Field trials at two composting facilities evaluated compostable foodservice packaging as a composting feedstock.
Rhodes Yepsen
BioCycle November/December 2018
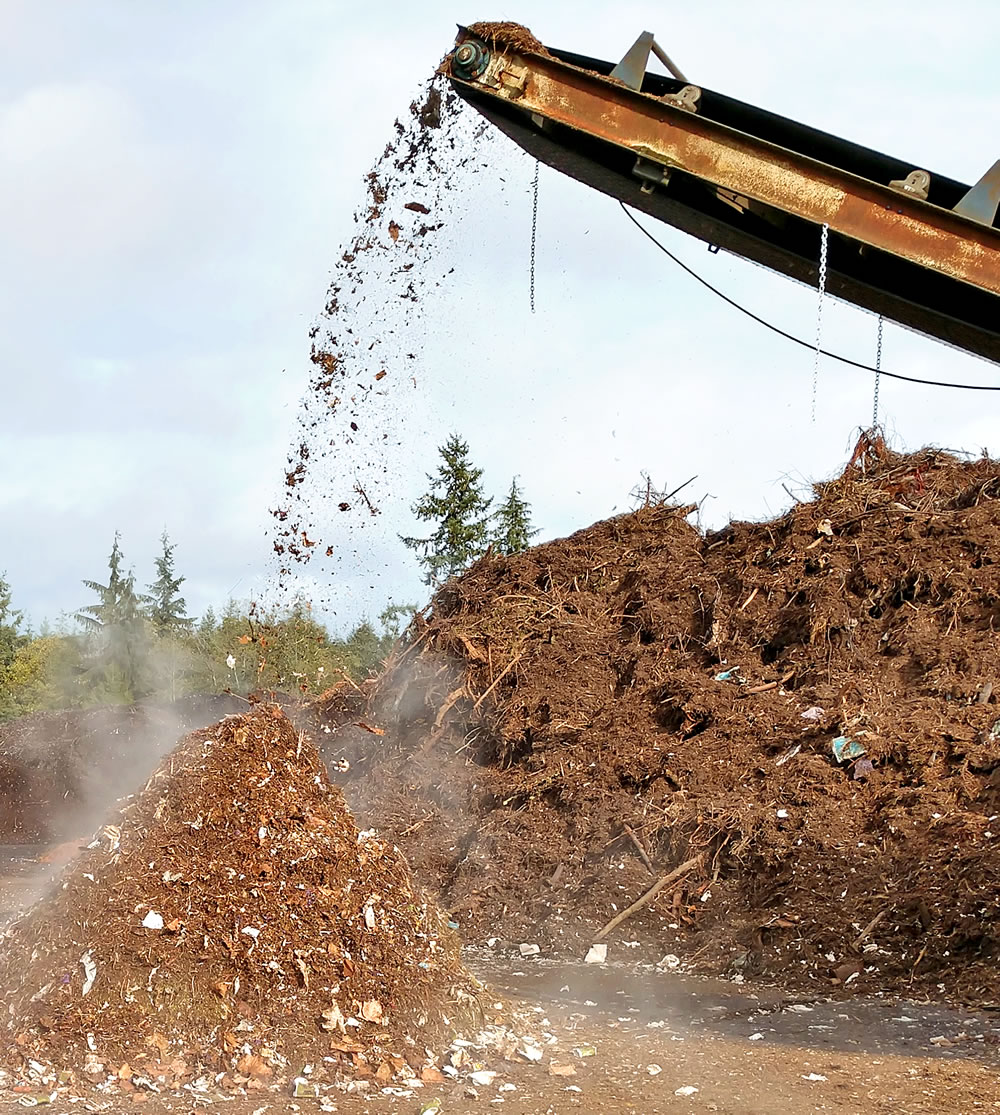
Compostable food service packaging was mixed with other feedstocks, e.g., yard trimmings, and run through a grinder. Photo courtesy of Michele Riggs
The main purpose of compostable products and packaging is to assist in the collection and diversion of food scraps to composting. This is why the Biodegradable Products Institute (BPI) only certifies products and packaging associated with organic waste diversion, with the main categories being foodservice products (cups, cutlery, straws, plates, bowls, takeout containers, etc.), food scrap collection bags and bin liners, and more recently items like coffee pods/capsules.
This has led to a widely held assumption that the only value of compostable products is as a tool for diversion, and that there is no inherent value to the products themselves. To investigate that assumption, the Foodservice Packaging Institute (FPI) and BPI commissioned an in-depth study of compostable packaging as a feedstock itself, compared to traditional inputs like yard trimmings. A field study was designed to answer the following question:
How does compostable foodservice packaging (FSP) compare with other conventional organic waste stream inputs (e.g. yard trimmings, straw, wood shavings, grass, food scraps, etc.) in its contribution to balancing targeted carbon to nitrogen (C:N) ratios, providing nutrients, and acting as a bulking agent in compost feedstocks?
For contribution of carbon, the short answer is that the organic carbon in products tested and certified to the ASTM standards must be converted into carbon dioxide (CO2), demonstrating that the carbon can be used as food for composting microbes, just like the conventional feedstocks a composter accepts. The non-organic carbon components in products are just as important, and lingo-cellulose that isn’t converted into CO2 results in the generation of finished compost to sell.
Compost Manufacturing Alliance (CMA) was contracted to conduct full-scale parallel field tests at two commercial composting facilities located in two geographies, with two of the most common composting methods: aerated static pile (ASP) at Olympic Organics (Washington state) and open windrow at A1 Organics (Colorado). For the field study, piles were super-loaded with compostable products and evaluated for impact on the composting process (e.g., C:N ratio, bulk density, etc.) and quality of the finished compost (e.g., nutrient value, heavy metals, etc.). The results were very positive, showing that on all factors evaluated, the compostable packaging provided the same benefit as traditional carbon and bulking materials found in yard trimmings.
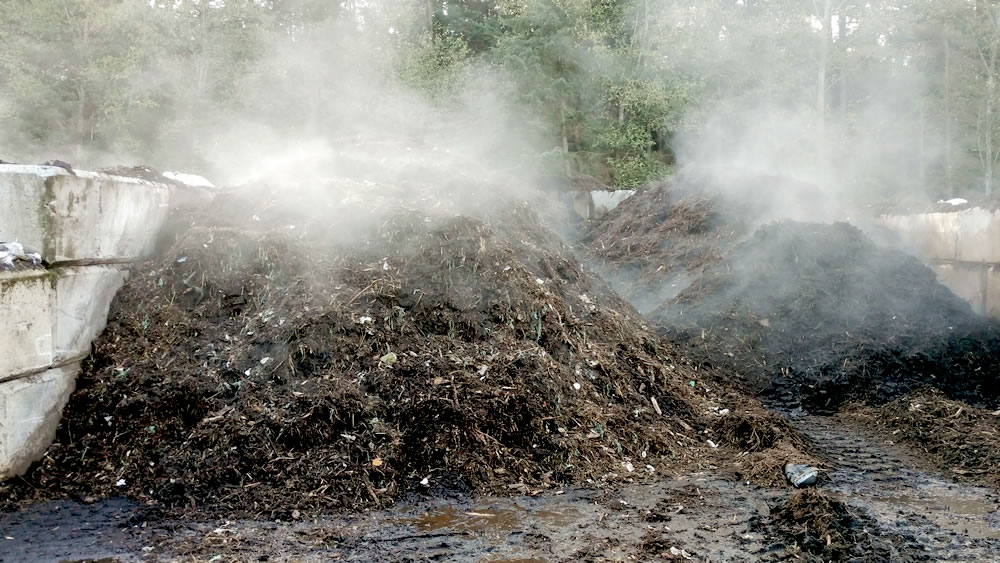
Each sample contained 130 cubic yards (cy) of the mixed material, or 520 cy for all samples combined at each facility. Photo of test piles in aerated bay (capacity of 600 cy) at Olympic Organics, one of the testing sites. Photo courtesy of Michele Riggs
Study Phases
The study consisted of six phases:
• Phase 1: Foodservice Packaging Selection and Analysis. The study design team identified the desired mix of FSP, looking at proportions of substrates that were reflective of real-world operational observations. Each foodservice item type was independently tested for carbon availability to ensure minimum feedstock preparation targets were met. Selected compostable FSP, and the proportion of each utilized in the trials, are shown in Table 1.
• Phase 2: Feedstock Preparation. Products were then mixed, ground, and incorporated into test piles and windrows using each site’s normal feedstock preparation protocols. Each test pile or windrow was divided into four sections: two control samples created from the sites’ seasonal recipes and two test samples using compostable foodservice packaging. The test samples incorporated the FSP mix at rates of 15 and 30 percent of the total recipe, displacing that amount of the facilities’ customary yard trimmings used as bulking agent and carbon source.
Each sample contained 130 cubic yards (cy) of the mixed material, or 520 cy for all samples combined at each facility. Both project sites used pile sizes typical of full-scale (vs. pilot-scale) operations. An ASP bay at Olympic Organics holds 600 cy (the same size as the four collective samples were processed in), and windrow piles at A1 Organics can vary between 100 to 1,000 cy.
• Phase 3: Preprocess Sampling and Analysis. Samples of all control and test samples were tested by an independent laboratory using Test Method for the Examination of Composting and Compost (TMECC) methods for target parameters including bulk density, moisture, organic carbon, nitrogen and the carbon-to-nitrogen ratio.
• Phase 4: Active Composting and Monitoring. The samples were in active composting for 45 days in ASP and 90 days in windrow per those facilities’ normal operations. Both sites extended their active composting process for an additional 21 days beyond their normal timeframes, with adjusted moisture and temperature profiles, to allow the compostable products to disintegrate further.
• Phase 5: Postprocess Sampling and Analysis. After processing, finished compost samples were tested by an independent soil testing laboratory using TMECC methods for pertinent compost characteristics including pH, nutrient content, organic matter, and moisture content, according to Seal of Testing Approval (STA) standards.
• Phase 6: Reporting and Review. A draft of this study report and its findings were reviewed by industry experts including members of the United States Composting Council (USCC) and BioCycle.
Study Findings
The results of the analyses performed before, during, and after active composting provide evidence that compostable FSP at both the 15 percent and 30 percent loading rates did not affect the balance of C:N ratios, nutrient levels, moisture content, or porosity in the feedstock mix or finished compost at these two facilities. Further, compostable FSP performed as an adequate bulking agent compared to wood and other traditional feedstocks used in compost production.
Adding significant levels of diverse FSP to feedstocks did not appear to change the quality of the finished product positively or negatively, and it appeared to perform as well as traditional feedstocks used in compost production.
Given these findings, compost manufacturing facility operators may take a different view on the value of compostable foodservice packaging itself, in addition to the added benefit of bringing in food scraps. This is especially significant in areas where composters are purchasing traditional bulking agents and carbon sources (or where these materials are seasonally scarce).
The full 52-page report — Field Study: Foodservice Packaging as Compost Facility Feedstock — is available for a free download, and includes extensive data, including figures showing feedstock characteristics, processing info and finished compost analysis comparing the control piles (without compostable products) with those that had large volumes of compostable products.
Rhodes Yepsen is Executive Director of BPI, which is North America’s leading certifier of compostable products and packaging, and can be reached at exec.dir@bpiworld.org.