Top: Aeration pad construction, food waste awaiting processing, and compost screening (left to right) at Salinas Valley Recycles’ (SVR) new composting facility. Photos courtesy of SVR.
Nora Goldstein
The Salinas Valley Solid Waste Authority (SVSWA), also known as Salinas Valley Recycles (SVR), is a joint powers agency made up of Monterey County (eastern half of the unincorporated county), and the cities of Gonzales, Greenfield, King City, Salinas, and Soledad. Its service area encompasses 2,400 square miles in the central and eastern parts of the county. SVR, like all other jurisdiction in the state of California, is required by SB 1383, the Short-Lived Climate Pollutants Reduction Act, to plan for and execute programs that achieve a 50% reduction in organic waste disposal from 2014 levels by 2020, and a 75% reduction by 2025.
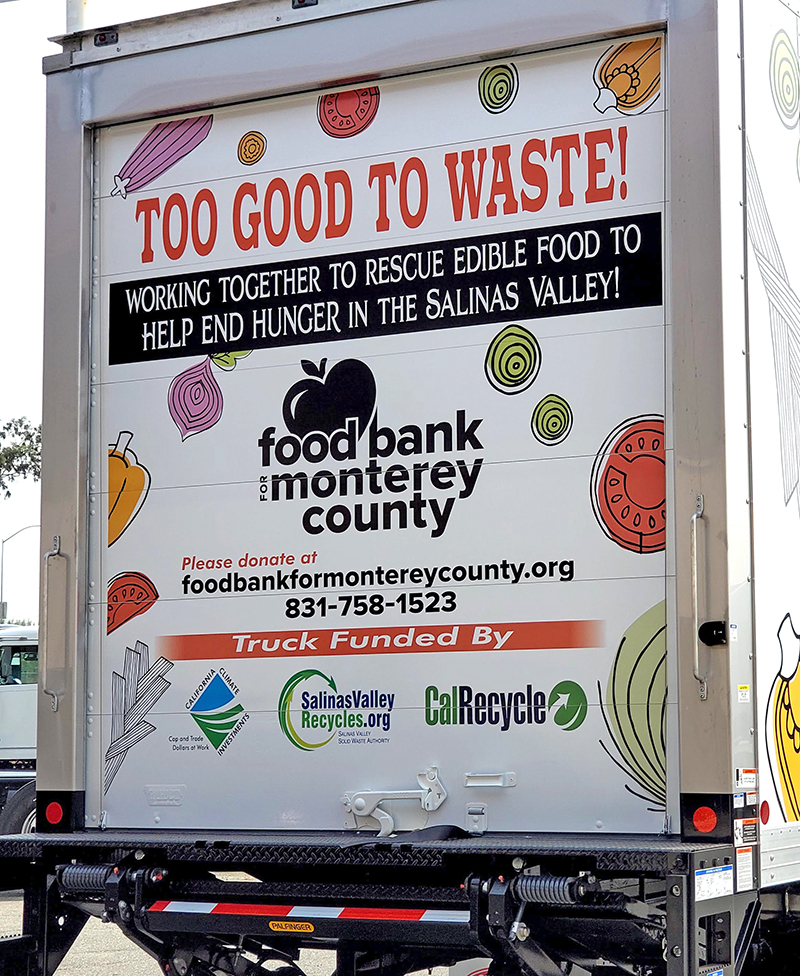
SVR purchased two refrigerated food rescue trucks, each 26-feet long, to help expand the Food Bank for Monterey County’s edible food recovery programs.
CalRecycle’s regulations to implement SB 1383 were adopted in November 2020. Its requirements for implementation and compliance are prescriptive, i.e., there are many, many layers of requirements that cover the “A to Z” of what it takes to capture and recycle organic waste, including education and outreach, collection, processing and utilization of the end products. The law also requires that not less than 20% of edible food that is currently disposed be recovered for human consumption by 2025. Although the regulations were not formally adopted until late 2020, what they require has been on local governments’ radar for a few years. The enforcement provisions of the SB 1383 regulations become effective on January 1, 2022.
Calculating Organics Recycling Capacity
Jurisdictions throughout California are in various phases of compliance with SB 1383. Some have barely started and others are well on their way. SVR is an example of a jurisdiction that began early to lay the groundwork for compliance. “We got started in 2017 with planning our path to compliance,” explains Patrick Mathews, SVR’s General Manager. “One of the first steps was hiring SCS Engineers to research and analyze the current organics programs with the primary objectives to provide an outline of necessary program enhancements, checklist of SB 1383 actions, and a coordinating timeline for SVR to comply with SB 1383 regulations. A critical part was capacity planning, i.e., what was needed for both organics recycling and edible food recovery to achieve 50% reduction, and then 75% reduction. More recently, CalRecycle stipulated that jurisdictions had to consider how we would get to 100% capacity, and include biosolids tonnage in the overall organics disposed numbers. As a result, SCS Engineers updated our planning report, which was submitted to us in early March 2021.”
Sec. 18992.1 of the SB 1383 regulations requires that the following materials have to be included in capacity plans: Food, green waste, landscape and pruning waste, wood, paper products, printing and writing paper, digestate and biosolids. To determine capacity, jurisdictions “must consult with haulers and owners of facilities, operations, and activities that recover organic waste” to do the following:
- Estimate the amount of all organic waste in tons that will be disposed
- Identify available, verifiable existing, new or expanded organics recycling infrastructure capacity (inside and outside of the county)
- Estimate the amount of new or expanded organics recycling facility capacity needed
SVR owns and operates the Johnson Canyon Landfill, the only open landfill in the Salinas Valley. A waste characterization study analyzed the composition of the overall waste landfilled at the facility by recoverability category. It found that about 72% of overall waste is either recoverable or potentially recoverable, of which 40% (nearly two-fifths) is compostable; 16% is recyclable, 5% is recoverable construction and demolition debris, and 12% is potentially recoverable.
A modeling exercise was performed by SCS Engineers to estimate the quantity of organic material in the waste stream for the SVR service area. SCS used data on the annual tons of waste disposed, recycled and composted, and applied the 2019 SVR waste characterization data to prepare the estimate. In 2019, 176,129 tons of residential and commercial waste were disposed in the service area along with 5,687 tons of biosolids; SCS estimated organic materials disposed are 72,534 tons. Based on projections that accounted for population growth, SB 1383 diversion requirements and projected organics processing capacity required, SCS determined that SVR will need to secure organics processing capacity for about 74,530 additional tons (80,217 tons including biosolids) per year of organics by December 31, 2024. Edible food recovery and food waste prevention may reduce the amount of organics processing capacity needed. SVR will also be adding an additional 50,000 tons of chip and grind activities, which will not be composted on-site.
In 2019, 29,465 tons were composted, of which 87% was residential green waste. Therefore, in the entire SVR service area, a total of 109,682 tons of total organics recycling capacity is needed to accommodate the estimated 72,534 tons of organics and 5,687 tons of biosolids currently landfilled, and the 29,465 tons that were composted in 2019. The SCS report includes assessments of organics processing capacity both within the SVR service territory, and within a 120-mile radius outside of the service area to provide information on available capacity for processing organic materials, including green waste, food scraps, and compostable paper.
Food Waste Streams, Edible Food Recovery
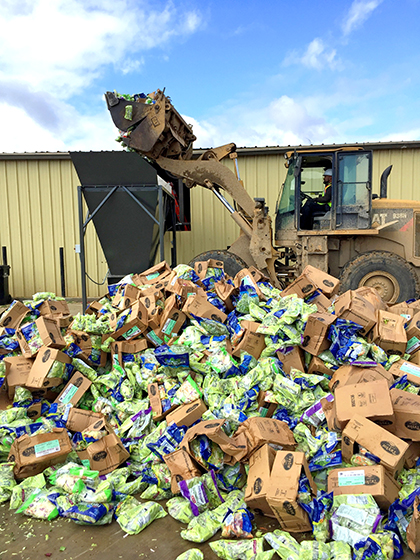
About 75% to 80% of the leafy green vegetables sold in the U.S. are grown and packaged in the Salinas Valley. No longer edible packaged greens are a significant portion of the food waste stream that must be diverted from SVR’s landfill.
SVR’s 2,400 square mile service area includes the “lettuce bowl of the world,” notes Mathews. “About 75% to 80% of the leafy green vegetables sold in the country are grown and packaged in this region. This creates a unique structure when it comes to organics, as prepackaged salads and vegetables that can’t be sold or donated comprise a significant portion of the food waste currently landfilled. It ends up getting disposed for several reasons, including weather delays that prevent shipping to other regions of the country, contracts for the packaged goods being canceled, and/or the packages are past their expiration date,” notes Mathews. “Managing that material became a focus of the facility planning.”
Another consideration is the roughly 200,000 tons/year of clean agricultural culls (post-harvest remnants from parts of the produce not sent to market), which traditionally have been diverted to cattle feed or land applied. “Feed markets are further and further away as the cattle industry has moved from Monterey County into the Central Valley,” he adds. Hauling the culls to the Central Valley could become too expensive, resulting in the need to recycle them in the Salinas Valley. Because this waste stream is not currently disposed, it is not counted in the Authority’s organics recycling capacity calculations.
SVR has initiated a capacity study for edible food recovery. The Food Bank for Monterey County has a very robust recovery and distribution system, says Mandy Brooks, SVR’s Resource Recovery Manager who oversees the organics programs, and education and outreach related to SB 1383. “However, the system has been impacted by the pandemic,” explains Brooks. “The Food Bank originally had 160 food pantry partners and with COVID, that has shrunk to 60, which limits accessibility for food distribution. At the same time demand for its services increased by 60%. In terms of food recovery infrastructure, SVR purchased two refrigerated food rescue trucks, each 26-feet long, to expand the Food Bank’s recovery efforts. We received a partial grant to purchase the first truck and fully funded the purchase of the second truck with agency money. One missing piece of the edible food recovery initiatives is capturing prepared food, which needs to be repackaged and distributed immediately.”
Increasing Composting Capacity
SVR has had a green waste processing site at the Johnson County Landfill for a number of years that primarily served as a “chip and grind” facility with some composting. It was permitted to have 26,000 tons of material on site at any given time. Anticipating the need for increased composting capacity, SVR applied for a CalRecycle Organics Grant for construction of an aerated static pile (ASP) facility at its existing site to process green waste, food waste and soiled paper. “The system is designed for 75,000 tons/year, in part because that is the limit we can process under our Monterey Bay Air Resources District (MBARD) permit,” explains Brian Kennedy, SVR’s Engineering and Environmental Compliance Manager. “It is a site-wide permit that includes other emissions such as the landfill gas flare and landfill cells. MBARD calculated an emissions factor and arrived at 75,000 tons/year for the composting facility. Under the air permit, we are required to have a 6-inch biocover on the aerated piles and are allowed 10 days to process stockpiles of green waste. All food waste must be processed within 24 hours.”
Currently, the composting facility receives about 40,000 tons/year of green waste and wood, along with vegetable waste that needs to be depackaged. Brooks estimates food waste represents less than 10% of what is currently received. “We foresee getting about 15,000 tons/year of agricultural food waste that would need to be processed through our depackaging system,” she says. “SVR just started a pilot-scale commercial food waste collection program in the southern part of our service area. Several restaurants and small grocery stores are participating at this time. We also are working on the rollout of our residential food waste collection.” Mathews projects that the facility will be processing close to 50,000 tons by the end of this fiscal year, which is “well within what is required to meet the 50% reduction in organic waste disposal.”
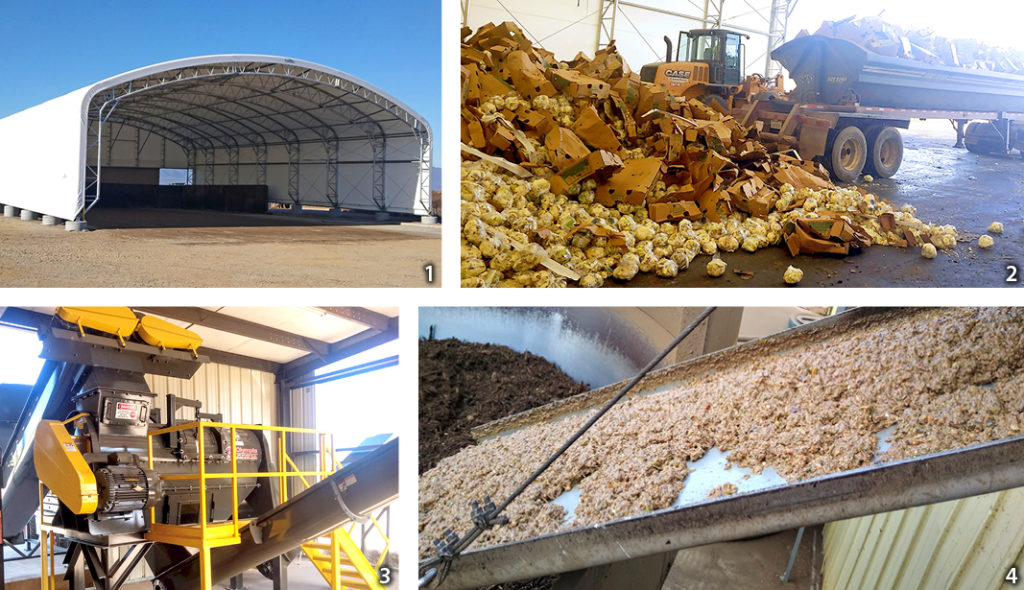
A 7,500 sq. ft. fabric structure (1) houses the tip floor (2) and feed hopper for the Scott Turbo Separator. Slurried food waste is conveyed to a mixer to be combined with ground green waste (4, 5). All photos courtesy of SVR.
SVR received a $1.4 million grant from CalRecycle to help cover the cost of the composting and food waste preprocessing infrastructure, which had to be designed to accommodate the packaged salad greens and vegetables. A Scott Equipment Turbo Separator was installed to process the packaged food waste about a year before the new composting facility was operating to pilot test use of the slurry as a feedstock for codigestion at a wastewater treatment plant. “The pilot proved the concept of codigestion, but the facility was too far away and hauling was expensive,” notes Mathews. “But we will continue to evaluate that option.” The depackager is located in an old machine shop; the food waste receiving area and feed hopper for the depackager are in a new 7,500 sq. ft. fabric building.
The composting facility came on line in June 2020. SVR procured the aeration system and design for the ASP from Green Mountain Technologies. Authority staff, led by Kennedy, did the installation of the aeration system and composting pad. “We had originally planned on having aeration pipes on a lime treated surface, but after geotechnical investigation we determined that the working surface met the permeability requirements of the state of California as is, so there was no need for further treatment,” explains Kennedy. “Knowing that the preferred ASP method is to have subgrade pipes but not having anywhere close to the budget needed to pour an acre of concrete, we worked with Green Mountain on an alternative design where we trenched into the native soil, placed our pipes on top of a rebar cage, and then poured concrete in just the trench. We hardened the surface between the pipes with 8 inches of baserock. We may further harden the surfaces between the pipes at some point in the future with either asphalt or even concrete if we have significant performance issues or to extend the life of the pad. This design worked for us, but if we had the budget we would have poured a continuous pad over the pipes.”
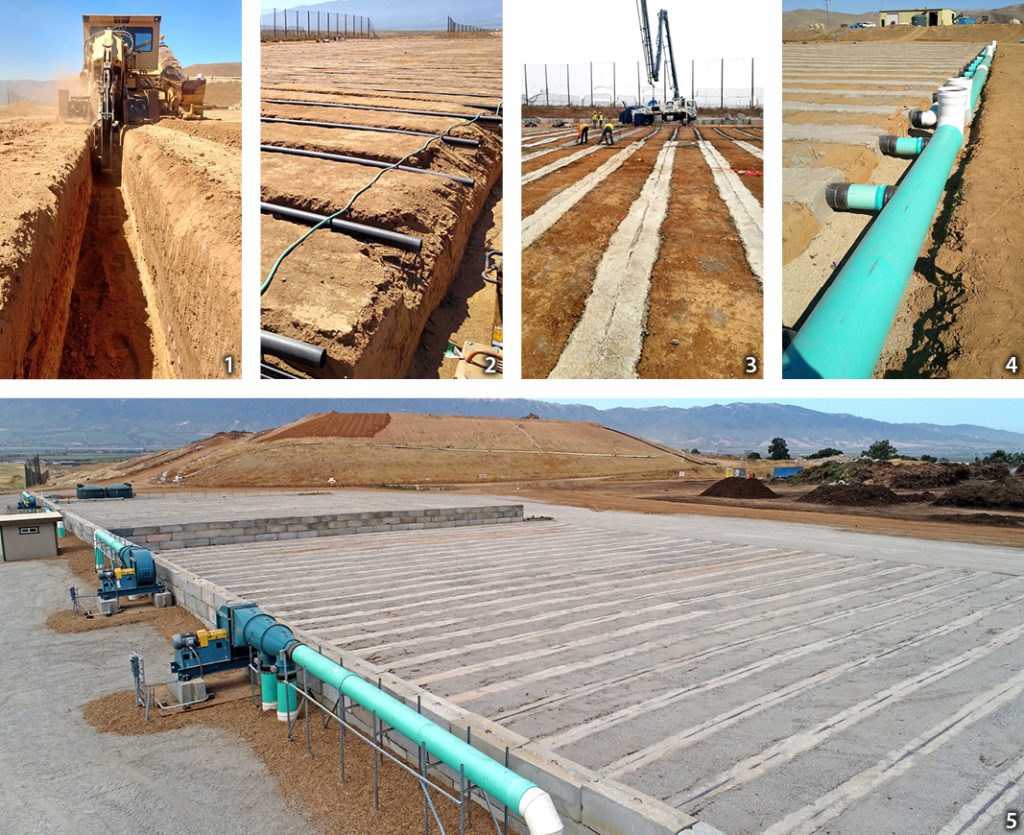
Installation of the SVR aeration system and composting pad involved: (1) Dig trenches into the native soil; (2) Lay pipes on top of rebar cage; (3) Pour concrete in trenches; (4) Connect Green Mountain Technologies aeration system; (5) Harden surface between pipes with bedrock.
Total facility costs were $2.5 million. SVR has a contract with Vision Recycling, an organics recycling company based in Fremont, California, to operate the composting facility. Vision Recycling uses its equipment for materials handling, grinding and screening (anything that is mobile, notes Mathews). It is also responsible for marketing the compost and mulch. SVR operates the food waste receiving and depackaging portion of the facility.
Slurried food waste is mixed with ground green waste in a twin-auger agricultural mixer prior to composting. The ASP system is operated in a positive aeration mode with the biocovers. The active composting phase is 42 days, with aeration shifting between low and high airflow rates. Curing time is typically between 30 to 90 days, and sometimes up to 6 months.
In terms of compost markets, Brooks sees potential in utilizing compost on ranchland in Monterey County. “There are over one million acres of ranchland in the county,” she says. “We hope to become part of projects that are measuring the benefit of compost use for carbon sequestration. Much of the agriculture in the Salinas Valley is industrial farming, especially with the row crops. There is a hesitancy to use compost made with food waste due to stringent food safety requirements with these large growers, but that doesn’t seem to be the case for smaller growers, including nurseries, orchards and vineyards.”
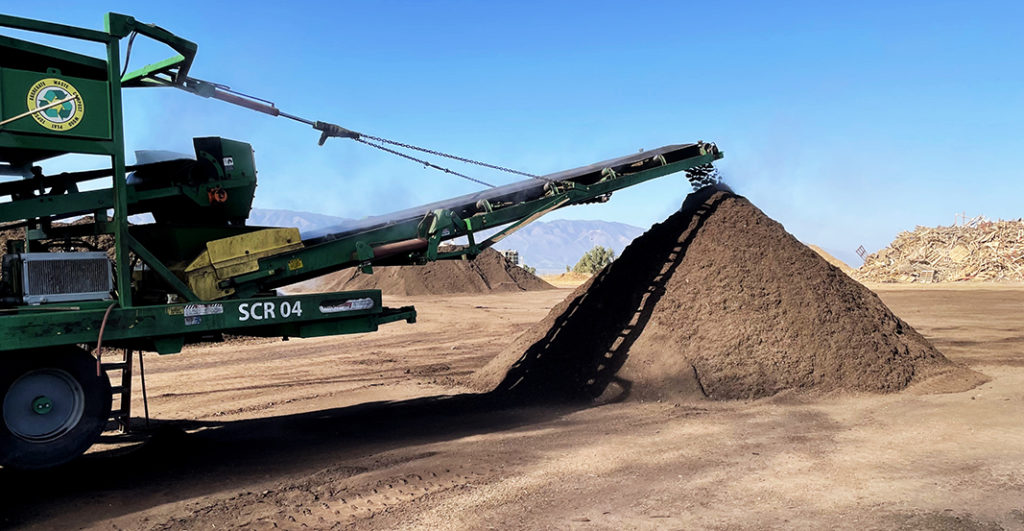
Vision Recycling is the contract operator for SVR’s composting facility, which includes compost marketing.
The Many Elements Of SB 1383
The SCS report lists many of the other elements that SVR needs to address on its SB 1383 compliance journey, including the administrative fee schedule to accommodate the Authority’s Member Agency’s new fees for SB 1383 implementation, agreements with collection service providers, development of ordinances for compliance, contamination monitoring, food waste prevention programs — and the list goes on, including procurement requirements for recycled organics (e.g., compost, mulch, biogas). SCS calculated the quantities each Member Agency is required to procure through 2025. Compliance with the procurement requirements starts on January 1, 2022.
“I feel like we are in a really good place with SB 1383 compliance because of our preplanning,” explains Brooks. “It doesn’t feel like we are in panic mode. Brian has been working night and day since 2017 on the air, water and solid waste permitting and organics recycling infrastructure. We all feel like we’ve hit the mark in terms of where we need to be with SB 1383 at this moment.”