Top: Tyler Miller (left) and Pierce Louis (right) cofounded Dirt Hugger in 2010.
Nora Goldstein
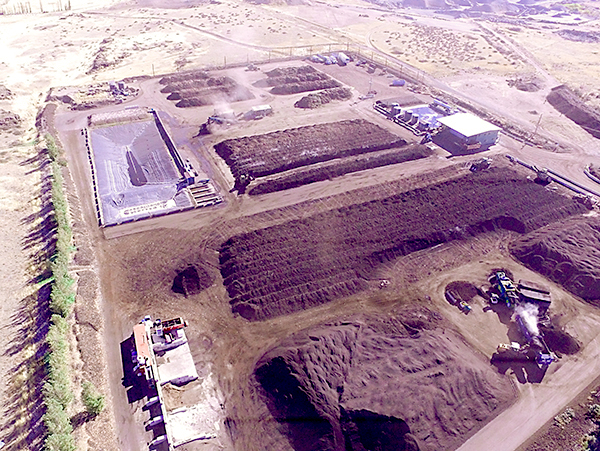
Newly expanded Dirt Hugger source separated organics composting facility in Dallesport, Washington. Photos courtesy of Dirt Hugger
Dirt Hugger was founded in 2010 by Pierce Louis and Tyler Miller in The Dalles, Oregon, close to Hood River in the Columbia River Gorge. Louis and Miller had read a study commissioned by Tri-Counties Recycling (a collaborative government organization) to assess and develop options regarding organic materials management in the Columbia Gorge region. The assessment determined that no local capacity was available to process them.
As told in a 2012 BioCycle article, in response to this study, “Louis and Miller quit their day jobs in the aerospace industry and set up a pilot project in Miller’s yard. From studying the industry, they realized they lacked both startup capital and large feedstock volumes, leading them to create a business model based on small-scale processing in a rural environment. This model required relatively little capital and could function at smaller volumes versus existing urban processing sites the two had visited.”
The entrepreneurs successfully won four grants totaling $65,000, took six months to complete the permitting process, incorporated as Dirt Hugger in March 2010 and started accepting feedstocks. The composting site in The Dalles, previously a lumber mill, had a 1-acre paved pad that met the Oregon Department of Environmental Quality’s regulations for a permitted facility. Incoming feedstocks were stored on the compost pad, and a Case 621D front-end loader was used to turn the piles. Dirt Hugger transitioned to aerated static pile composting for the active curing phase in late 2011.
“Our original vision in 2010 was to open lots of 10,000 tons/year facilities close to where source separated organics were generated and where end markets existed for the compost,” recalls Louis. “It was sort of the Starbucks approach to composting facility development. But we quickly learned that given capital costs and permitting challenges, opening smaller sites was not a viable business plan. Tyler and I decided structurally, we needed to go bigger with one site. To put it simply, you are paying an operator the same whether that person is using a 3 cubic yard (cy) bucket or a 6 cy bucket.”
New Facility, Recent Expansion
In 2014, Dirt Hugger transitioned to a new composting facility in Dallesport, Washington, 7 minutes away (across the Columbia River) from its original site. The operation was forced to move to make room for development of an industrial park. At the time, Dirt Hugger was composting 10,000 to 15,000 tons/year of mixed residential yard debris and food scraps, commercial food waste, fruit and fruit processing waste, and liquid brewing feedstocks from the Columbia River Gorge region. The new 9-acre site would initially house a 26,000 tons/year facility. Designed in conjunction with Green Mountain Technologies, it featured a half-acre in-floor aeration system capable of positive/negative and reversing aeration. Stage One composting was designed to take 14 to 21 days in either windrows (average volume intake) or mass bed ASP (peak volume intake); Stage Two was turned windrow curing on 4.5 acres of cement-stabilized soil.
The total cost for the new site was $400,000, which included grading, and installation of high and low aeration leachate ponds, the aeration pad, and power and water systems. About $300,000 of that cost was financed by bank loans. Dirt Hugger also utilized three grants (both state and federal) totaling $85,000.
From the get go, Louis and Miller designed the site with the intention of expanding it. For example, it installed piping for adding water to piles, and wired a future area for electricity. And, in 2020, it pulled the trigger, building out 4 more acres of the site (total of 8 aeration zones) and mostly operating in negative aeration mode with two biofilters — excepting when turning the mass bed piles with its elevating face turners. Composting capacity increased to 62,700 tons/year. Louis said they had wanted to increase its capacity to 100,000 tons/year, but were limited by Washington state’s air quality regulations.
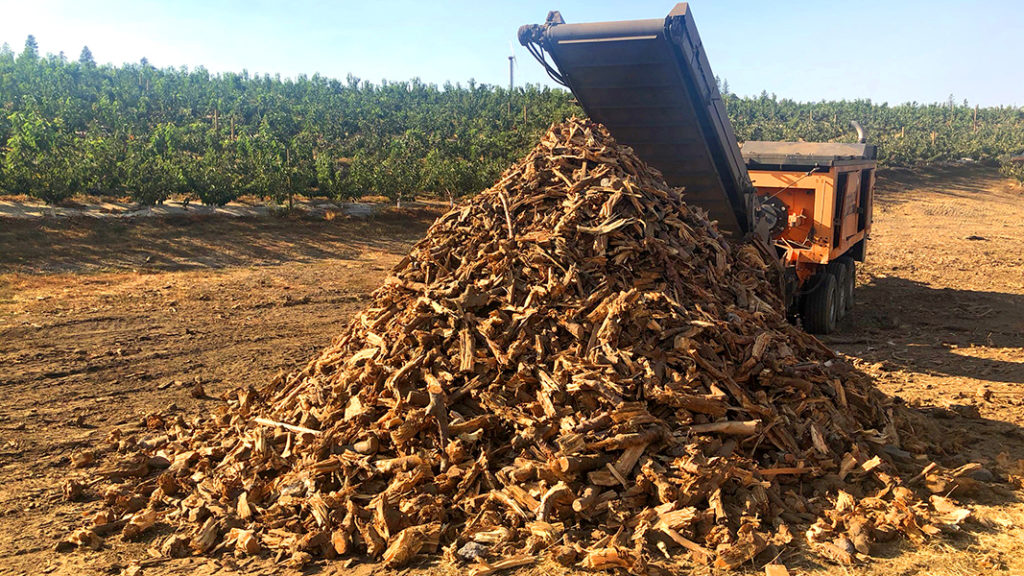
Dirt Hugger offers orchard debris shredding services with a mobile grinder to help minimize the practice of orchard burning.
“Tyler and I were noting recently that going from one to two in terms of growth is a lot easier than going from zero to one with a new facility,” says Louis. “When we came to Dallesport, we borrowed $300,000 and were in a total panic. This time, we borrowed $1.4 million. The dollar value was much more, but the risk was much lower. We had planned the expansion before we started in Dallesport and having that in our business plan really helped guide us on how to build out the site and manage the flow of materials.” The company currently has 22 employees.
While commercial organics comprise the bulk of material composted by Dirt Hugger, it has been receiving material from a residential program rolled out by the City of Vancouver, Washington in October 2019. The city, its contracted hauler (Waste Connections) and Dirt Hugger collaborated on program design, including collection frequency, containers, and materials allowed. “The overarching focus was on the cleanliness of feedstock,” explains Louis. “That was top of mind for everyone, and so only food scraps and yard debris are allowed. Vancouver opted for every-other-week collection, and use of 65-gallon carts, although households can bump that up to 95 gallons. It’s hard to know exactly how much food waste is in the carts, but we’ve received over 17,000 tons of source separated organics since the program began.”
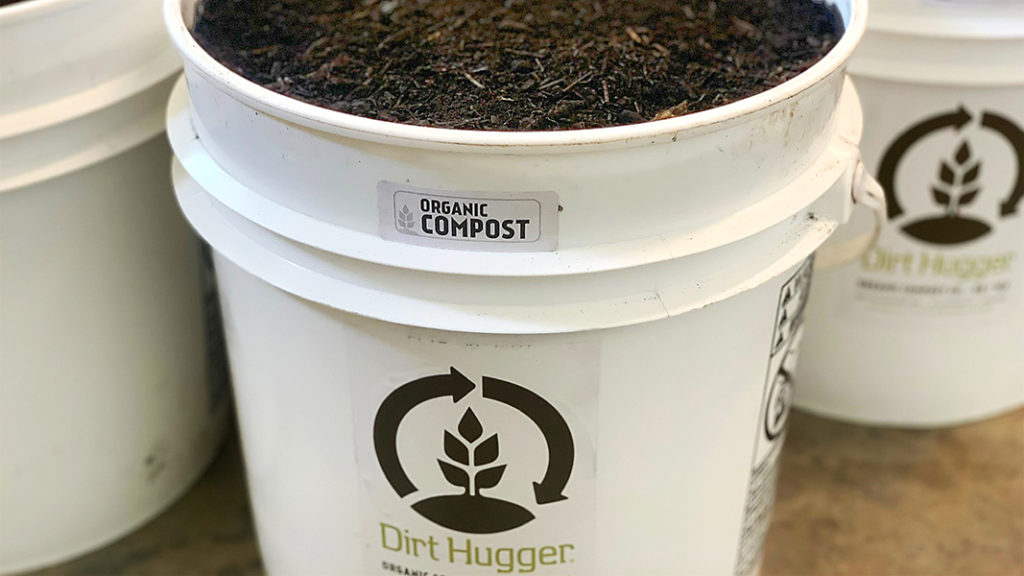
A new innovation in 2020 is selling compost and blends in 5-gallon buckets. Customers pay a refundable $2 deposit for the bucket.
Focus On Product Sales
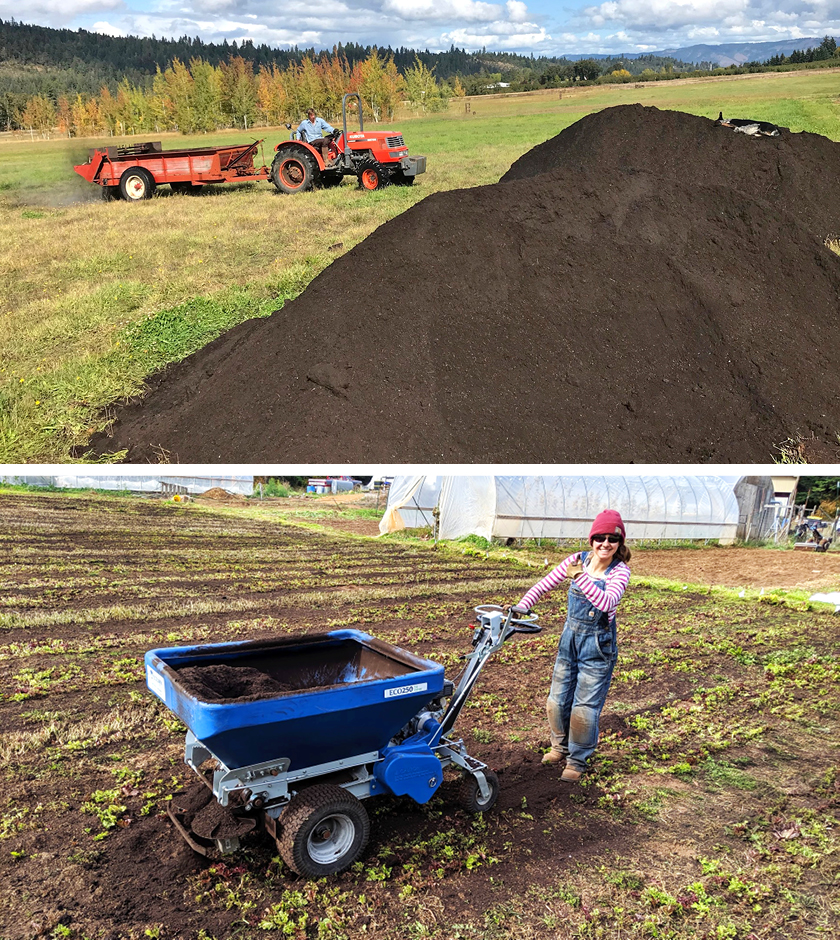
Kuhn-Knight compost spreader (top) is used in the orchards and vineyards. Hand-operated EcoLawn spreader (above) is employed for smaller applications.
From the beginning, Dirt Hugger has received processing residuals from area orchards and vineyards, and sells compost to these markets. More recently, the company added orchard and vineyard compost application services as well as orchard debris shredding services that offset orchard burning. Dirt Hugger purchased a Doppstadt mobile shredder. It uses Kuhn-Knight spreaders to apply the compost, as well as Ecolawn spreaders for smaller applications. “And we have a Roto-Mixer, which works really well for premixing the amendments, especially with vineyard blends,” says Louis. “Gypsum and other amendments are added, so that all amendment application is done in a single pass.”
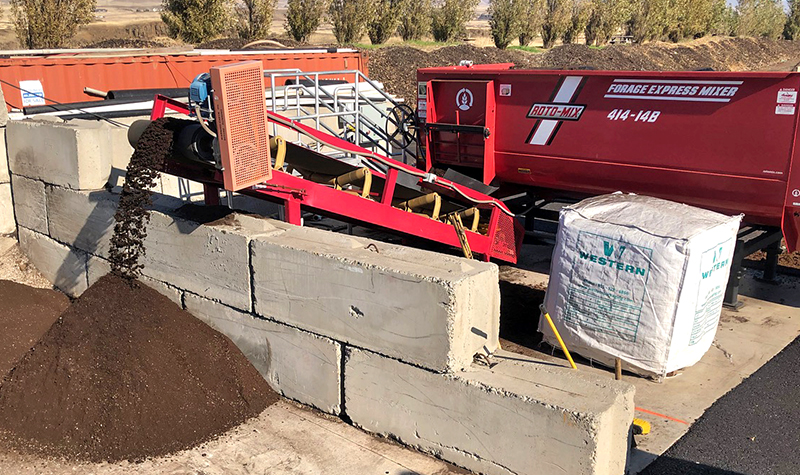
A Roto-Mixer works “really well” for premixing amendments, especially with vineyard blends, says Pierce Louis.
He adds that the company recently signed a contract on a property in Oregon that will be a dedicated retail facility “with employees that focus exclusively on our end products.” It began making compost available in 5-gallon buckets that are “rescued” from area yogurt, ice cream and cherry factories. (Normally the used buckets are landfilled.) “We fill them, and customers pay a $2 deposit which they get back when they return the bucket,” explains Lewis. “The return rate is very high. Nine times out of 10 the customer comes back the next day to get their deposit! We created a label that has all of our products and then we just check the box for the product that is in the bucket.” Dirt Hugger hopes to collaborate with local retailers, e.g., hardware stores, to sell its compost in buckets.