evaluating replacement of the existing mixer system with a submersible system with anti-ragging blades that need only annual maintenance.
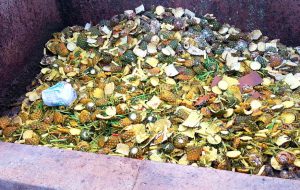
About 900 to 1,000 tons/year of food scraps from the University’s nine dining halls and 23 other food service establishments are diverted to the digester.
Other process design and engineering changes under consideration include a depackaging unit to cut down on contaminants and/or an inline grinder with the new mixing system to improve feedstock particle size, modifying process plumbing to add above-grade cleanouts and eliminate frictional losses in 90-degree pipe elbows, and to insulate the biogas moisture removal cleanup system. MSU also plans to install a nutrient separation system to treat the effluent coming off the digestate dewatering system. “We currently export manure to off campus farms to maintain good agronomic nutrient limits,” he says. “We’d like to export a more concentrated and hence a more valuable nutrient product.”
Lessons Learned
The original system performance goals were to produce 3,000 megawatts (MW) of power annually, meeting 7.3 percent of MSU’s energy transition goals, capture 3,000 MW of thermal energy, divert 14,500 tpy from landfilling and wastewater disposal, reduce MSU’s carbon footprint, and recycle both carbon and nutrients. The AD system is on its way to achieving those goals, with current electrical production at 2,600 MW/yr and diversion at 12,500 tpy. The original plan for the AD system anticipated a 10- to 12-year Return-On-Investment (ROI) due, in part, to assigning a negative value to the digestate (managing it is a cost, not a revenue source). Kirk believes MSU can drop the ROI to under 10 years if it can separate and capture the nutrients in the digestate to make a higher value-added product.
Kirk also offers his observations on lessons learned for others considering similar projects. MSU has been diverting food scraps from the dining halls to the AD system for over two years, and has yet to perfect the logistics for moving them from the cafeterias to the facility and dealing with contamination in the compostables containers. He recommends performing extensive due diligence on outside sources of feedstocks so that potential changes in quantities and qualities can be anticipated and accommodated.
Kirk also expressed concern about the ability of project developers to adequately verify the claims made by technology providers, particularly in the development of accurate O&M pro forma cost estimates. “The most important lesson I’ve learned is Plan For Change,” he notes. “Market forces are constantly rearranging the waste feedstock markets and variability in waste streams is inevitable. I’m also hopeful that the biogas industry will share more operational and financial data in the future to assist other project developers as they plan new projects. However, our system is up and running and contributing to MSU’s Energy Transition Plan, which is what this project was all about.”
Craig Coker is a Senior Editor at BioCycle. He can be reached at ccoker@jgpress.com.