Top: Examples of packaged food waste that typically are received for depackaging. Photo by Bob Spencer
Craig Coker
As Zero Waste initiatives gain traction in the U.S., some companies, including several in the food processing industry, have adopted “Zero-waste-to-landfill” goals and turn to the organics recycling industry to help achieve them. The industrial automation of food processing means foods are prepared, cooked and packaged at rapid speeds, so any sort of glitch in the processing can result in packaged food products that can’t be sold or donated, thus becoming feedstocks for composting or anaerobic digestion.
Food products come packaged in an almost infinite variety of materials, shapes, weights, and densities. Almost all packaging is a contaminant, including (in some views) the ASTM-compliant compostable plastics that are beginning to capture market share. Packaging varies from the expanded polystyrene foam used to make the small sandwich tray to the flexible package pouch containing a juice drink to the ubiquitous film plastic to cover and carry it all.
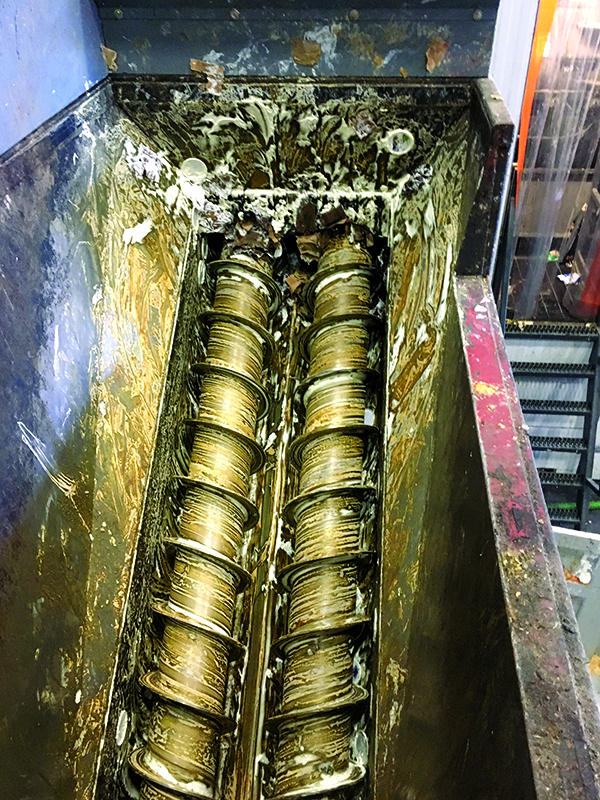
Twin screws in the bottom of the feed hopper of Scott Equipment’s Turbo Separator tear open cardboard boxes and other containers. Photo by Bob Spencer
At the same time, food scraps diversion from landfill programs continues to grow. In 2017, BioCycle counted 148 food scraps diversion programs (both curbside-collected and drop-off) in the U.S. A new BioCycle survey is underway, and preliminary results find a 65% growth in four years (to about 250 programs). Regardless of how well trained people are in source separation of food scraps, the purity of source separated organics (SSO) is always going to be less than 100%, and, in some cases, significantly less. The need to keep contaminants out of the feedstocks for a wet anaerobic digester system and out of compost-based finished product(s), coupled with the costs and difficulties of removing contaminants with human labor, has given rise to machinery designed to do the job. The costs of machine removal are often passed back to the food waste generator instead of being passed along to the compost buyer.
Part I of this article explains the separation principles employed in depackaging. Permitting, and the potential creation of microplastics during processing, are also discussed. Part II provides information on 12 different depackagers available in the U.S. market.
Principles Of Materials Separation
Organics recycling is, in part, a search for order, a processing of heterogeneous materials into purer components. This quest invariably requires some materials be separated from other materials. In its simplest form, separation is a binary process, splitting a feed material into two components. Many facilities depend on the separation of one material from a mixture of many materials. In food waste recycling, this separation process has one input, the heterogeneous feedstock, and two outputs, the extract (the recovered material, e.g. depackaged foods) and the reject (e.g. waste packaging). The video clip (below) from Missouri Organic Recycling shows the slurry from a depackager being fed into a mixer where it is blended with ground yard trimmings prior to composting.
Separation of materials requires identifying the appropriate characteristic (i.e. a “code”) by which separation can be done and optimized. For example, color is an easy characteristic by which to identify and separate materials; magnetic attraction is the characteristic/code for optimizing separation of ferrous metals from ground-up pallets. The key separation codes of all recyclables for processing fall into several common categories: size, weight, density, hardness, magnetism, electrical conductivity, and light refraction. Some materials are separated on the basis of more than one code.
The ability of a machine to identify a code and to perform some function, actively or passively, on that material as a result of that information is called “switching” or separating the material according to that identified code (Vesilind, 1984). For example, a trommel screen uses particle size as the code and screen mesh as the switch, allowing smaller particles to fall through and larger particles to be retained. Another example might be separating colored glass from clear glass, which uses transparency as the separation code (i.e. transparent vs. opaque), and percent light transmittance as the switch.
The metrics used to evaluate separation efficiency are recovery and purity. Recovery is simply the percent recovered from the entire waste stream feed (percent food captured vs. percent not captured). Purity is the percentage of the desired recovered material in the total recovered waste stream (i.e. percent actual food in the recovered materials pile). Food waste depackagers operate in the 90% to 97% recovery and purity range, depending on how much food remains adhered to the packaging after separation.
How Depackagers Work
A food waste depackager can use multiple characteristics and switches. For example, tensile/compressive strength is the code and applied force renders it open as the switch. Hardness, or resistance to force, can be a code, and pressure as a switch opens packages to separate out the packaging and the wasted food. The switches employed by the machines in the market today are variations on applied force, either in a tangential shearing action, a vertically-oriented hammering action, horizontal or vertical pressure through a metal sieve or screen, or some combination thereof.
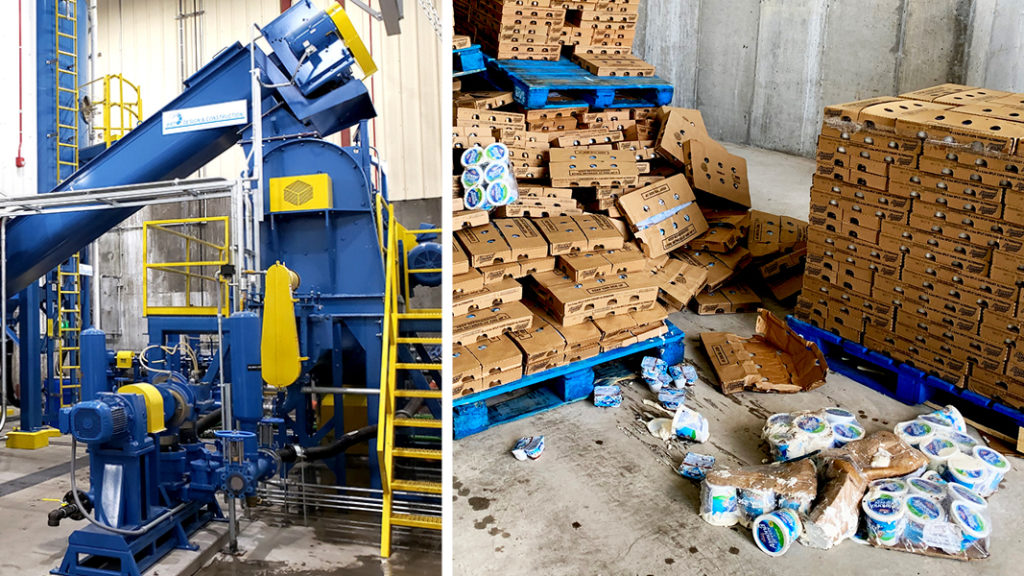
A Scott THOR Turbo Separator was installed by the Oneida-Herkimer Solid Waste Authority (OHSWA) in Utica, New York to process packaged goods from food manufacturers and commercial organics with packaging. The slurry is codigested at an adjacent wastewater treatment plant. Photos courtesy of OHSWA
Drawing from the hammermills common in grinding wood, early depackagers used similar applications of force, but the splintering of the packaging allowed small particles to pass through the sieve/screen. Newer models are designed to separate the packaging with the least amount of applied force needed, through fine adjustments like changing the angle of paddles mounted on a shaft, and to convey that separated packaging out of the machine with the least amount of additional handling.
Permitting Considerations
Composters and anaerobic digestion (AD) facilities wishing to incorporate a depackager into their operations may have to formally request a Minor Permit Modification. However, if the added depackaging capability leads to a significant increase in incoming tonnages or truck traffic to/from the facility, some regulators may insist on a Major Permit Modification, which usually requires a public hearing.
Pennsylvania’s Department of Environmental Protection amended the operating permit of a farm-based digester to allow “the utilization of a depackaging unit(s) to mechanically separate preconsumer and postconsumer food waste from commercial establishments, institutional establishments, or industrial food manufacturing operations, from its packaging, prior to anaerobic digestion” (Goldstein, 2021). Not surprisingly, the permit modification imposes constraints, including operating in an enclosed building, no visible plastic fragments in the food wastes, and quarterly sampling and analysis of 16 different analytes in both the solid and liquid streams.
Formation Of Microplastics And Nanoplastics
The issue of microplastics (defined as plastic particles less than 5 mm or about one-quarter inch in size) getting into the environment is much discussed but consensus on how (or even whether) to address this problem is lacking at present. The U.S. Environmental Protection Agency (EPA) recently published a report looking at the issue of plastic contamination in food wastes (EPA, 2021). The report refers to the growing use of depackagers, drawing heavily from previous BioCycle articles. EPA notes there is very little U.S.-based data on plastic contamination of finished products (either compost or digestates), but they report on anecdotal evidence of produce stickers and other small plastic pieces in composts being reported.
“Degradation of plastics starts every time a product is touched, transported, transferred and then processed,” notes Kevin Pedretti, Business Development Manager for Scott Equipment. “Since all depackaging systems employ some type of mechanical process, the possibility of further size reduction occurs. The question is — if recycling food is a good thing and food typically is packaged in plastics — which plastics are the ’worst offenders‘ in the realm of microplastics. It has been my experience that the #5 polypropylene family is a contributor more than the others. Given the desire to recycle and recover — can a different plastic be used that is less brittle or less likely to shatter when recycling or transporting?”
There has been some testing in Europe for microplastics in depackaged food. According to EPA, “The available international literature reports a wide variation in the level of plastic contamination found in samples of compost and digestate derived from household and commercial organic waste, ranging from 0% to 0.22% by weight. Part of this plastic contamination is microplastic particles (MP), which have been found at levels of 14 to 895 MPs per kilogram (kg) dry weight in compost and digestate. Data on the level of plastic present in the food waste used to generate the products measured in these studies is not reported” (EPA, 2021).
Notes Tony Pickess, Sales Director for Gemidan Ecogi (a depackager manufacturer), “We commission regular independent testing of the substrate ECOGI produces for non-organic content (including plastic). This testing confirms that the substrate is 99.9% free from contamination (plastic). During the development of ECOGI, Gemidan was awarded European Union ‘Environmental Technology‘ certification for process performance outcomes including contamination removal.”
Craig Coker is a Senior Editor at BioCycle CONNECT and a Principal in the firm Coker Composting & Consulting (www.cokercompost.com), near Roanoke VA. He can be reached at ccoker@cokercompost.com.