Cambridge, Ohio retrofitted a portion of its vacuum assisted drying beds into a covered composting facility, processing about 300 dry tons/year of biosolids and wood chips.
Nora Goldstein
BioCycle October 2013, Vol. 54, No. 10, p. 37
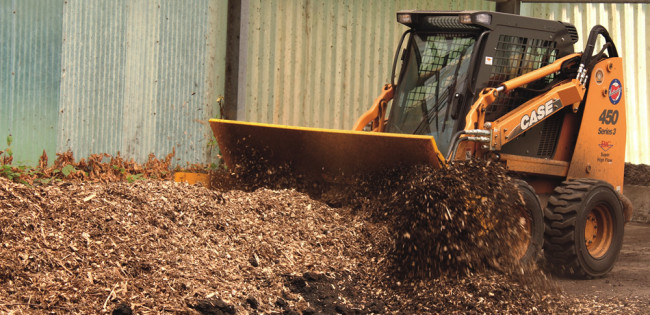
A row of new wood chips is put down, then topped with layers of finished compost and biosolids. Feedstocks are mixed with a Brown Bear aerator attached to a
skid loader.
Hauling and disposal fees were between $50,000 and $100,000/year, and Lou Thornton, Cambridge’s environmental compliance and safety manager, was looking for a more sustainable alternative. He began exploring the option of composting biosolids with green waste, and toured a variety of facilities to see what would work best for Cambridge. “We had stopped using the vacuum assisted drying beds that were in a greenhouse structure, so that area was available for composting,” says Jamiel. “Lou decided that given that space, windrow composting would work out best.”
The city had been struggling with removing solids throughout the treatment facility and reviewed various treatment options. It experimented with a dewatering tube system that resulted in 8 to 10 percent solids, and ultimately opted to install a rotary fan press that produces 19 to 22 percent solids. “We were paying to haul a lot of liquid, and the higher solids content is much more conducive to composting,” he notes. The rotary fan press has been operating since 2010.
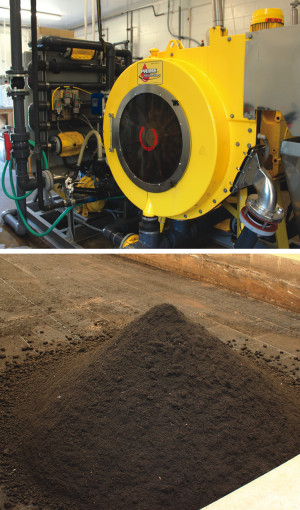
A rotary fan press (top) produces 19 to 22 percent solids (bottom); a portion is composted and the remainder is hauled to an anaerobic digester operated by quasar energy group.
Windrows are 3-feet high, 5-feet wide and 70-feet long. After the pile meets PFRP, it is moved to another bed for curing. Last year, the city stopped composting in November because it was too cold to achieve PFRP in the windrow, and then resumed in the spring of 2013. “We expect we will do the same thing this year,” he says. The city is still developing markets for the compost, and uses some of it for municipal projects. Finished compost is stored at a separate facility.
Less than 10 percent of the 300 dry tons of biosolids generated annually is composted. The remainder is collected by quasar energy group and taken to the company’s anaerobic digestion facility in Zanesville, about 25 miles away. The City of Cambridge hopes to compost more of the biosolids, especially as it develops markets for the end product. “We have seen a huge savings just as a result of the higher percentage of solids in the material,” explains Jamiel. “Having the ability to compost on-site opens up more cost-saving opportunities.”