Sensory detection techniques are applied to both source separated and commingled solid wastes to reduce contamination, segregate components, and improve feedstock quality.
Craig Coker
BioCycle January 2018
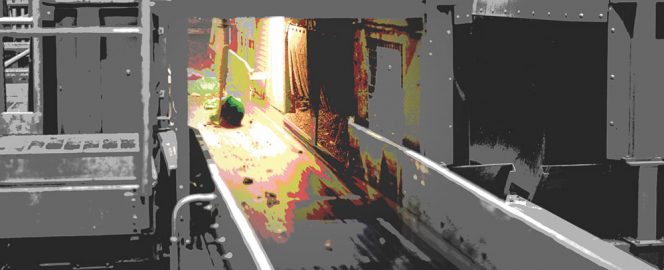
At a central waste sorting facility in Vestfold, Norway, digital image processing is used to distinguish bags of a predefined color, e.g., green bags containing food waste, from others and loose waste. Original photo courtesy of Optibag
Composters and anaerobic digestion facilities handling source separated organic (SSO) solid wastes have been struggling with feedstock contamination issues for many years. Rejecting loads and imposing contamination surcharges has had some effect on improving feedstock quality but many believe there are limits to how effective those pushback approaches can be.
Technology may offer another potential solution to improving feedstock quality in composting and digestion, both by facilitating the sortingoof cocollected SSO and by removing contaminants from mixed waste streams. Traditionally, separating out contaminants has been done using the material “code” — the material property that will be “exploited” to achieve separation, e.g., magnetic attraction — and the removal action “switch” — the machine’s ability to identify that property, e.g., the magnet (see “Separation Code & Switch in Contaminant Removal,” September 2016). Sorting cocollected SSO is more efficiently done by extracting that which is to be composted from that which is not.
Since the 1980s, there has been a significant growth in the field of spectroscopic imaging with computer-aided sensors, such as those used in the medical industry. Imaging is being used in food processing to remove defects and foreign materials to improve the quality of a variety of products. These sensory detection techniques are now being applied to both source separated and commingled solid wastes to reduce contamination, separate components, and improve feedstock quality.
How Imaging Sensors Work
Imaging sensors are based on the science of spectroscopy — the study of energy that is emitted by or reflected from materials and its variation in energy with wavelength. The electromagnetic spectrum (Figure 1) is the range of frequencies (the spectrum) of electromagnetic radiation and their respective wavelengths. Long-wavelength radio waves lie at one end of the spectrum and very short-wavelength gamma radiation waves are at the other end. The human eye detecting the different colors of the visible light spectrum is an example of spectroscopy at work (e.g. is the traffic light red or green?).
Spectroscopic sensors work in different bands of the electromagnetic spectrum corresponding to the nature of the interaction between matter and incoming energy. The sensors record the results of the interaction. For example, a radio picks up (senses) radio waves produced by vibrations of a quartz crystal in response to electrical voltage. An x-ray sensor produces an image based on what parts of matter are transparent to the x-ray emissions (flesh) and what parts are not (bone). A radiation detector picks up decay emissions from radioactive materials. Sensors commonly used in materials handling operate in the x-ray, visible and near-infrared portions of the spectrum.
Spectroscopic data collected by sensors are often represented by an emission spectrum, a plot of the response of the energy-matter interaction as a function of wavelength or frequency as shown in the illustration below. In this example (Figure 2), different emissions spectra of the different glass colors allow glass to be sorted on a moving conveyor belt in a Materials Recovery Facility (MRF).
Recording the emissions spectra of matter bombarded with electromagnetic energy is only part of how these sorting systems work. The other part is the computer-based image management system, which, with the image acquisition method, is known as “machine vision.” This term is defined as the technology and methods used to extract information from an image. The information extracted can be a simple good-part/bad-part signal, or more a complex set of data such as the identity, position and orientation of each object in an image.
Conventional (two-dimensional visible light) imaging is most commonly used in machine vision; other alternatives include multispectral imaging, hyperspectral imaging, imaging various infrared bands, line scan imaging, three-dimensional imaging of surfaces and X-ray imaging. Once the image has been acquired, machine vision software employs various digital image processing techniques to extract the required information, and often make decisions (such as sort/don’t sort) based on the extracted information. Multiple stages of processing are generally used in a sequence that ends up as a desired result. A typical sequence might start with tools such as filters, which modify the image, followed by extraction of objects, then extraction (e.g. measurements, reading of codes) of data from those objects, followed by communicating that data, or comparing it against target values to create and communicate “pass/fail” results.
Applications To Organics Processing
Spectral analysis is currently used in two ways in organics management:
1. Separate out differently colored bags of SSO for further processing in composting or anaerobic digestion facilities
2. Separate out contaminants from the organics fraction of mixed solid waste prior to composting or digestion.
The following case studies highlight current applications in the U.S. and Europe.
Waste Robotics, Delano, Minnesota
Randy’s Sanitation in the Minneapolis metro region of Minnesota owns and operates a dual-purpose MRF. It handles clean source separated recyclables in the day shift, processing about 250 tons/day. On the second shift, the MRF runs in mixed waste mode, where it processes about 150 tons/day, of which 85 tons/day is SSO bagged under the Blue Bag Organics fee-based diversion participation program of its subsidiary, Organix Solutions. (See “Hennepin County Residential Food Scraps Diversion,” May 2017.)
The SSO is contained in bright blue compostable plastic bags and is cocollected with regular trash by Randy’s collection trucks. “We launched this program in some of our collection communities in 2011,” explains Jim Wollschlager, CEO of Organix Solutions and Vice-President of Randy’s Sanitation. “In northern climates like ours, the additional truck traffic of a separate collection route for organics does tremendous damage to asphalt roads in the winter.” The bags are sorted out on the picking line at the front end of the MRF and routed to the Rosemont (MN) composting facility owned by SET Environmental.
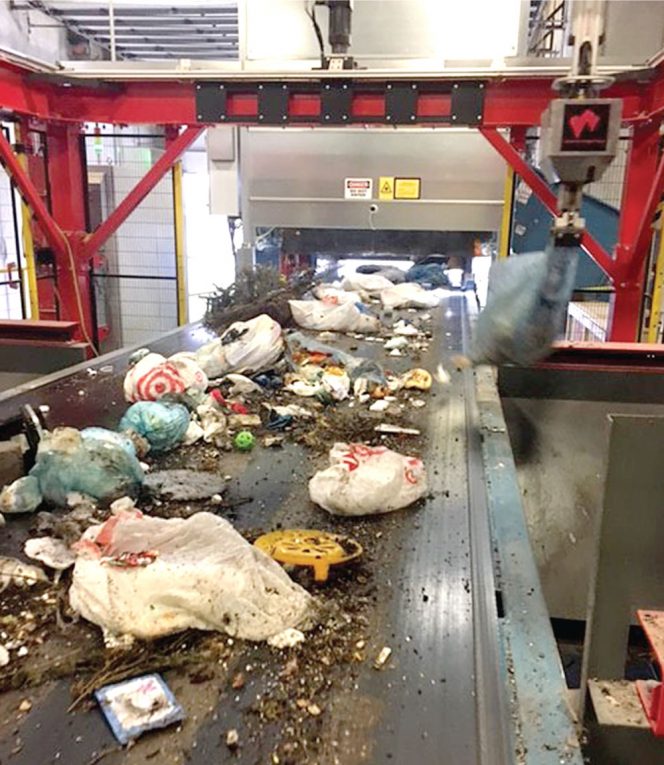
Organix Solutions installed an automated bag sorting system that utilizes color recognition and a robot to recover household organics contained in blue bags. Photo courtesy of Organix Solutions
In May 2017, working with Marathon Equipment Co., Organix Solutions began installation of an automated sorting system made by Waste Robotics of Quebec, Canada. The system was designed to fully automate the bag recovery process and help keep Blue Bag Organics’ diversion program costs down to improve participation rates in the region.
“We designed the robot at Randy’s MRF to work with two-dimensional and three-dimensional color images to recognize a bag from the Blue Bag Organics program,” notes Eric Camirand, Chief Technology Officer at Waste Robotics. The camera image is processed by the computer system at Waste Robotics to recognize the color pixels corresponding to the blue tint of the bags.
“The robot grabs the bags and accelerates it upward at a force of 3g’s, so we are appreciative of the strong tensile strength of the plastic Jim’s company makes the bags from,” adds Nicholas Bélanger, CEO of Waste Robotics. The robot’s “hand” grabs the bags and tosses them into a nearby container over a distance of about 5 feet. “We found that by tossing the bags, rather than having the robot’s arm travel over to the container and drop the bags, we could shave about 250 milliseconds off the time to separate each bag,” he explains. The average duration for a single blink of a human eye is 100 to 400 milliseconds.
Camirand notes that color recognition is only half the battle. “We adopted some of the algorithmic principles used by Google and Facebook so the robot can tell the difference between a blue bag of SSO and a pair of blue jeans,” he says. The robot is capable of picking up 20 to 25 bags/minute from the moving conveyor if the bags weigh less than 30 pounds (it is slower with heavier bags). During a certification trial in December, the robot removed the blue bags with 95 percent accuracy. “We don’t have a human operator downstream of the robot to catch missed bags,” adds Wollschlager, “as that labor cost would offset a portion of the savings we see with the robot.”
As with all new technologies, implementation comes with challenges. “We were relying on a wireless Internet router for the robot to communicate with Waste Robotics,” noted Wollschlager, “but we had some disruptions that compromised system performance and we had to switch to a hard-wired connection.”
Optibag AB, Vestfold, Norway
About 90 miles from Oslo, the capital of Norway, are the municipalities of Bamble, Porsgrunn, Siljan and Skien. Together the four municipalities have about 106,000 inhabitants distributed in 48,700 households, producing about 64,485 tons of solid waste in 2016. About 38 percent of this amount goes to materials recovery, 57 percent to energy recovery and the remaining 5 percent to a landfill. A sorting plant for household waste has been in operation since 2008 and was modernized in 2015. A new technology supplier, Optibag, was chosen to upgrade the plant for sorting food waste and plastic packaging from the waste stream. Last year, the modernized sorting plant processed about 20,300 tons of household waste.
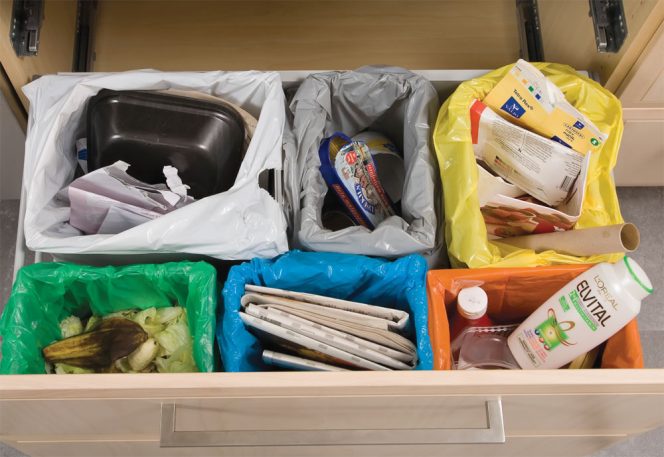
Households serviced by the automated sorting facility in Vestfold presort their waste into different colored bags that are cocollected weekly. Photo courtesy of Optibag
Households are instructed to presort their waste in their homes. Food waste is sorted into a polyethylene green bag; paper, containers and plastic packaging waste go into different colored bags and all residual trash can be put into a bag of any other color. All separated waste fractions are put into the garbage bin and are collected by one single truck weekly. “Households in this area wanted to have a simple solution to sort waste fractions in their homes without increasing the number of collection bins in front of every house (and thus garbage trucks) or having to bring food waste or plastic packaging to a special recycling facility,” explains Jürgen Jacoby, Director of Export Sales for Optibag.
Acceptable material for the food waste bags are fruits and vegetables, pastries, teabags, coffee filters and coffee grounds, shellfish and other fish, meat leftovers, eggshells, used kitchen paper and napkins, nut shells. Not acceptable in the food waste bags are milk and juice cartons, egg cartons, used paper plates and organic garden wastes (grass, leaves or indoor plants).
Collected waste is transported to a central sorting facility where it is separated according to the bag color. The sorting plant itself was supplied by Optibag and consists of a waste receiving hall with a waste bunker. Jurgen explains how it works: “The optical sensor is based on a digital camera that looks down onto the conveyor belt. Digital image processing is used to distinguish bags of the predefined color — green or blue in this case — from others and loose waste. The software is an in-house developed program. The ‘trick’ with this detection technology is that the program needs to learn what bags look like, how they can lie flat on the conveyor, or be an almost round ball when they are filled to maximum, or how some may also be half-covered by a newspaper, for example.
“Once the software has identified a bag, the pusher paddle is activated. The speed of the conveyor belt is fixed to about 4 meters per second (787 feet per minute), as is the distance between the spot where the camera detects the bags. It takes 50 milliseconds for the camera to record the color, and for the software to instruct the paddle to move. The software can tell the paddle the exact time when it should activate and push the bag off the belt. The paddles are driven by a linear motor drive and can push up to four bags per second off the belt. This technology can handle about 9,000 bags/hour for each pusher unit.”
Optibag gives a guarantee that at least 95 percent of all colored bags can be detected and sorted with this technology. The plant is fully automated, operated in a single shift mode by one person; no manual after-sorting is done. The plant is operated by the municipally owned company, Renovasjon i Grenland (RiG), which was founded in 2014 by the four municipalities. RiG has contracted with a partner who operates a 121,254 tons/year anaerobic codigestion plant that takes in the sorted organics along with animal manures. This plant will be featured in a future edition of BioCycle.
Optibag is a Swedish company founded in 1989 and its first sorting plant came online in 1990 to separate black bags containing organic wastes from white bags containing landfilled waste.
Steinert, Olpe, Germany
Composting facilities in Germany adhere to a self-obligatory quality program known as BGK, which includes quality standards (known as RAL) for a standardized and regularly inspected product. There are standards for compost (RAL-GZ-251), for digestate (RAL-GZ-245/246), and for composted sludge products (RAL-GZ-258). There are about 800 composting and anaerobic digestion facilities in Germany and 70 percent of the produced compost is labeled under the RAL-GZ-251 quality label.
According to the RAL-GZ-251 standard, “impurities” larger than 2 mm (about 1/16”) are limited to 0.5 percent on a dry weight basis. If impurities exceed 0.1 percent, then only 25 cm² (about 4 sq. in.) of foreign particles are permitted per liter of fresh substance in fresh and finished compost. This value will be reduced to 15 cm² (about 2.3 sq. in.) per liter beginning on 1 July 2018 (about 65 sq. in. of contaminants per cubic foot of compost).
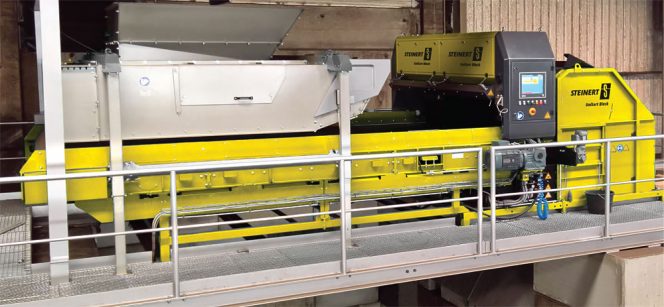
The UniSort Black sorting system installed at a mechanical-biological treatment plant in North Rhine-Westphalia, Germany, has a near infrared (NIR) sensor for recognizing NIR-detectable plastics as well as objects not normally detectable by means of NIR. Photo courtesy of Steinert
The Waste Treatment Technologies (WTT) tunnel reactor composting facility in Olpe, in North Rhine-Westphalia, Germany, composts the organic fraction of mixed solid waste that is processed at a mechanical-biological treatment (MBT) plant run by WTT. The plant uses a Steinert UniSort Black sorting system to remove impurities upstream of the composting reactors. This is a 9-tunnel, 64,000 tons/year facility handling biowaste that has been operational since early 2015. WTT recently upgraded the plant and installed the Steinert system.
The UniSort Black sorting system consists of an NIR (near infrared) sensor for recognizing NIR-detectable plastics as well as objects that are normally not detectable by means of NIR (such as dark-colored and black plastics). Both types of material are sorted out during the same run through. The use of hyperspectral imaging (HSI) technology (see sidebar) enables the UniSort Black to recognize both types of material simultaneously and detect stones and ceramics. “These contaminants do not return a spectral signature in the NIR wavelengths, so the computer interprets that lack of signature to be a signal to reject those materials,” explains Michael Drolet, Solutions Sales Manager for Steinert’s U.S. base in Walton, Kentucky. “Black plastic absorbs all of the NIR energy so it, too, returns no signature. We’ve been able to remove both hard and film black plastic with our system.”
The UniSort system uses compressed air to move the identified contaminant off the conveyor belt. Depending on the application, this technology has a throughput rate of 7 to 11 tons/hour at a conveyor belt working width of 9 feet; the particle sizes captured range from about one-half to 3 inches. Capture efficiency can be as high as 95 percent, but is very dependent on the initial material composition and how evenly distributed the material is on the belt. “The system works best with a single-layer feed,” notes Drolet, “where material coverage is less than 50 percent of the belt surface.”
Steinert is a German company founded in 1889 to make electromagnets to recover iron and coal from steel slag. It has been in the U.S. since 2003.
Craig Coker is a Senior Editor at BioCycle and CEO of Coker Composting and Consulting (www.cokercompost.com) near Roanoke VA. He can be reached at ccoker@jgpress.com.