From managing mountains of storm debris to fine-tuning mulch products, several public agencies share lessons learned.
Nora Goldstein
BioCycle April 2013, Vol. 54, No. 4, p. 28
From coast to coast, municipal agencies operate yard trimmings composting facilities. In many cases, they are on the front line when storms hit that leave downed trees and branches in their wake, opening their gates to a flow of feedstocks of all shapes and sizes. On the other end of the processing chain, these facilities are refining their capabilities to transform the incoming wood, storm debris and yard trimmings into high quality mulch and compost products. This article highlights facilities in Pennsylvania and California.
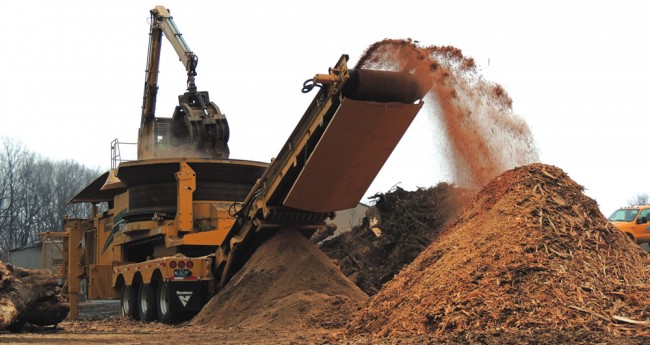
Allentown (PA) has been using a Vermeer tub grinder to manage the tons of storm debris left by Superstorm Sandy and a freak Halloween snowstorm the previous year.
Allentown, Pennsylvania
In late October 2011, Lehigh County, Pennsylvania, like many surrounding regions, had a Halloween trick played on them. A snowstorm dropped a significant amount of wet heavy snow, which built up on trees that had not yet dropped their leaves. The result was many downed trees and branches, along with lengthy power outages. One year later, on October 29, Hurricane Sandy hit, once again causing major tree damage in the region.
The net effect on the City of Allentown, Pennsylvania’s leaf and yard trimmings facility was, and still is, a huge backlog of unprocessed debris, including trees with massive roots, and piles and piles of leaves. “We exhausted the capacity of local farms to take our leaves for mulching, and have quite an accumulation of single ground mulch from wood that we did process,” explains Eric Trobetsky, Operations Manager for the City of Allentown, who oversees the municipal yard trimmings and wood processing facility. “We used to take material to the Lehigh County composting facility for processing, but since it was privatized, there is a fee to tip there.”
In the spring of 2011, Allentown purchased a Vermeer tub grinder with the capacity to “process stumps the size of a Volkswagen Beetle,” says Trobetsky. “We were fortunate to already have that when the freak snowstorm hit in the fall of 2011.” The grinder is rated to process 300 cubic yards (cy) in an 8-hour day, but throughput varies with the size of the material It is equipped with a shield that covers half of the grinding drum. “That is essential for worker safety because when the machine is running, material can fly out of one side of the drum,” he adds. “The shield is placed on that side so that anything coming out is caught. Also, it is easy to do maintenance on the grinder due to the way the tub opens and tilts to a 90° angle. We can access the cutters and tips easily.”
The city makes the grinder available to other municipalities that also are struggling to process stockpiled storm debris. “We need to get an annual permit from the Pennsylvania Department of Transportation to transport it because it is too large to move under a regular license,” explains Trobetsky. “We ask that they pay the costs of an operator to be there for 8 hours and the wear parts to run the machine.”
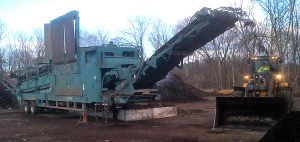
To refine stockpiles of single ground mulch, American Biosoils & Compost (ABC) lent the city a screening plant and Airlift Separator. In turn, ABC purchases the screened mulch at a reduced price.
“We realized that ABC has tremendous resources it can provide to the mulch production and composting communities in terms of equipment, operational expertise and back end markets, and that we needed to make any and all of this available to other composting operations,” explains Ned Foley, a partner in ABC and owner of Two Particular Acres. “The city of Allentown came to our attention through the Pennsylvania Recycling Markets Center. Our initial introductions and discussions were with Allentown’s Solid Waste and Recycling Manager, Ann Saurman, who asked us to develop some solutions with the Operations Manager, Eric Trobetsky. Ann warned us that like all municipal governments, there was and is no money in the budget. In other words don’t come back and tell them this is going to cost a lot of money to solve.”
Foley, Dave Sands of ABC and Trobetsky discussed Allentown’s issues at length and as a result of these discussions, ABC agreed to provide a properly sized screening plant (Powerscreen) and an Airlift Separator (Lane Forest Products) that Allentown would operate with its loaders and personnel. Once properly processed, ABC would purchase the screened material for some of its blended products. “We solved their problem by providing them with the right equipment and some additional revenue and we were able to fill in some of our back end market shortfalls,” notes Foley. “It was and continues to be a win-win.”
San Diego, California
The City of San Diego, California’s Miramar Greenery processes about 100,000 tons/year of green waste, along with source separated commercial and institutional food scraps, unpainted treated wood and particle board, shredded paper and clean, unpainted dry wall. The composting and mulch production facility is located on 74-acres, adjacent to the city’s Miramar Landfill. About 30 percent of incoming material is from the San Diego’s curbside yard trimmings collection program; the remainder is from self-haulers. In 2012, the Greenery received about 3,800 tons of food scraps, and expects that amount to double in 2013.
A variety of mulch and wood chip products are sold, along with compost that is certified under the US Composting Council’s Seal of Testing Assurance program. The majority of incoming green waste is processed in a Diamond Z Tracked 7000 horizontal grinder and then put in windrows for composting. Recently, the Greenery purchased a Diamond Z tub grinder to replace a unit it has had for many years. “The horizontal grinder does an excellent job of just churning out the green waste that comes in, which is 98 percent of what we receive,” says Renee Robertson, Recycling Specialist with the city’s Environmental Services Department, which manages the Greenery. “We use the tub grinder for all wood chip and mulch products. We prefer the tub grinder for those materials because operators can control the feed rate and perfect their abilities to make specialty mulch products. We plan on making 2- and 3-inch mulches with the new grinder.”
The Greenery recently modified its feedstock receiving process to improve product quality control. Landscape self-haul loads are kept completely separate from curbside material and are ground with the tub grinder to make the specialty mulches. The feedstock quality (these loads are generally free of contamination and are mostly wood or leaves), combined with the tub grinder’s ability to make consistent sizing, results in a superior mulch product. “We focus on how to make quality products by controlling the processing of the inputs being received,” notes Robertson.
Nine different recycled landscape products are produced, which are sold in bulk directly from the facility to commercial landscapers, nurseries, government and homeowners. Processed green waste is also used to maintain the city’s active and inactive landfills. San Diego residents can self-load 2 cy of mulch or compost for free. Other equipment used at the facility includes a Wildcat turner and a Komptech Starscreen.