Hometown BioEnergy, LLC, a subsidiary of the Minnesota Municipal Power Agency, has capacity to produce 8 MW of electricity at its anaerobic digestion plant.
Dan Emerson
BioCycle November 2014
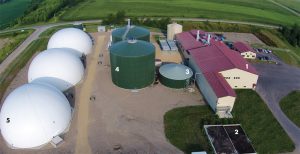
The footprint of the Hometown Bioenergy anaerobic digestion facility is shown at left: (1) Receiving building; (2) Biofilter; (3) Liquid storage tank; (4) CSTR reactors; (5) Biogas storage units.
Since opening last December in the southern Minnesota town of LeSeuer, the Hometown Bioenergy anaerobic digester has been converting agricultural and food wastes into methane used to generate electricity. Hometown BioEnergy, LLC is a subsidiary of the Minnesota Municipal Power Agency (MMPA), which provides power to LeSeuer and 11 other cities in the region. MMPA’s partner, Minneapolis-based Avant Energy, oversaw development and construction and manages the $45 million plant. Expenditures for development, engineering and project management accounted for about $11 million of that total. The project was funded mainly with municipal bonds and received an $8.2 million federal stimulus grant through the U.S. Treasury’s 1603 program (which expired at the end of 2011).
Hometown BioEnergy has a production capacity of 8 megawatts of electricity, generated by four Cummins gas-fueled combined heat and power (CHP) generator sets, according to Kelsey Dillon, Avant’s Vice President of BioPower. Denmark-based Xergi A/S supplied key technology including feedstock pretreatment modules and the plant’s SCADA control system. Xergi provided process design and start-up services for the thermophilic digestion system, which includes two continuously stirred reactors (CSTR).
Organic wastes are sourced from a 60-mile radius. Food processors and farmers bring vegetable processing residuals, manure and agricultural waste such as sweet corn silage to the plant. The waste supply contract terms, including tipping fees charged by Hometown Bioenergy, are based on the energy content of the material, and handling characteristics. “Every feedstock is different,” notes Dillon. “Fats, oils and greases are very energy-dense and relatively easy to handle because they are in liquid form. Sweet corn silage, on the other hand, is quite seasonal, so there are some storage as well as extra processing costs on the front end.”
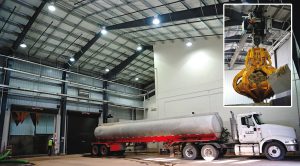
Delivery trucks unload feedstocks, sourced from a 60-mile radius of the plant, inside the receiving and preprocessing building. Solids are moved via an automatic crane (inset).
Situated on a 35-acre site, the plant includes a 22,280 square foot preengineered Butler steel building. The fully enclosed receiving building operates under negative pressure and routes all air to a biofilter for treatment. Delivery trucks unload inside the building. Liquids are placed into an in-floor tank. Solids are received into a dump pit and moved via an automated crane for further size reduction in the plant’s shredder. Processed feedstocks are loaded into feeding modules inside the building that weigh, mix and heat (with recovered heat from the CHP units) the biomass in preparation for the AD process. Ultimately, the mix of liquid and solid material is heated to approximately 125°F in the feeding modules and processed in CSTR reactors for approximately 45 days. Each tank has a holding capacity of 1.6 million gallons.
Since the facility opened, “we have taken a measured approach in bringing these digesters up to speed,” gradually increasing the amount of feedstock processed at one time, Dillon explains. The facility, permitted to process up to 45,000 dry tons of waste, was designed for maximum feedstock flexibility. “The facility has been designed to easily adapt to seasonal variations in waste volume — almost all food processors and agricultural producers have some seasonal variability,” she adds. “The process squeezes every ounce of value possible from the waste products delivered to the plant’s door.”
Feeding The Grid
The Hometown Bioenergy plant was designed for flexibility on the energy production side, with on-site gas storage enabling “dispatch flexibility” to maximize revenue generation, notes Dillon. “We utilize our automated SCADA system and in house lab to manage the feedstock recipe and loading rates to appropriately respond to market conditions.” The on-site storage is comprised of three double-membrane gas holders supplied by Ovivo, with total storage capacity of 27,000 cubic meters. Biogas is sent to the generators during periods of peak electrical demand, 12 to 16 hours a day. “The on-demand electric generation relies heavily on our in-house dispatch activities,” notes Dillon. “Prices in MISO (Midcontinent Independent System Operator) adjust every 5 minutes, so closely monitoring these prices and understanding markets is critical to revenue maximization.” She adds that the system is “highly automated,” which helps keep operational costs low.
After digestion, solids are separated with a screw press. Effluent is available to local farmers as a liquid fertilizer. Dried digestate is used as soil amendment, animal bedding or as a boiler fuel.
Avant Energy is actively working to develop more bioenergy plants. “We think there is really good potential for bioenergy facilities in Minnesota and the Midwest, as well as in other areas where there’s a good ‘appetite’ for renewable energy and government mandates,” says Dillon, citing Minnesota’s requirement that 20 percent of the state’s energy will be provided by renewable sources by 2020 as an example. “We see tremendous opportunities to redefine the term ‘waste’ and believe bioenergy can help utilities, large waste producers, food processors and communities to create value from waste streams and reduce overall energy costs.”
Dan Emerson is a Contributing Editor to BioCycle.