A New Brunswick farm in need of more digestion capacity decided to utilize an existing storage lagoon. The challenge was finding an appropriate cover.
Peter Gorrie
BioCycle February 2016
LaForge Bioenvironmental presented a tough challenge when it decided to dramatically increase biogas production at its mixed farming operation in St. André, New Brunswick, Canada. Its plan was to convert a concrete lagoon used to store digestate from the existing digester into a second anaerobic digester. The storage lagoon is 200 feet in diameter and 16 feet high. This second digester would continue serving as a storage facility, which meant the level of digestate inside would fluctuate widely during the year. The challenge was finding a cover for the lagoon that could fit these specific operational parameters.
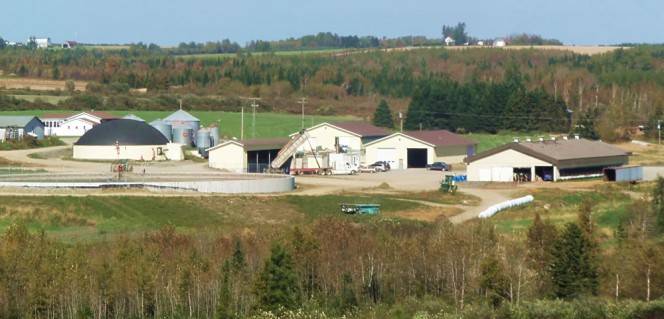
Laforge Bioenvironmental manages a 1,000-acre farm that is home to about 180 head of Holstein dairy cattle, about half of which are milk producers. It also grows silage crops, grains and sugar beets. Photo courtesy of Laforge Bioenvironmental
The 1,000-acre farm is a progressive, family-run operation headed since 1981 by Jacques Laforge, the third generation in the business. The farm is home to about 180 head of Holstein dairy cattle, half of which are milk producers. It also grows silage crops to feed the herd, as well as grains and sugar beets.
Laforge began planning the province’s first on-farm anaerobic digester in 2009 and it went into operation two years later. The feedstock included manure from the farm cattle, but consisted mainly of wastes from nearby potato and poultry processors and a pizza producer. The 65-foot-diameter, 53,000-cubic-foot digester produced enough biogas to fuel a 600-kilowatt generator that fed electricity to the New Brunswick Power grid. But the feedstock supply quickly overwhelmed the digester’s capacity. To compensate, the retention time was reduced from 26 or 27 days to a less efficient 21.
The original biogas project included the large storage lagoon. Using the lagoon as a digester required insulating the structure, and adding heating and mixing equipment along with a cover. The new installation includes a GE Jenbacher gas engine that drives a 1.4-megawatt (MW) generator. The solution to the cover came from Geomembrane Technologies Inc. (GTI), based just two hours from the farm. It proposed a single-membrane, two-ply cover that is held in a rigid dome shape by the pressure of the biogas it contains.
The digester, which went into operation 17 months ago, could produce enough biogas to generate up to 7 MW of electricity. But Laforge has approvals to supply only 1.6 MW to the provincial grid and, in any case, there isn’t enough feedstock to run it at full capacity. The new digester consumes the same materials as the original. The 75 acres of sugar beets are grown as a supplemental input, particularly for periods, such as the Christmas and New Years holidays, when the food processors shut down.
Since it’s not always full, the second digester can continue to double as a storage tank for its digestate. The cycle starts in late fall, when the level is allowed to slowly begin rising to its maximum depth of 15.5 feet. By the following May, the tank and a recently expanded adjacent lagoon, are filled to capacity, just in time for the first application of digestate to fertilize crops. The silage fields are treated immediately after each harvest. This fertilization produces three crops each growing season instead of the region’s typical two. As the digestate is used, the lagoon empties and the level in the digester gradually drops to seven feet. Then, the refilling process begins again.
Digestate from the original digester is moved by gravity pipe to the new digester to finish decomposition. Because the original digester is primarily used to supplement biogas production, there is often energy value in the digestate after it has produced the biogas required. This digestate moves to the new digester to complete decomposition.
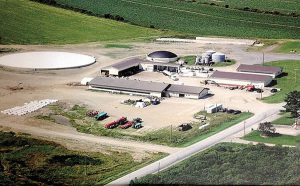
Digestate from the original digester (in center with dome black cover) is moved by gravity pipe to the new digester (on left in background with white cover) to finish decomposition. Photo courtesy of Laforge Bioenvironmental
Cover Options
This process led to unique requirements for the newly converted digester. All heating and mixing equipment must be under the seven-foot level to ensure it is never exposed to biogas. And the cover must be able to remain in place and effective while the digestate level varies.
The original digester, still in operation, has a flexible cover made from rubber that’s slightly heavier than the material used in a tractor tire inner tube. It is covered by netting to prevent overexpansion. But such a system couldn’t be used on the new, much larger tank.
Several alternatives were considered, says Darin Evans, a vice-president of product management at GTI, which is a subsidiary of ADI Group Inc., an environmental technology company based in Fredericton, New Brunswick’s capital city. The first was a floating cover, a design GTI frequently installs, which rests on the surface of the digestate. The cover is subject to a vacuum created by blowers, to eliminate leakage, and biogas is extracted as it is generated. These systems are generally suited to wastewater treatment operations, where the feedstock is liquid and requires little mixing, and the level of material being digested remains relatively constant.
However, the Laforge feedstock contains a significant amount of solids and requires constant mixing. A floating cover could interfere with, and be damaged by, that operation. Most important, floating covers are typically designed for fluctuations of less than four feet and could not handle the eight-foot variation in the Laforge digester.
A second option was an inflatable dual-membrane system that includes an inner membrane to contain the biogas, shielded from the elements and insulated by an outer membrane. The outer membrane is inflated into a dome shape by air blown between the covers. Because the inner membrane doesn’t need to maintain a full dome shape, this system can handle wide variations in biogas pressure. But such covers are intended for digesters not much bigger than 100 feet in diameter, Evans explains. The Laforge tank was far too wide. In addition, its biogas pressure is relatively constant, so the ability to cope with variations wasn’t necessary.
The third possibility was to add a concrete cover. Since the Laforge project involved installation atop an existing tank, this option, requiring reinforcement of the perimeter walls, would have been difficult and expensive, Evans adds. In addition, concrete is highly susceptible to corrosion from the hydrogen sulfide in biogas. The underside of concrete covers usually gets an epoxy coating. But this protection can be weakened as the concrete shifts and contracts, and the coating cracks.
Based on these considerations of the alternatives, Laforge chose the single-membrane cover. “We discussed the options with them,” Evans recalls. “They had done some research on this type of gas-supported dome cover. It was innovative, a bit new, and took some buy-in on the operator’s part. We had limited experience with it. But we did some research and calculations and they said okay.”
The material, manufactured by Solmax, in Varennes, Quebec, is made of two plies of high-density polyethylene that are extruded together. The underside contains carbon black, which helps it to withstand the aggressively corrosive chemicals in biogas. The outer side is white, to reduce heat absorption that not only could overheat the digester but also make the cover expand and contract, opening the possibility of damage and leaks. The white cover results in only 20 percent of the movement that would occur if it were black.
The cover was installed over a six-week period in 2014. The work included two weeks each for preparing the tank, putting the large membrane in place and, then, for maximum strength, fastening it to the outside face of the structure. The work was done with digestate in the tank and producing small amounts of biogas, a toxic substance, so safety precautions were required.
The tank itself was a challenge: Since it was built as an open storage facility the concrete is rough. Refinishing was required in places to ensure a tight seal for the membrane. The circular shape presented additional difficulties for achieving a tight seal. Wrinkles were created in the membrane as it was pulled over the edge of the tank, similar to what happens when a tin can is covered in plastic wrap. “We had to come up with a special detail for the transition from the dome to the connection,” Evans notes.
Much attention was paid to the fastening system, to prevent gas leaks, he adds. After extensive testing, they settled on gaskets that are impervious to biogas, pliable enough to create a tight seal against the concrete but not so soft they would collapse. “It took us a year to get it running smoothly,” says Laforge, 60, who runs the operation with his son Roque and daughter Louise. During the first winter of operation, when biogas production hadn’t yet ramped up, the cover was kept inflated with biogas from the original digester. The lack of heat also meant snow collected on the cover and had to be cleared with hand tools. But over the spring and summer, the digester became fully active, and this winter it has operated well, producing plenty of biogas and generating enough heat to keep the cover free of snow.
The single membrane can be employed as a floating cover, and can be removed, with “a bit of work,” if the tank needs to be drained for major repairs or cleaning, Evans says. The cover design life is targeted for 15 years, but it’s expected to last at least 20, he adds.
Biogas from the original and new digesters can be fed to either generator, or both. The usual practice is to keep the larger plant (the new digester) operating at full capacity, with the smaller, original digester running at a high enough rate to ensure enough electricity is produced to supply the farm and feed the maximum allowed into the grid.
Laforge is now considering what to add to the facility, and how he might use its additional capacity. Since the operation is paid only 10 cents (CDN) per kilowatt-hour of electricity, that wouldn’t be a lucrative option even if Laforge could get permission to sell more to the grid. Upgrading biogas to biomethane looked “interesting” until the recent collapse of oil prices. Adding greenhouses or facilities to dry and cube silage (to reduce spoilage and increase milk production) are possibilities.
Peter Gorrie is a Contributing Editor to BioCycle.